Customer Company Size
Large Corporate
Region
- America
Country
- United States
Product
- Infor's enterprise software
- LogicMonitor
- Amazon Web Services (AWS)
Tech Stack
- AWS EC2
- AWS ECS
- AWS ELB
- AWS EBS
- AWS RDS
Implementation Scale
- Enterprise-wide Deployment
Impact Metrics
- Productivity Improvements
- Digital Expertise
Technology Category
- Infrastructure as a Service (IaaS) - Cloud Computing
- Infrastructure as a Service (IaaS) - Cloud Storage Services
- Infrastructure as a Service (IaaS) - Public Cloud
Applicable Industries
- Aerospace
- Automotive
- Finance & Insurance
Applicable Functions
- Discrete Manufacturing
- Product Research & Development
Use Cases
- Predictive Maintenance
- Manufacturing System Automation
Services
- Cloud Planning, Design & Implementation Services
- Data Science Services
About The Customer
Infor is a global enterprise software provider headquartered in New York City. The company is a strategic partner to more than 90,000 customers spread across 170 countries worldwide. They produce industry-specific software solutions for some of the most well-known companies in the world, including 18 of the top 20 aerospace firms, 20 of the top 20 automotive suppliers, and 21 of the top 30 global banks. In order to support their purpose-built applications, ranging from process-oriented solutions for Ferrari’s engineers to data science analytics for the Brooklyn Nets, Infor leverages a substantial and extremely sophisticated deployment in Amazon Web Services (AWS).
The Challenge
Infor, a global enterprise software provider, has a massive deployment in Amazon Web Services (AWS) to support their purpose-built applications. They leverage a wide range of AWS services, including more than 14,000 EC2 instances, ECS, ELB, EBS, RDS, Elasticsearch, Auto Scaling, Lambda, ElastiCache, and more. However, maintaining visibility into the more than 50,000 AWS resources supporting their application solutions is a significant challenge. Before LogicMonitor, Infor relied on several monitoring tools, but primarily used an agent-based system that required a significant amount of ongoing maintenance and configuration. With more than 14,000 EC2 instances, upgrading and configuring agents required substantial staffing investments. The frequent need to upgrade agents only during appropriate maintenance windows for such a huge fleet was a constant challenge. On top of that, updating an existing agent or adding a new agent to a host carried the risk of affecting other production processes and services on that host.
The Solution
Infor chose LogicMonitor to streamline their monitoring processes and improve mean-time-to-resolution. LogicMonitor’s built-in automation, actionable alerting, and depth of coverage for AWS resources allowed Infor to reassign staff to more strategic activities than configuring and upgrading agents. LogicMonitor also provided Infor with access to critical metrics more efficiently. It automatically collects AWS performance data using three main methods to provide a complete picture: the CloudWatch API, the AWS SDK, and via the LogicMonitor Collector installed in an AWS environment. This multi-pronged monitoring strategy provides a deeper and more robust picture of resource performance. Data from all of these collection methods can be alerted on, displayed on rich, customizable dashboards, and disseminated through detailed reports, all from within LogicMonitor.
Operational Impact
Quantitative Benefit
Case Study missing?
Start adding your own!
Register with your work email and create a new case study profile for your business.
Related Case Studies.
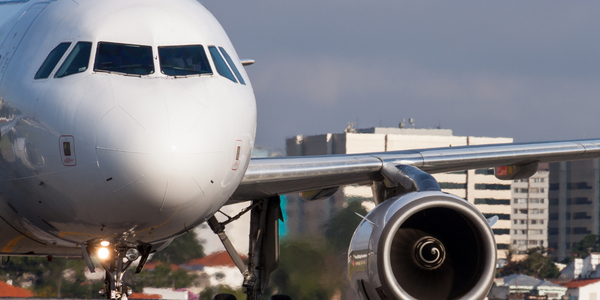
Case Study
Airbus Soars with Wearable Technology
Building an Airbus aircraft involves complex manufacturing processes consisting of thousands of moving parts. Speed and accuracy are critical to business and competitive advantage. Improvements in both would have high impact on Airbus’ bottom line. Airbus wanted to help operators reduce the complexity of assembling cabin seats and decrease the time required to complete this task.
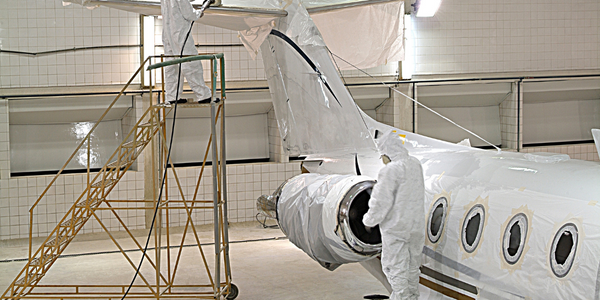
Case Study
Aircraft Predictive Maintenance and Workflow Optimization
First, aircraft manufacturer have trouble monitoring the health of aircraft systems with health prognostics and deliver predictive maintenance insights. Second, aircraft manufacturer wants a solution that can provide an in-context advisory and align job assignments to match technician experience and expertise.
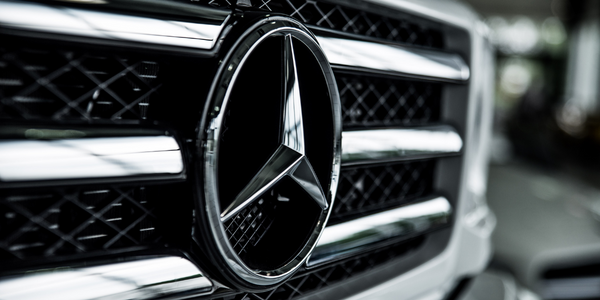
Case Study
Integral Plant Maintenance
Mercedes-Benz and his partner GAZ chose Siemens to be its maintenance partner at a new engine plant in Yaroslavl, Russia. The new plant offers a capacity to manufacture diesel engines for the Russian market, for locally produced Sprinter Classic. In addition to engines for the local market, the Yaroslavl plant will also produce spare parts. Mercedes-Benz Russia and his partner needed a service partner in order to ensure the operation of these lines in a maintenance partnership arrangement. The challenges included coordinating the entire maintenance management operation, in particular inspections, corrective and predictive maintenance activities, and the optimizing spare parts management. Siemens developed a customized maintenance solution that includes all electronic and mechanical maintenance activities (Integral Plant Maintenance).
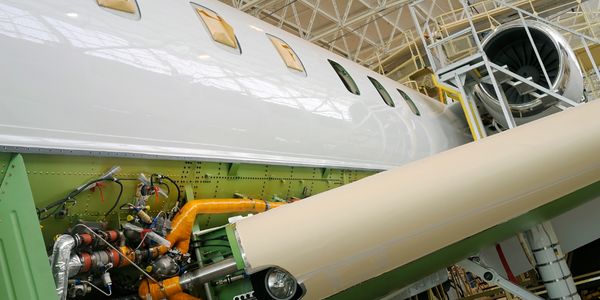
Case Study
Aerospace & Defense Case Study Airbus
For the development of its new wide-body aircraft, Airbus needed to ensure quality and consistency across all internal and external stakeholders. Airbus had many challenges including a very aggressive development schedule and the need to ramp up production quickly to satisfy their delivery commitments. The lack of communication extended design time and introduced errors that drove up costs.