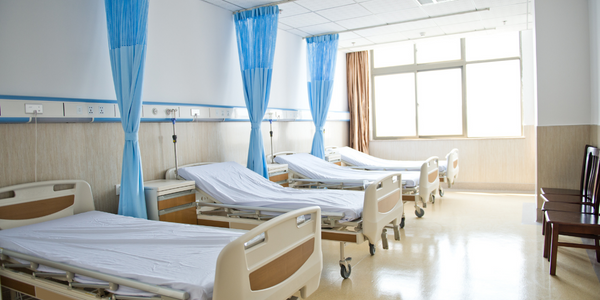
- Functional Applications - Inventory Management Systems
- Networks & Connectivity - RFID
- Sensors - RFID Readers
- Healthcare & Hospitals
- Logistics & Transportation
- Inventory Management
The hospital supply chain team is responsible for ensuring that the right medical supplies are readily available to clinicians when and where needed, and to do so in the most efficient manner possible. However, many of the systems and processes in use at the cancer center for supply chain management were not best suited to support these goals. Barcoding technology, a commonly used method for inventory management of medical supplies, is labor intensive, time consuming, does not provide real-time visibility into inventory levels and can be prone to error. Consequently, the lack of accurate and real-time visibility into inventory levels across multiple supply rooms in multiple hospital facilities creates additional inefficiency in the system causing over-ordering, hoarding, and wasted supplies. Other sources of waste and cost were also identified as candidates for improvement. Existing systems and processes did not provide adequate security for high-cost inventory within the hospital, which was another driver of cost. A lack of visibility into expiration dates for supplies resulted in supplies being wasted due to past expiry dates. Storage of supplies was also a key consideration given the location of the cancer center’s facilities in a dense urban setting, where space is always at a premium. In order to address the challenges outlined above, the hospital sought a solution that would provide real-time inventory information with high levels of accuracy, reduce the level of manual effort required and enable data driven decision making to ensure that the right supplies were readily available to clinicians in the right location at the right time.
After a careful search, they made a decision to deploy ARC Healthcare Technologies’ (ARCHLT) Helios solution to replace their existing inventory management system. Helios integrates with RAIN RFID technology from Impinj to provide a comprehensive set of capabilities used to optimize their inventory management processes across multiple hospital locations. As part of the system deployment, existing supply rooms and storage infrastructure such as cabinets, carts and shelves were retrofitted with Impinj RAIN RFID readers and antennas, creating 500 read points spread throughout the hospital’s storage areas. Fixed reader points were also installed in supply room transition points such as doorways. Workstations outfitted with RAIN RFID label printers were setup in receiving areas to enable hospital staff to print and encode RAIN RFID tags and attach them to supplies when they first entered the hospital. The low cost and small form factor of RAIN RFID meant they could tag a wide range of inventory items at the individual item level including implants, medications, catheters and so on. Once inventory is individually tagged, the supplies are tracked in the Helios system throughout their lifecycle, including location and expiration dates, length of time in inventory, movement of inventory from one supply location to another, and so on. Furthermore, items going into an operating or procedure room are also tracked and monitored through this system. Helios inputs the information on consumed medical supplies, via a hand-held RFID scanner, or a mobile, self-contained scanning workstation, into the EMR system containing the patient’s medical record and also sends this information to the hospital’s billing system. With this level of visibility into hospital inventories, the supply chain team can now continuously monitor inventory levels throughout the hospital in real time, and when appropriate automatically generate requisitions and purchase orders to reorder products such as implants, medications, catheters thereby ensuring that optimal inventory levels are maintained at all times.
Case Study missing?
Start adding your own!
Register with your work email and create a new case study profile for your business.
Related Case Studies.
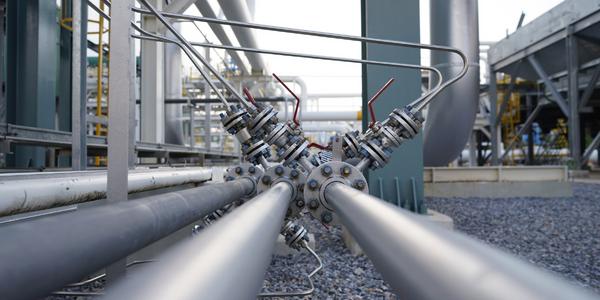
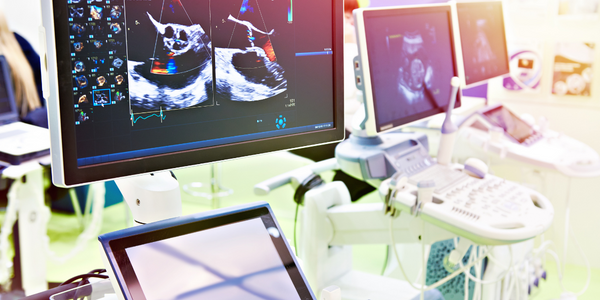
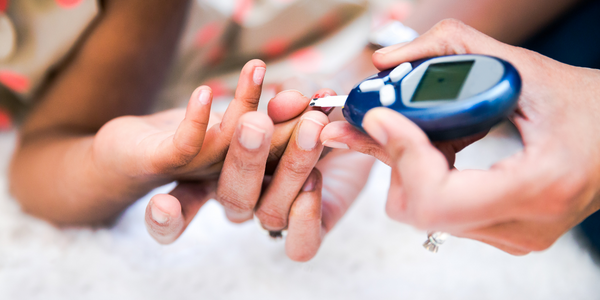
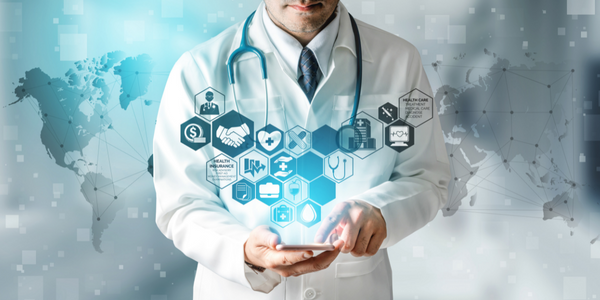
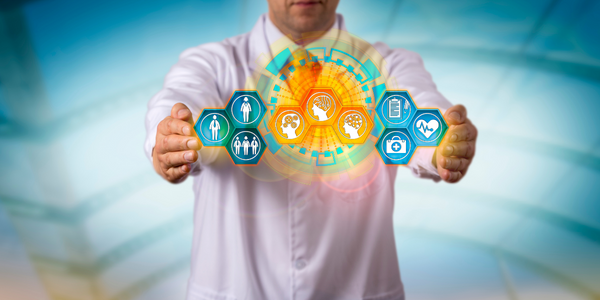