Applicable Industries
- Cement
- Metals
Applicable Functions
- Maintenance
- Product Research & Development
Use Cases
- Construction Management
- Virtual Prototyping & Product Testing
About The Customer
Nippon Steel Texeng Co., Ltd. is a design-build firm specializing in steel plant construction. The company covers all phases of the process, from plant design and construction to operation management and maintenance. NS-Texeng is a wholly-owned subsidiary of Nippon Steel Corporation, a renowned Japanese steel fabrication company. The company was formed in 2014 through the merger of eight companies, resulting in a diverse mix of CAD software packages. NS-Texeng is headquartered in Chiyoda, Tokyo, Japan, and employs over 11,000 people as of 2019.
The Challenge
Nippon Steel Texeng Co., Ltd., an engineering company specializing in steel plant construction, faced a significant challenge following a merger with multiple companies. Each of these companies used different CAD software packages, resulting in a lack of standardization across the newly formed entity. In 2014, eight companies were integrated into NS-Texeng, leading to the use of six different types of software for 2D CAD. The company recognized the need to unify its CAD software and began a comparison study to identify the most suitable product. Additionally, the 2D CAD software that had been widely used within the company switched to subscription-only licensing, which was expected to significantly increase the budget required to maintain the company’s CAD licenses.
The Solution
After a thorough comparison study, NS-Texeng chose BricsCAD as their preferred CAD software. The decision was based on several key factors. Firstly, BricsCAD facilitated an easy transition from other CAD software, ensuring a smooth integration process. Secondly, BricsCAD offered a comprehensive solution with 2D, 3D, and BIM capabilities, all within a single software product. This feature was a significant advantage for NS-Texeng, as it allowed the company to use all three dimensions in their design process. Lastly, BricsCAD's ongoing development of software that imports 3D laser scans aligned with NS-Texeng's future plans, making it a future-proof solution. The company felt that both entities were looking in the same direction, further solidifying BricsCAD as the ideal choice.
Operational Impact
Case Study missing?
Start adding your own!
Register with your work email and create a new case study profile for your business.
Related Case Studies.
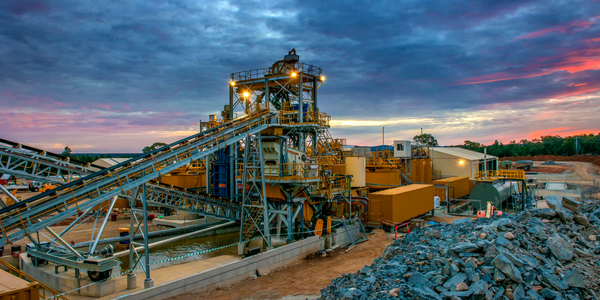
Case Study
Goldcorp: Internet of Things Enables the Mine of the Future
Goldcorp is committed to responsible mining practices and maintaining maximum safety for its workers. At the same time, the firm is constantly exploring ways to improve the efficiency of its operations, extend the life of its assets, and control costs. Goldcorp needed technology that can maximize production efficiency by tracking all mining operations, keep employees safe with remote operations and monitoring of hazardous work areas and control production costs through better asset and site management.
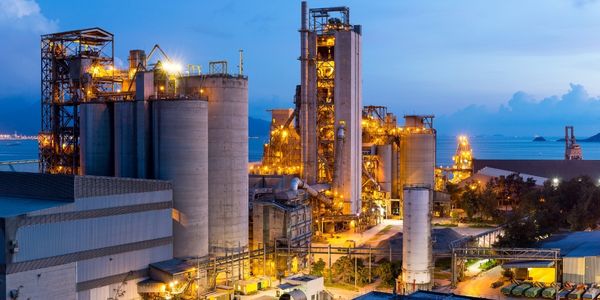
Case Study
System 800xA at Indian Cement Plants
Chettinad Cement recognized that further efficiencies could be achieved in its cement manufacturing process. It looked to investing in comprehensive operational and control technologies to manage and derive productivity and energy efficiency gains from the assets on Line 2, their second plant in India.
