Applicable Industries
- Mining
- Retail
Applicable Functions
- Logistics & Transportation
Use Cases
- In-process Traceability
- Supply Chain Visibility
About The Customer
The customer in this case is the ITSCI Programme, an initiative that aims to promote responsible mineral trade in conflict-affected and high-risk areas. The programme focuses on the supply chains of tin, tungsten, and tantalum in Burundi, the Democratic Republic of the Congo, Rwanda, and Uganda. The ITSCI Programme uses technology to gain transparency and traceability in the supply chain of these minerals, ensuring that they are mined, processed, traded, and smelted responsibly. The programme uses customized software built on ChainPoint technology to achieve its objectives.
The Challenge
In conflict-affected and high-risk areas (CAHRA), the extraction and trade of minerals such as tin, tungsten, tantalum, and gold can contribute to conflicts and human rights abuses. These raw materials are used in a wide range of products, including everyday electronic devices. The challenge lies in promoting responsible mineral trade, which requires transparency and traceability in the supply chain. The lack of a reliable system to track and trace these minerals from their source to their final destination makes it difficult to ensure ethical practices in their extraction and trade. The ITSCI Programme was established to address this issue, focusing on the supply chains in Burundi, the Democratic Republic of the Congo, Rwanda, and Uganda.
The Solution
The ITSCI Programme uses ChainPoint software to track and trace tin, tantalum, and tungsten from mines, processors, and exporters. At mine sites and processing facilities, each bag of minerals is tagged with a unique code. This code is recorded at every stage in the supply chain and linked to a unique shipping number. With this highly detailed logging system, it is possible to determine where each bag of minerals was mined, processed, traded and smelted. The data can be presented in multiple ways, such as maps, charts, and graphs. The software that ITSCI uses on a day-to-day basis is built on ChainPoint technology and is customized to the specific needs of the programme. The solutions used include data collection using a mobile solution, reporting and analytics, traceability from mine to smelter, and multi-language and advanced authorization.
Operational Impact
Case Study missing?
Start adding your own!
Register with your work email and create a new case study profile for your business.
Related Case Studies.
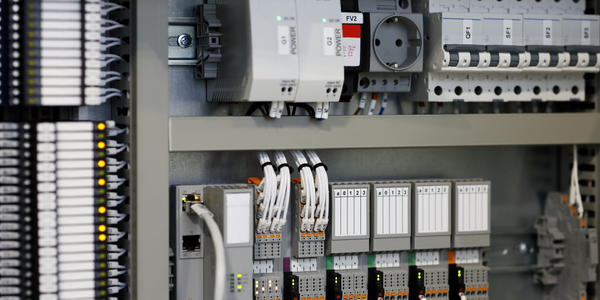
Case Study
Improving Production Line Efficiency with Ethernet Micro RTU Controller
Moxa was asked to provide a connectivity solution for one of the world's leading cosmetics companies. This multinational corporation, with retail presence in 130 countries, 23 global braches, and over 66,000 employees, sought to improve the efficiency of their production process by migrating from manual monitoring to an automatic productivity monitoring system. The production line was being monitored by ABB Real-TPI, a factory information system that offers data collection and analysis to improve plant efficiency. Due to software limitations, the customer needed an OPC server and a corresponding I/O solution to collect data from additional sensor devices for the Real-TPI system. The goal is to enable the factory information system to more thoroughly collect data from every corner of the production line. This will improve its ability to measure Overall Equipment Effectiveness (OEE) and translate into increased production efficiencies. System Requirements • Instant status updates while still consuming minimal bandwidth to relieve strain on limited factory networks • Interoperable with ABB Real-TPI • Small form factor appropriate for deployment where space is scarce • Remote software management and configuration to simplify operations
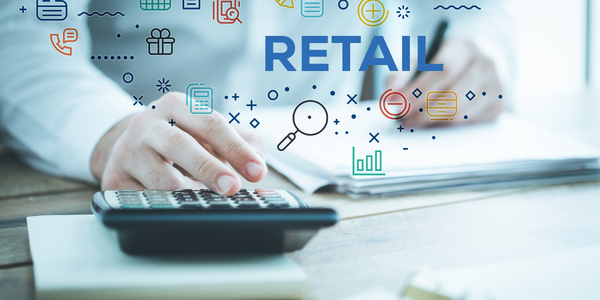
Case Study
Digital Retail Security Solutions
Sennco wanted to help its retail customers increase sales and profits by developing an innovative alarm system as opposed to conventional connected alarms that are permanently tethered to display products. These traditional security systems were cumbersome and intrusive to the customer shopping experience. Additionally, they provided no useful data or analytics.
