Technology Category
- Functional Applications - Inventory Management Systems
- Functional Applications - Warehouse Management Systems (WMS)
Applicable Industries
- E-Commerce
- Marine & Shipping
Applicable Functions
- Logistics & Transportation
- Warehouse & Inventory Management
Use Cases
- Inventory Management
- Picking, Sorting & Positioning
About The Customer
Fire Department Coffee is a veteran-owned business certified by the National Veteran-Owned Business Association (NaVOBA). The company is run by active and retired firefighters and operates as an e-commerce coffee company, shipping coffee globally. As the business expanded, they faced challenges in managing their inventory and needed a system that could handle their growing and evolving operations. They sought a solution that could integrate with their existing platforms and assist with their daily warehouse tasks, ensuring accurate inventory tracking and efficient order fulfillment.
The Challenge
Fire Department Coffee (FDC), a veteran-owned e-commerce coffee company, was facing challenges in managing its inventory as the business grew. The company, run by active and retired firefighters, ships coffee globally, necessitating a robust and efficient inventory system. The existing system was not equipped to handle the increasing complexity and scale of operations, leading to inefficiencies and potential errors in order fulfillment. The company needed a solution that could seamlessly integrate with their existing platforms like Shipstation, Shopify, and Faire, and help them manage their day-to-day warehouse tasks effectively.
The Solution
FDC adopted Finale Inventory, a comprehensive inventory management software, to address their growing needs. The software's Barcode Scanner App was particularly useful in assisting with daily warehouse tasks, ensuring accurate tracking of inventory and efficient order fulfillment. The integration of Finale with Shipstation, Shopify, and Faire streamlined FDC's operations, enabling them to pull in all their sales orders from Shipstation and accurately pack and pull orders using the Barcode Scanner. This significantly reduced shipping errors in their warehouse. Additionally, Finale's customer service was a key factor in their decision, with the assurance of prompt assistance whenever needed.
Operational Impact
Quantitative Benefit
Case Study missing?
Start adding your own!
Register with your work email and create a new case study profile for your business.
Related Case Studies.
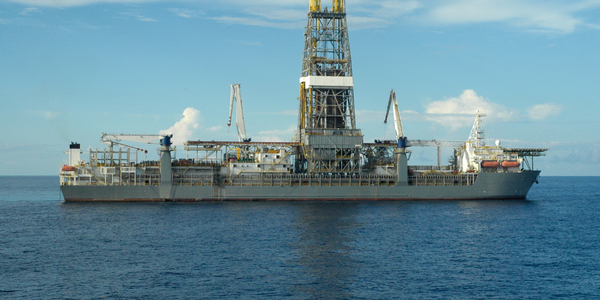
Case Study
Drill ship power challenge: hybrid solution solves distribution issues
Aspin Kemp & Associates (AKA), a manufacturer of electrical power and control systems headquartered in Montague, PEI, encountered one with its hybrid power initiative, the first hybrid drill floor destined for installation on ultra-deepwater drill ships operated by Transocean, Swiss offshore drilling contractors. Since on-site modification was impossible and scrap recycling of any modifications was unacceptable, the enclosures had to arrive ready-to-install.
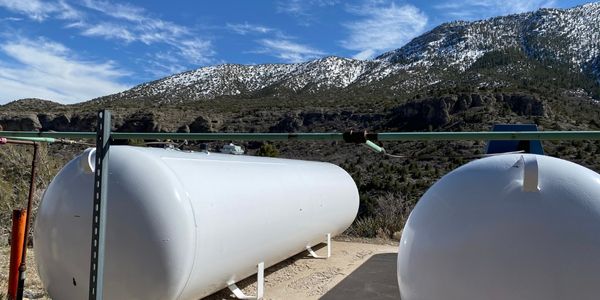
Case Study
Ensures Tanker Safety and Emissions Compliance
Storage tanks are irregular in shape and a certain amount of mathematical modelling is required to get an accurate representation of volume and, more importantly, the weight of material in each tank. In addition, countries have different emission regulations, so the ships position needed to be accurately known in order to geotag emission data.
