Customer Company Size
Mid-size Company
Region
- America
- Asia
Country
- United States
- China
Product
- Intellect QMS
Tech Stack
- Cloud-based software
- No-code capabilities
- Mobile app
Implementation Scale
- Enterprise-wide Deployment
Impact Metrics
- Productivity Improvements
- Waste Reduction
Technology Category
- Platform as a Service (PaaS) - Data Management Platforms
Applicable Industries
- Consumer Goods
Applicable Functions
- Quality Assurance
Use Cases
- Inventory Management
Services
- Cloud Planning, Design & Implementation Services
- Software Design & Engineering Services
About The Customer
Klean Kanteen is a family- and employee-owned manufacturer of stainless steel bottles, food solutions, accessories, and sustainable lifestyle products. The company was founded in northern California in the early 2000s and is built on a love of adventure, a love of conserving wild places, and a mission to replace single-use plastic with healthful, BPA-free drinkware and food solutions. Klean Kanteen introduced the first reusable stainless steel drinking bottles nearly two decades ago, at a time when no other company was producing them. This marked the beginning of the company’s powerful mission-driven journey to transform an entire industry and save the planet. Being a family- and employee-owned company affords Klean Kanteen the flexibility to remain nimble and responsive while pursuing their mission, empowering their employees, and helping organizations that are working to make the world a better place.
The Challenge
Klean Kanteen, a manufacturer of stainless steel bottles and sustainable lifestyle products, was facing challenges with its business processes. The company's employees were spending days each month collecting and organizing quality data manually. The company also worked with contract manufacturers overseas, employing local workers to inspect finished goods prior to shipment. The company needed a Quality Management System (QMS) solution that could automate these processes and be accessed by any employee, from virtually anywhere. The solution also needed to be localizable to meet the needs of overseas employees.
The Solution
Klean Kanteen decided on the Intellect QMS platform after a thorough vetting process. They were impressed with its no-code capabilities, extreme configurability, and its proven record with both custom and out-of-the-box mobile apps. Intellect’s cloud-based software met all of the company’s requirements for anytime/anywhere access, and it was localizable for China, or for any other overseas location. The team at Klean Kanteen implemented a finished goods inspection app, and also realized that document control was an even higher priority. They moved to cloud-based software for document control, making it easier for their global workforce to access any quality management document, at any time. With Intellect's no-code capabilities, the team at Klean Kanteen has successfully built a sophisticated mobile app for inspection.
Operational Impact
Case Study missing?
Start adding your own!
Register with your work email and create a new case study profile for your business.
Related Case Studies.
.png)
Case Study
Improving Vending Machine Profitability with the Internet of Things (IoT)
The vending industry is undergoing a sea change, taking advantage of new technologies to go beyond just delivering snacks to creating a new retail location. Intelligent vending machines can be found in many public locations as well as company facilities, selling different types of goods and services, including even computer accessories, gold bars, tickets, and office supplies. With increasing sophistication, they may also provide time- and location-based data pertaining to sales, inventory, and customer preferences. But at the end of the day, vending machine operators know greater profitability is driven by higher sales and lower operating costs.
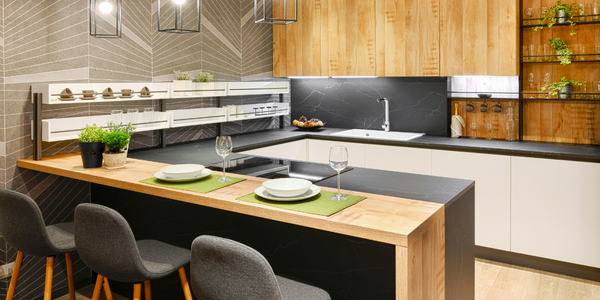
Case Study
Series Production with Lot-size-1 Flexibility
Nobilia manufactures customized fitted kitchens with a lot size of 1. They require maximum transparency of tracking design data and individual processing steps so that they can locate a particular piece of kitchen furniture in the sequence of processes.
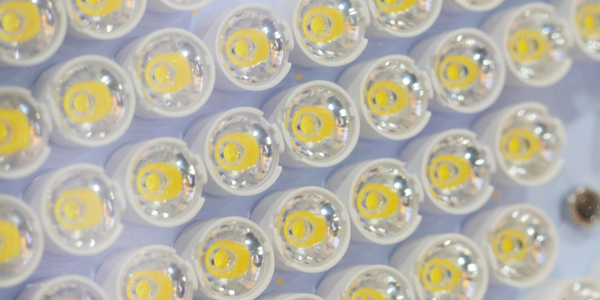
Case Study
American Eagle Achieves LEED with GE LED Lighting Fixtures
American Eagle Outfitters (AEO) was in the process of building a new distribution center. The AEO facility management team decided to look at alternate options for lighting layout that could provide energy and maintenance savings. AEO would need a full-time maintenance employee just to replace burned-out fluorescent tubes.
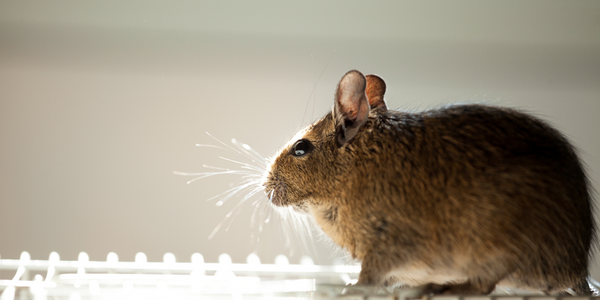
Case Study
Revolutionizing Rodent Control
From pet- and child-safe traps, to touch-free and live-catch rodent control solutions, Victor continues to stay committed to producing superior products that meet the varying needs of today’s pest control professionals. And, with a long standing history supporting customers in the food processing, service, and retail settings, Victor knew that strict regulations were costing organizations thousands of dollars in excess overhead trying to manage their rodent-control solutions. Trap inspections in these environments are often difficult and time consuming, requiring personnel to manually check a trap’s status multiple times per day, amounting to over six hours of manual labor. Victor is looking for an innovative way to increase operational efficiencies with the use of technology.