Technology Category
- Application Infrastructure & Middleware - Middleware, SDKs & Libraries
- Sensors - Acoustic Sensors
Applicable Industries
- Electronics
- Retail
Applicable Functions
- Product Research & Development
Use Cases
- Time Sensitive Networking
- Virtual Prototyping & Product Testing
About The Customer
Bang & Olufsen is a Danish company that was founded in 1925. It has since developed a reputation for its range of unique, high-quality audio, video, and multimedia products. The company is known for its innovative designs and commitment to quality, which is reflected in its products that dictate the new fashion in audio equipment. Bang & Olufsen employs over 2,550 people across its offices and retail stores located in over 100 countries. The company's 'ideas factory', where most of its electronic designs are born, is a testament to its commitment to innovation and creativity.
The Challenge
Bang & Olufsen, a renowned manufacturer of high-quality audio, video, and multimedia products, faced a unique challenge in its 'ideas factory'. The 'ideas factory' is the birthplace of most of the company's electronic designs, where prototypes for the next generation of audio, visual, and mobile communication systems are created. The challenge was dealing with the multitude of options and changes that each prototype presented. Every new prototype was akin to a blank canvas, and the real test was finding the appropriate architecture for the board. Additionally, the company's unique mechanical casings presented a significant challenge for the designers. The process of changing and redesigning components, re-evaluating design media, and making trade-offs was complex and time-consuming.
The Solution
The solution to Bang & Olufsen's challenge came in the form of Altium Designer, a PCB design software that introduced a 3D STEP file import function. This feature allowed the designers to view all the electronics inside its mechanical case in its final form, significantly reducing development time. Altium Designer also enabled the designers to link to external databases and draw their footprints onto the schematic. The software's integrated libraries made it easy to create unique components, which was crucial for Bang & Olufsen, given the uniqueness of their products. The unified design environment of Altium meant that changes made in a single domain would be reflected throughout the entire design, eliminating the usual re-formatting or revision problems that previously impeded development.
Operational Impact
Quantitative Benefit
Case Study missing?
Start adding your own!
Register with your work email and create a new case study profile for your business.
Related Case Studies.
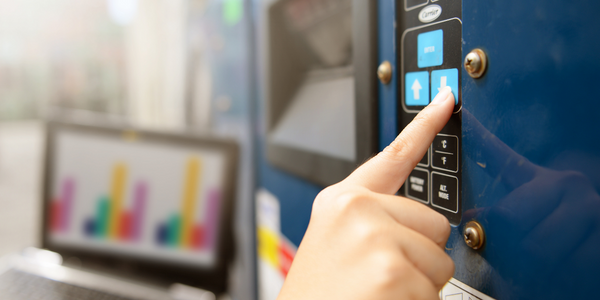
Case Study
Remote Temperature Monitoring of Perishable Goods Saves Money
RMONI was facing temperature monitoring challenges in a cold chain business. A cold chain must be established and maintained to ensure goods have been properly refrigerated during every step of the process, making temperature monitoring a critical business function. Manual registration practice can be very costly, labor intensive and prone to mistakes.
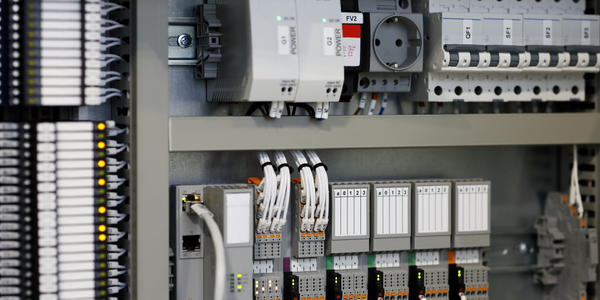
Case Study
Improving Production Line Efficiency with Ethernet Micro RTU Controller
Moxa was asked to provide a connectivity solution for one of the world's leading cosmetics companies. This multinational corporation, with retail presence in 130 countries, 23 global braches, and over 66,000 employees, sought to improve the efficiency of their production process by migrating from manual monitoring to an automatic productivity monitoring system. The production line was being monitored by ABB Real-TPI, a factory information system that offers data collection and analysis to improve plant efficiency. Due to software limitations, the customer needed an OPC server and a corresponding I/O solution to collect data from additional sensor devices for the Real-TPI system. The goal is to enable the factory information system to more thoroughly collect data from every corner of the production line. This will improve its ability to measure Overall Equipment Effectiveness (OEE) and translate into increased production efficiencies. System Requirements • Instant status updates while still consuming minimal bandwidth to relieve strain on limited factory networks • Interoperable with ABB Real-TPI • Small form factor appropriate for deployment where space is scarce • Remote software management and configuration to simplify operations
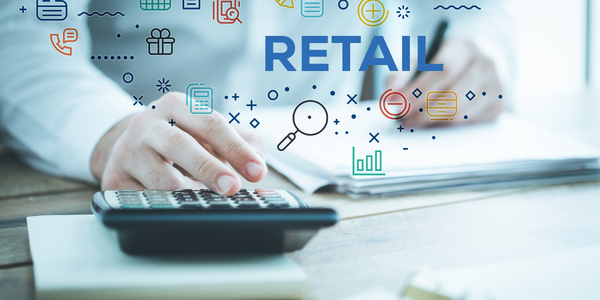
Case Study
Digital Retail Security Solutions
Sennco wanted to help its retail customers increase sales and profits by developing an innovative alarm system as opposed to conventional connected alarms that are permanently tethered to display products. These traditional security systems were cumbersome and intrusive to the customer shopping experience. Additionally, they provided no useful data or analytics.
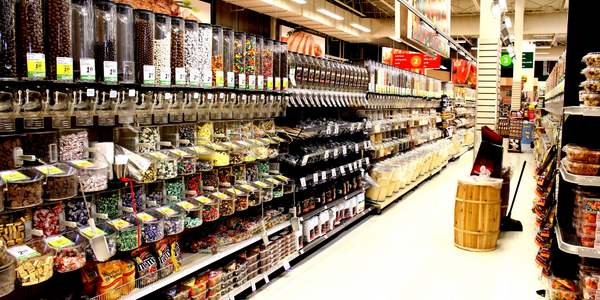
Case Study
How Sirqul’s IoT Platform is Crafting Carrefour’s New In-Store Experiences
Carrefour Taiwan’s goal is to be completely digital by end of 2018. Out-dated manual methods for analysis and assumptions limited Carrefour’s ability to change the customer experience and were void of real-time decision-making capabilities. Rather than relying solely on sales data, assumptions, and disparate systems, Carrefour Taiwan’s CEO led an initiative to find a connected IoT solution that could give the team the ability to make real-time changes and more informed decisions. Prior to implementing, Carrefour struggled to address their conversion rates and did not have the proper insights into the customer decision-making process nor how to make an immediate impact without losing customer confidence.