Technology Category
- Sensors - Environmental Sensors
- Sensors - Temperature Sensors
Applicable Industries
- Oil & Gas
- Transportation
Applicable Functions
- Logistics & Transportation
- Product Research & Development
Use Cases
- Time Sensitive Networking
- Vehicle Telematics
Services
- System Integration
About The Customer
Grupo Especializado en Obras Marinas (GEOMSA) is a major developer of pipe-soil systems in the Gulf of Mexico. With over 18 years of experience in marine platform and submarine platform engineering projects, GEOMSA assesses the strength of subsea pipeline systems by determining the effect that expansion and lateral wear have on its life expectancy. The organization specializes in terrestrial pipe and industrial installation projects for hydrocarbon collection and processing. GEOMSA's mission is to reliably meet its clients' requirements.
The Challenge
Grupo Especializado en Obras Marinas (GEOMSA), a major developer of pipe-soil systems in the Gulf of Mexico, was tasked with assessing pipeline integrity under various conditions in the clay soil trenches of an underwater pipeline system. The project's objective was to increase domestic oil production in the surrounding region. The team needed to determine how the new pipeline system would react to expansion and lateral deformation considering the route's horizontal curves, the varying widths of the trench, the number of ocean floor levels above the pipeline, and how the pipeline would interact with the clay soil environment in which it was being placed. They also had to determine a logical and reliable behavior of the pipeline by simulating it inside the trench considering variables such as temperature, lateral deformations, and system stress.
The Solution
To address these challenges, GEOMSA deployed Bentley's AutoPIPE to perform the structural analysis and accurately model the geometry of the pipeline and the characteristics of the soil. The project occurred in two phases. In the first phase, the engineering team used AutoPIPE to develop a 3D model using the project's informational database that describes the types of materials needed for the pipes, connections, and valves. In the second phase, the design team input codes and regulations, design factors, design pressure and temperature, and bend radius elbows. These factors were then used to calculate how the system would interact with the soil. The engineers manipulated the parameters of the soil-pipe interaction in the model to simulate the variations in the width of the trench. They also performed several flexibility analyses so that the team could obtain stress results and deformations in the clay soil.
Operational Impact
Quantitative Benefit
Case Study missing?
Start adding your own!
Register with your work email and create a new case study profile for your business.
Related Case Studies.
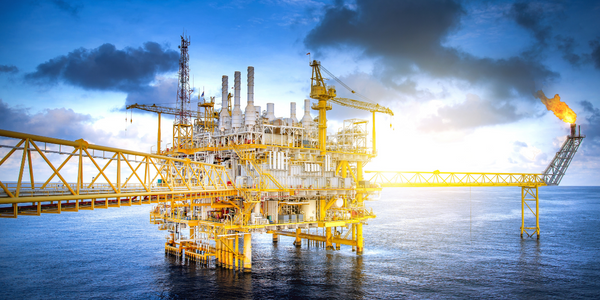
Case Study
Taking Oil and Gas Exploration to the Next Level
DownUnder GeoSolutions (DUG) wanted to increase computing performance by 5 to 10 times to improve seismic processing. The solution must build on current architecture software investments without sacrificing existing software and scale computing without scaling IT infrastructure costs.
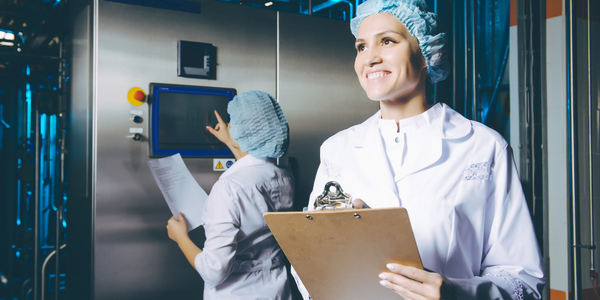
Case Study
Remote Wellhead Monitoring
Each wellhead was equipped with various sensors and meters that needed to be monitored and controlled from a central HMI, often miles away from the assets in the field. Redundant solar and wind generators were installed at each wellhead to support the electrical needs of the pumpstations, temperature meters, cameras, and cellular modules. In addition to asset management and remote control capabilities, data logging for remote surveillance and alarm notifications was a key demand from the customer. Terra Ferma’s solution needed to be power efficient, reliable, and capable of supporting high-bandwidth data-feeds. They needed a multi-link cellular connection to a central server that sustained reliable and redundant monitoring and control of flow meters, temperature sensors, power supply, and event-logging; including video and image files. This open-standard network needed to interface with the existing SCADA and proprietary network management software.
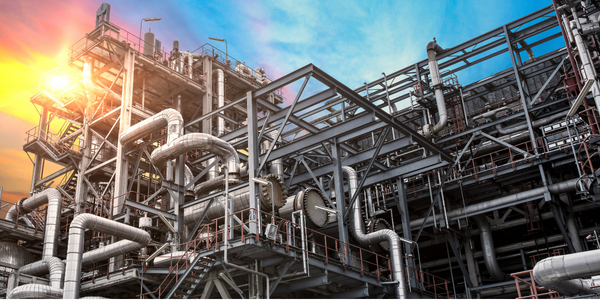
Case Study
Refinery Saves Over $700,000 with Smart Wireless
One of the largest petroleum refineries in the world is equipped to refine various types of crude oil and manufacture various grades of fuel from motor gasoline to Aviation Turbine Fuel. Due to wear and tear, eight hydrogen valves in each refinery were leaking, and each cost $1800 per ton of hydrogen vented. The plant also had leakage on nearly 30 flare control hydrocarbon valves. The refinery wanted a continuous, online monitoring system that could catch leaks early, minimize hydrogen and hydrocarbon production losses, and improve safety for maintenance.
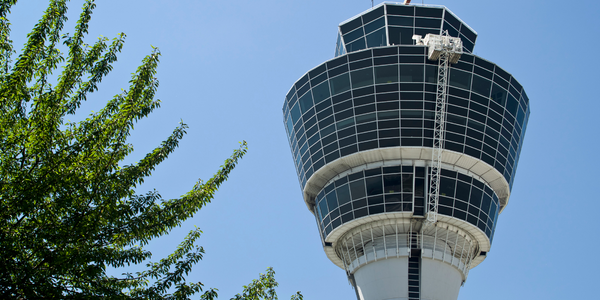
Case Study
Airport SCADA Systems Improve Service Levels
Modern airports are one of the busiest environments on Earth and rely on process automation equipment to ensure service operators achieve their KPIs. Increasingly airport SCADA systems are being used to control all aspects of the operation and associated facilities. This is because unplanned system downtime can cost dearly, both in terms of reduced revenues and the associated loss of customer satisfaction due to inevitable travel inconvenience and disruption.
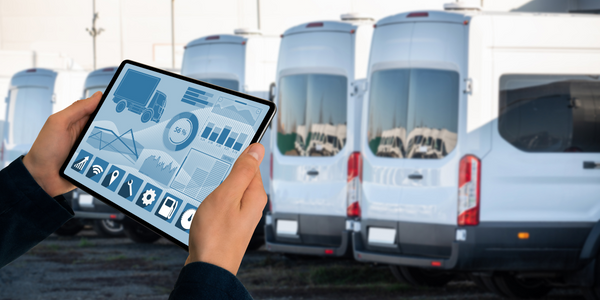
Case Study
IoT-based Fleet Intelligence Innovation
Speed to market is precious for DRVR, a rapidly growing start-up company. With a business model dependent on reliable mobile data, managers were spending their lives trying to negotiate data roaming deals with mobile network operators in different countries. And, even then, service quality was a constant concern.