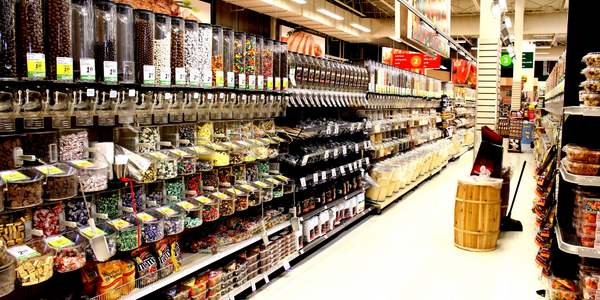
Case Study
How Sirqul’s IoT Platform is Crafting Carrefour’s New In-Store Experiences
Carrefour Taiwan’s goal is to be completely digital by end of 2018. Out-dated manual methods for analysis and assumptions limited Carrefour’s ability to change the customer experience and were void of real-time decision-making capabilities. Rather than relying solely on sales data, assumptions, and disparate systems, Carrefour Taiwan’s CEO led an initiative to find a connected IoT solution that could give the team the ability to make real-time changes and more informed decisions. Prior to implementing, Carrefour struggled to address their conversion rates and did not have the proper insights into the customer decision-making process nor how to make an immediate impact without losing customer confidence.
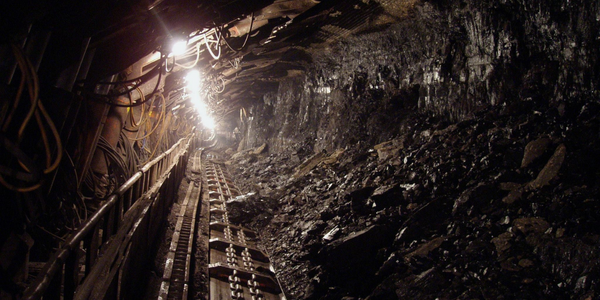
Case Study
Underground Mining Safety
The goal was to produce a safety system to monitor and support underground mining operations; existing systems were either too simple (i.e. phone line) or overly complex and expensive, inhibiting deployment, and providing little-to-no support in event of an accident. Given the dangerous nature of the mining work environment and the strict regulations placed on the industry, the solution would have to comply with Mine Safety and Health Administration (MSHA) regulations. Yet the product needed to allow for simple deployment to truly be a groundbreaking solution - increasing miner safety and changing daily operations for the better.
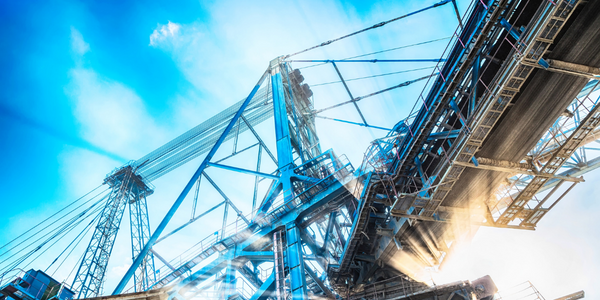
Case Study
Mining Firm Quadruples Production, with Internet of Everything
Dundee Precious Metal’s flagship mine, in Chelopech, Bulgaria, produces a gold, copper, and silver concentrate set a goal to increase production by 30%. Dundee wanted to increase production quality and output without increasing headcount and resources, improve miner safety, and minimize cost.