Customer Company Size
Large Corporate
Region
- Africa
- America
Country
- Canada
- South Africa
Product
- IsoMetrix EHS Solution
Implementation Scale
- Enterprise-wide Deployment
Impact Metrics
- Environmental Impact Reduction
- Brand Awareness
- Customer Satisfaction
Technology Category
- Functional Applications - Remote Monitoring & Control Systems
Applicable Industries
- Mining
Applicable Functions
- Discrete Manufacturing
- Quality Assurance
Use Cases
- Predictive Maintenance
- Remote Asset Management
Services
- Software Design & Engineering Services
- System Integration
About The Customer
De Beers Group is a global diamond mining company that has been in operation since 1888. The company has operations in Canada, South Africa, Botswana, and Namibia. De Beers Group is committed to a sustainable legacy built on safety, thriving communities, and protected environments. This commitment is encapsulated in their 'Building Forever' strategy, which is built on four pillars: protecting the natural world, partnering for thriving communities, standing with women and girls, and leading ethical practices across the industry. In 2019, the company reported an annual revenue of USD 4.6 billion and has over 30,000 employees.
The Challenge
De Beers Group, a global diamond mining company, recognized the need for a software solution to support their 'Building Forever' strategy, which is built on protecting the natural world, partnering for thriving communities, standing with women and girls, and leading ethical practices across the industry. The company had been using IsoMetrix since the late 1990s, but in 2016, they initiated a global strategy to drive sustainability and shared value. They chose IsoMetrix as a software vendor to develop and implement a standardized system for managing Environmental, Health and Safety (EHS) incidents, risk management, and actions across all their business units. This complex project, named 'Project Unity', aimed to standardize reporting requirements across eight individual business units to allow for group reporting. The business units where IsoMetrix has been implemented are in Botswana, Canada, and South Africa.
The Solution
De Beers Group chose IsoMetrix based on the software provider’s global footprint, and the product’s user-friendly interfaces and superior dashboarding and reporting capabilities. In addition, the two companies’ 20-year partnership was a key factor, with the product’s evolution having been spurred to a large extent by forward-thinking customers such as De Beers Group. The solution allows for individual customization at site level to match existing processes, ease change management, and create global reporting. The key success factors in the project were achieving functionality, flexibility, and simplicity of design. Building on the IsoMetrix systems that De Beers Group was already using made it easier for employees to adopt the changes because they were already familiar with the systems. The IsoMetrix team was cognizant of the operational requirements of each business unit, and the software itself had sufficient flexibility to accommodate each business unit’s requirements while still maintaining a global group reporting standard.
Operational Impact
Case Study missing?
Start adding your own!
Register with your work email and create a new case study profile for your business.
Related Case Studies.
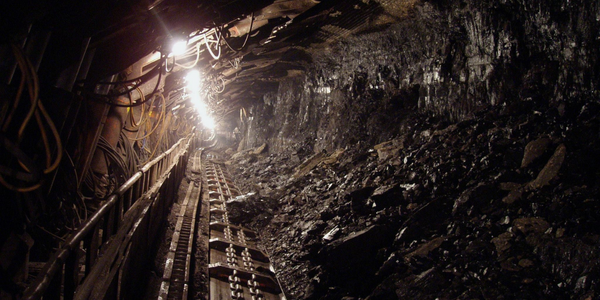
Case Study
Underground Mining Safety
The goal was to produce a safety system to monitor and support underground mining operations; existing systems were either too simple (i.e. phone line) or overly complex and expensive, inhibiting deployment, and providing little-to-no support in event of an accident. Given the dangerous nature of the mining work environment and the strict regulations placed on the industry, the solution would have to comply with Mine Safety and Health Administration (MSHA) regulations. Yet the product needed to allow for simple deployment to truly be a groundbreaking solution - increasing miner safety and changing daily operations for the better.
