Customer Company Size
Large Corporate
Region
- Europe
Country
- United Kingdom
Product
- MetaPack Manager
- Supplier Direct
- Ship to Store
- Range Expansion
Tech Stack
- SAP
Implementation Scale
- Enterprise-wide Deployment
Impact Metrics
- Customer Satisfaction
- Brand Awareness
Technology Category
- Platform as a Service (PaaS) - Connectivity Platforms
Applicable Industries
- Retail
- Automotive
Applicable Functions
- Logistics & Transportation
- Sales & Marketing
Use Cases
- Supply Chain Visibility
- Inventory Management
Services
- System Integration
- Software Design & Engineering Services
About The Customer
Halfords is a well-established brand that was founded in 1902. The company operates more than 460 retail stores throughout the UK and ROI, with its head office located in Worcestershire. Halfords offers a comprehensive range of products to consumers interested in automobiles, leisure, cycling, and more. The company's multichannel strategy has grown in combination with the Halfords store network to provide a compelling array of services to meet changing consumer behaviors as online becomes more and more embedded in everyday life. The company's website offers 30,000 product lines, providing a truly comprehensive range to its customers.
The Challenge
Halfords, a company offering 30,000 product lines related to automobiles, leisure, cycling, and more, wanted to keep up with the changing consumer behaviors as online shopping becomes more prevalent. The company aimed to launch a service that allows consumers to order goods online and collect them from a local store at no extra delivery cost. This was in response to the changing shopping habits of their customers who increasingly move between Halfords stores and the brand’s website. The challenge was to implement this without incurring any additional implementation, resource, or cost requirements.
The Solution
Halfords had previously overhauled its ‘direct from supplier’ process by adopting MetaPack’s Supplier Direct solution. Each morning order data is imported from SAP to MetaPack with the click of just one button. Each supplier can then log onto MetaPack through a web interface to see all of their Halfords orders as pre-allocated consignments. MetaPack prints the carrier labels for the supplier and sends collection notices to the appropriate carrier. Both the suppliers’ and Halfords’ customer service teams have full visibility into delivery information. With this process already in place, it was easy for Halfords to add the ‘free delivery to store’ option without any additional implementation, resource or cost requirements.
Operational Impact
Quantitative Benefit
Case Study missing?
Start adding your own!
Register with your work email and create a new case study profile for your business.
Related Case Studies.
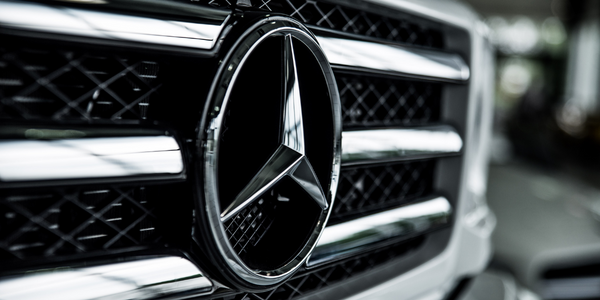
Case Study
Integral Plant Maintenance
Mercedes-Benz and his partner GAZ chose Siemens to be its maintenance partner at a new engine plant in Yaroslavl, Russia. The new plant offers a capacity to manufacture diesel engines for the Russian market, for locally produced Sprinter Classic. In addition to engines for the local market, the Yaroslavl plant will also produce spare parts. Mercedes-Benz Russia and his partner needed a service partner in order to ensure the operation of these lines in a maintenance partnership arrangement. The challenges included coordinating the entire maintenance management operation, in particular inspections, corrective and predictive maintenance activities, and the optimizing spare parts management. Siemens developed a customized maintenance solution that includes all electronic and mechanical maintenance activities (Integral Plant Maintenance).
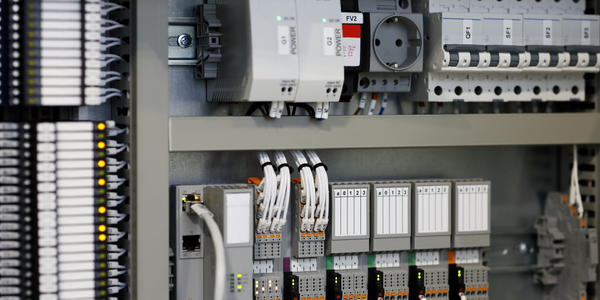
Case Study
Improving Production Line Efficiency with Ethernet Micro RTU Controller
Moxa was asked to provide a connectivity solution for one of the world's leading cosmetics companies. This multinational corporation, with retail presence in 130 countries, 23 global braches, and over 66,000 employees, sought to improve the efficiency of their production process by migrating from manual monitoring to an automatic productivity monitoring system. The production line was being monitored by ABB Real-TPI, a factory information system that offers data collection and analysis to improve plant efficiency. Due to software limitations, the customer needed an OPC server and a corresponding I/O solution to collect data from additional sensor devices for the Real-TPI system. The goal is to enable the factory information system to more thoroughly collect data from every corner of the production line. This will improve its ability to measure Overall Equipment Effectiveness (OEE) and translate into increased production efficiencies. System Requirements • Instant status updates while still consuming minimal bandwidth to relieve strain on limited factory networks • Interoperable with ABB Real-TPI • Small form factor appropriate for deployment where space is scarce • Remote software management and configuration to simplify operations