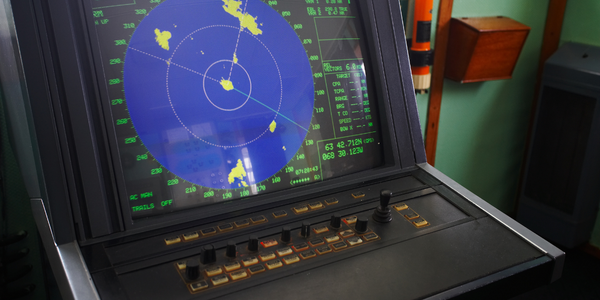
Case Study
Real-time Networked Sonar System for Ships
A multinational, knowledge-based corporation that delivers marine electronics solutions is utilizing industrial Ethernet technology to help ensure that operations at sea are dependable and optimal. Based in Europe, the company has nearly 4000 employees working in 20 countries around the world, and produces high-tech systems for offshore oil and gas operations, merchant marine systems, and various applications for the defense and aerospace industries. The company produces products and systems used by merchant vessels and offshore installations for positioning, navigation, automation, as well as for surveying and monitoring the seabed, and for fishing vessels and fi sheries research. As one of the major suppliers of high quality marine electronics in the world, their products include chart plotters for yachts, triple redundant dynamic positioning systems for oil drilling rigs, and sonar and instrument systems for scientifi c research vessels. Products used for marine applications must be rugged enough to endure the corrosive effects of salt water, and be able to withstand excessive amounts of vibration and shock. For this reason, the company only uses DNV and GL certified products and components to ensure that their systems can meet the high standards required by the maritime industry.
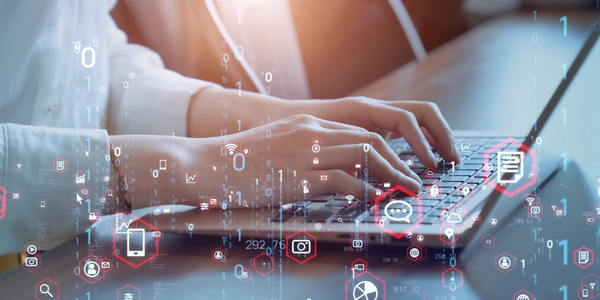
Case Study
Digital Transformation of Atlanta Grout & Tile: An IoT Case Study
Atlanta Grout & Tile, a Tile, Stone & Grout restoration company based in Woodstock, Georgia, was facing challenges with its traditional business model. Despite steady growth over the years, the company was falling behind the web revolution and missing out on the opportunity to tap into a new consumer base. They were using independent software from different vendors for each of their department information and workforce management. This resulted in a lot of manual work on excel and the need to export/import data between different systems. This not only increased overhead costs but also slowed down their response to clients. The company also had to prepare numerous reports manually and lacked access to customer trends for effective business decision-making.
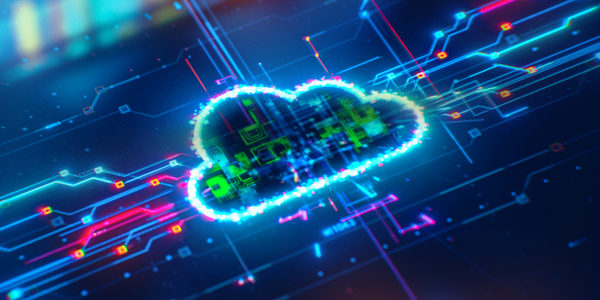
Case Study
Fleet Management Connectivity Solution for Marzam
Marzam, in order to ensure the best service, invested 3 million dollars in the construction of 2 fuel oil tanks with 40k gallons and 10k gallons capacity each, located in Manta, Ecuador. The customer needs to keep fleet operations going with fuel available at all times in order to guarantee quality of service. KEY ELEMENTS FOR THE CUSTOMER: Real-time level monitoring: Tank infrastructure remote level monitoring. Configure alerts and notifications when reaching critical values to avoid the need for emergency refills and optimize supply schedules. Real-time consumption monitoring: The customer needed an easy way to monitor in real-time accurate values of consumption.
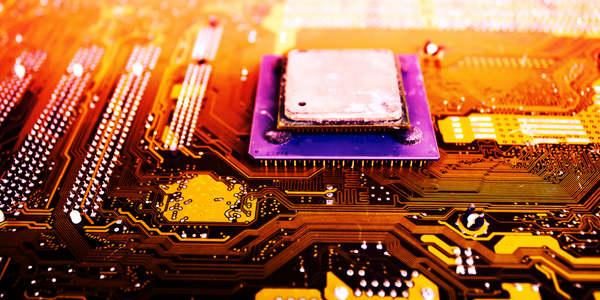
Case Study
Mitsubishi Electric's Edge Computing Solution Powered by Wind River VxWorks
Mitsubishi Electric Corporation, a global leader in factory automation (FA) applications, identified edge computing as a critical component of the Industrial Internet of Things (IIoT). The company aimed to enhance device and data security, reduce data traffic to the cloud, and enable faster response to network or device issues. In 2018, Mitsubishi Electric launched its first line of industrial hardware products designed for edge computing, the MELIPC Series. The primary development goals for MELIPC were to support the type of edge computing promoted by Mitsubishi Electric and to introduce advanced vision technology for device control. The flagship computer of the MELIPC line, the MI5000, was designed to combine real-time equipment control with high-speed data collection, processing, diagnosis, and feedback in a single machine. However, the development team needed a real-time control platform that could seamlessly integrate real-time control with proven analytic and diagnostic applications.