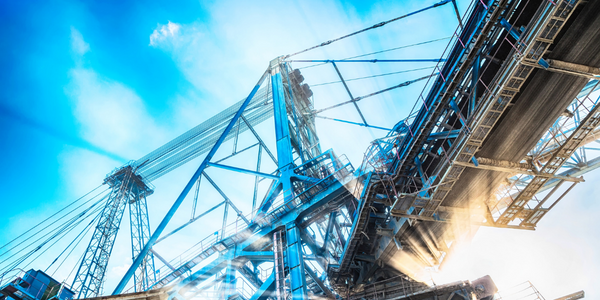
Case Study
Mining Firm Quadruples Production, with Internet of Everything
Dundee Precious Metal’s flagship mine, in Chelopech, Bulgaria, produces a gold, copper, and silver concentrate set a goal to increase production by 30%. Dundee wanted to increase production quality and output without increasing headcount and resources, improve miner safety, and minimize cost.
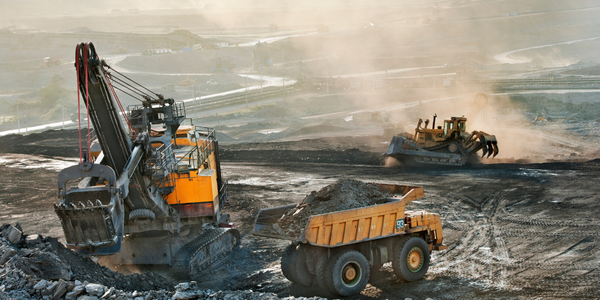
Case Study
Fastenal Builds the Future of Manufacturing with MachineMetrics
Fastenal's objective was to better understand their machine downtime, utilization, quality issues, and to embrace cutting-edge manufacturing technology/process improvement capabilities to bring their team to the next level. However, there was a lack of real-time data, visualization, and actionable insights made this transition impossible.
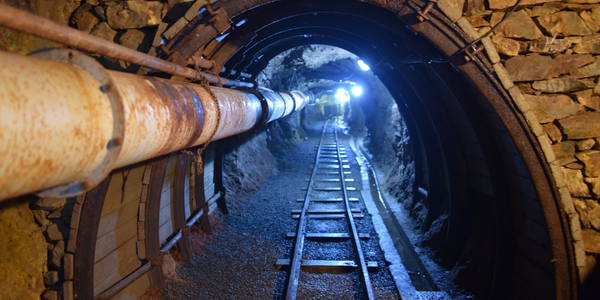
Case Study
Joy Mining Systems
Joy equipment faces many challenges. The first is machine integration and control. The business end of the machine has a rapidly-spinning cylinder with 6-inch diamond-studded cutting teeth. It chews through rock at rates measured in tens of tons per minute. The system grinds through the rock in front, creating a rectangular mine tunnel. Hydraulic lifters support the ceiling as the machine moves forward. Automated drills and screws drive 3-ft long screws into the ceiling to stabilize it. The rock and coal fall into a set of gathering "fingers" below the cutting cylinder. These fingers scoop up the rock and coal and deposit it onto a conveyor belt. The conveyor passes under the machine and out the back. A train of conveyor belt cars, up to a mile long, follows the cutter into the mine. The rock shoots along this train at over 400 feet per minute until it empties into rail cars at the end. Current systems place an operator cage next to the cutter. Choking dust (potentially explosive), the risk of collapse and the proximity of metal and rock mayhem make the operator cage a hazardous location.
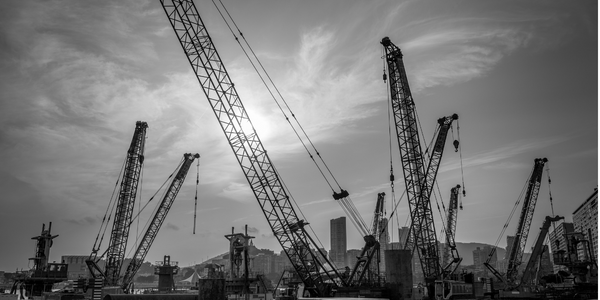
Case Study
Improved Monitoring in Industrial Manufacturing Facility
When your crane is moving tons of magma-hot iron, you can’t afford an unexpected failure. McWane Ductile knew monitoring the crane motor metrics within their facility could help prevent a mechanical failure that would strand an enormous bucket of molten metal overhead. Unfortunately, their legacy wired monitoring system couldn’t work with moving objects in this extreme environment. If they could integrate wireless capabilities into their existing equipment they could extend their monitoring capabilities without starting over from scratch.