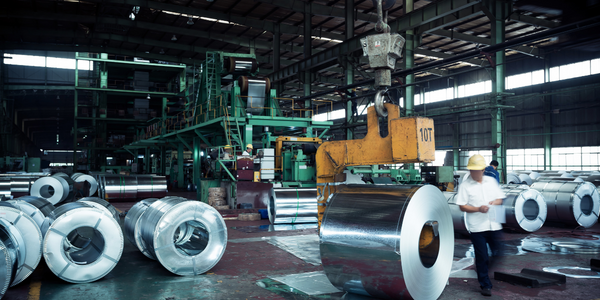
Case Study
KSP Steel Decentralized Control Room
While on-site in Pavlodar, Kazakhstan, the DAQRI team of Business Development and Solutions Architecture personnel worked closely with KSP Steel’s production leadership to understand the steel production process, operational challenges, and worker pain points.
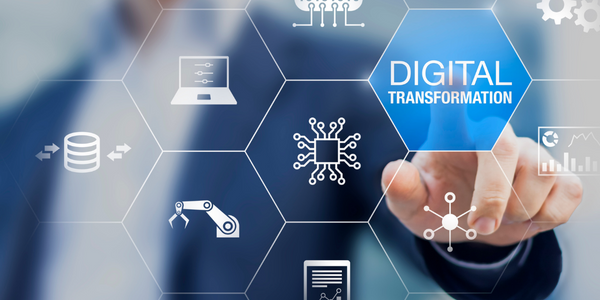
Case Study
Bluescope Steel on Path to Digitally Transform Operations and IT
Increasing competition and fluctuations in the construction market prompted BlueScope Steel to look toward digital transformation of its four businesses, including modern core applications and IT infrastructure. BlueScope needed to modernize its infrastructure and adopt new technologies to improve operations and supply chain efficiency while maintaining and updating an aging application portfolio.
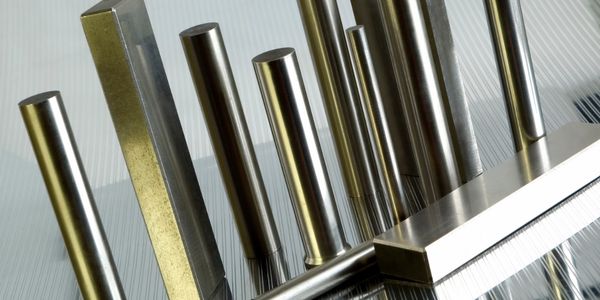
Case Study
RobotStudio Case Study: Benteler Automobiltechnik
Benteler has a small pipe business area for which they produce fuel lines and coolant lines made of aluminum for Porsche and other car manufacturers. One of the problems in production was that when Benteler added new products, production had too much downtime.
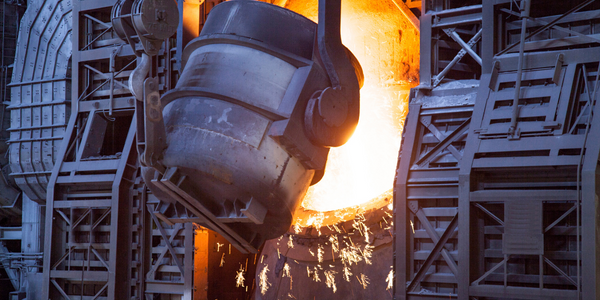
Case Study
Continuous Casting Machines in a Steel Factory
With a very broad range of applications, steel is an important material and has been developed into the most extensive alloy in the engineering world. Since delivering high quality is absolutely crucial for steel plants, ensuring maximum productivity and the best quality production are the keys to competitiveness in the steel industry. Additionally, working conditions in steel factories are not suitable for workers to stay in for long periods of time, so manufactures usually adopt various machines to complete the steel production processes. However, the precision of these machines is often overestimated and the lack of flexibility also makes supervisors unable to adjust operating procedures. A renowned steel factory in Asia planned to improve its Distributed Control System (DCS) of furnaces as well as addressing the problem of insufficient accuracy. However, most well-known international equipment suppliers can not provide a satisfactory solution and local maintenance because the project needed new technologies to more accurately control equipment operations. By implementing Advantech’s automated monitoring and control solution, steel factories can not only improve the manufacturing processes but can also allow users to add additional functions to the existing system so as to make sure the operation runs at high efficiency.