Technology Category
- Functional Applications - Computerized Maintenance Management Systems (CMMS)
- Functional Applications - Inventory Management Systems
Applicable Industries
- Aerospace
- Automotive
Applicable Functions
- Maintenance
- Warehouse & Inventory Management
Use Cases
- Inventory Management
- Predictive Maintenance
Services
- System Integration
About The Customer
HEXPOL Compounding Americas (HCA) is a custom rubber manufacturer headquartered in Malmö, Sweden, with 16 locations throughout the U.S. and Mexico. HCA manufactures rubber compounds used for parts in the automotive industry, including seals, tires, and hoses, along with a wide range of other industries and applications from aerospace to consumer items. The company uses various methods and materials to customize compounds durable enough to withstand the harshest of conditions. HCA has over 50 manufacturing lines throughout its entire North America portfolio. The company caters to both large bulk orders and small orders, depending on the customer’s needs.
The Challenge
HEXPOL Compounding Americas (HCA), a custom rubber manufacturer with 16 locations throughout the U.S. and Mexico, faced a significant challenge in standardizing their maintenance and operations across all sites. The company's rapid growth, partly through acquisitions, made standardization a top priority. The sites, while decentralized, needed to coordinate among themselves. The company sought a solution that would allow them to implement preventive and predictive maintenance standards to meet the exact requirements of the automotive industry. They also needed a system that could help them standardize their maintenance operations, send weekly and monthly reports to the Managing Director of each site, and implement audits to ensure each site is following best practices.
The Solution
HCA implemented eMaint, a Computerized Maintenance Management System (CMMS), to standardize their maintenance and operations across all sites. The CMMS allowed HCA to roll out standards and make changes quickly across their 16 sites. The reports feature in eMaint was used to automatically send weekly and monthly reports to the Managing Director of each site. Audits were implemented to ensure each site was following best practices for using eMaint. The implementation of eMaint involved a considerable amount of planning and preparation, which ultimately helped HCA gain more visibility and clarity across the organization. The CMMS also helped measure the KPIs that would add the most value and identify processes that could be improved. The parent-child asset hierarchy within eMaint allowed HCA to pinpoint the assets causing the root problem and build additional preventive actions around those assets.
Operational Impact
Case Study missing?
Start adding your own!
Register with your work email and create a new case study profile for your business.
Related Case Studies.
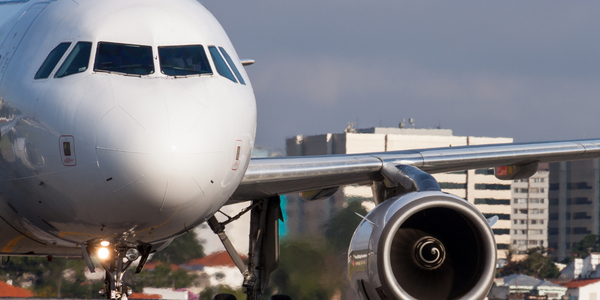
Case Study
Airbus Soars with Wearable Technology
Building an Airbus aircraft involves complex manufacturing processes consisting of thousands of moving parts. Speed and accuracy are critical to business and competitive advantage. Improvements in both would have high impact on Airbus’ bottom line. Airbus wanted to help operators reduce the complexity of assembling cabin seats and decrease the time required to complete this task.
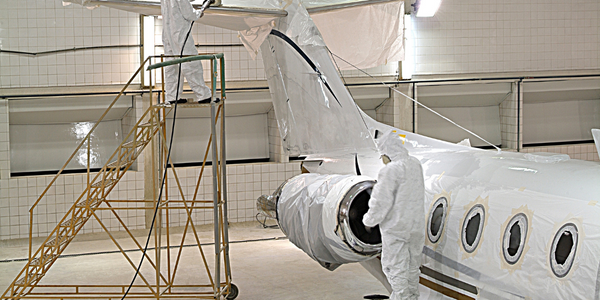
Case Study
Aircraft Predictive Maintenance and Workflow Optimization
First, aircraft manufacturer have trouble monitoring the health of aircraft systems with health prognostics and deliver predictive maintenance insights. Second, aircraft manufacturer wants a solution that can provide an in-context advisory and align job assignments to match technician experience and expertise.
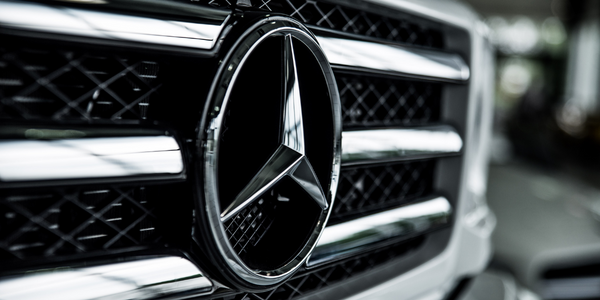
Case Study
Integral Plant Maintenance
Mercedes-Benz and his partner GAZ chose Siemens to be its maintenance partner at a new engine plant in Yaroslavl, Russia. The new plant offers a capacity to manufacture diesel engines for the Russian market, for locally produced Sprinter Classic. In addition to engines for the local market, the Yaroslavl plant will also produce spare parts. Mercedes-Benz Russia and his partner needed a service partner in order to ensure the operation of these lines in a maintenance partnership arrangement. The challenges included coordinating the entire maintenance management operation, in particular inspections, corrective and predictive maintenance activities, and the optimizing spare parts management. Siemens developed a customized maintenance solution that includes all electronic and mechanical maintenance activities (Integral Plant Maintenance).
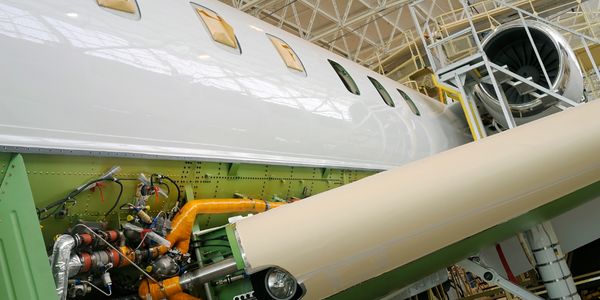
Case Study
Aerospace & Defense Case Study Airbus
For the development of its new wide-body aircraft, Airbus needed to ensure quality and consistency across all internal and external stakeholders. Airbus had many challenges including a very aggressive development schedule and the need to ramp up production quickly to satisfy their delivery commitments. The lack of communication extended design time and introduced errors that drove up costs.