Technology Category
- Networks & Connectivity - Bluetooth
- Sensors - Liquid Detection Sensors
Applicable Industries
- Life Sciences
- Oil & Gas
Applicable Functions
- Product Research & Development
- Quality Assurance
Use Cases
- Smart Lighting
- Time Sensitive Networking
Services
- Testing & Certification
- Training
About The Customer
KONE Coal Valley is a branch of KONE, a world-leading manufacturer of elevators, escalators, and autowalks. The company is dedicated to the advancement of urban flow and is a force to be reckoned with in the urban development sphere. KONE Coal Valley is known for pushing the boundaries of what is possible for highly populated areas. They have won the Elevator World Project of the Year Award and a $179-Million escalator contract in Washington D.C. The company is always pushing for innovation and has plans for continued growth and utilization of VKS.
The Challenge
KONE Coal Valley, a leading manufacturer of elevators and escalators, faced two significant challenges before their digital transformation. Firstly, their work instructions were distributed on paper within multiple binders, making it difficult to update and keep track of the best and most current practices. Secondly, with a significant portion of their workforce set to retire in the coming years, they had to hire a new generation of workers who lacked the necessary experience. The company needed a solution that would enable them to transfer the knowledge and experience of their senior employees to their new hires before they retired. These challenges were not unique to KONE Coal Valley alone but are common issues that many modern manufacturers face daily.
The Solution
KONE Coal Valley implemented VKS, a work instruction software, to mitigate these challenges. The software provided digital resources that could be updated with a click of a button, empowering employees to perform the right work, at the right time, with the right knowledge. The company leveraged the software to integrate smart manufacturing practices, resulting in significant operational efficiency and flow. They used VKS to document their best practices and capture the tribal knowledge developed over the years. They also developed a special hardware setup that enabled their operators to see the work instructions from anywhere in the workstation. The company used VKS Smart Forms to reduce material bottlenecks within their operation and to supplement their new training curriculum. They also leveraged VKS to enact dynamic and direct Andon measures on their shop floor, track massive amounts of accurate production data, and give their operators a voice in creating and documenting their best practices.
Operational Impact
Quantitative Benefit
Case Study missing?
Start adding your own!
Register with your work email and create a new case study profile for your business.
Related Case Studies.
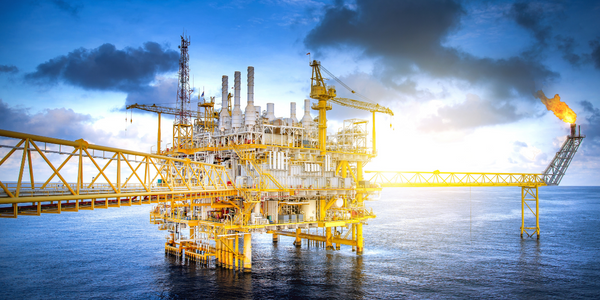
Case Study
Taking Oil and Gas Exploration to the Next Level
DownUnder GeoSolutions (DUG) wanted to increase computing performance by 5 to 10 times to improve seismic processing. The solution must build on current architecture software investments without sacrificing existing software and scale computing without scaling IT infrastructure costs.
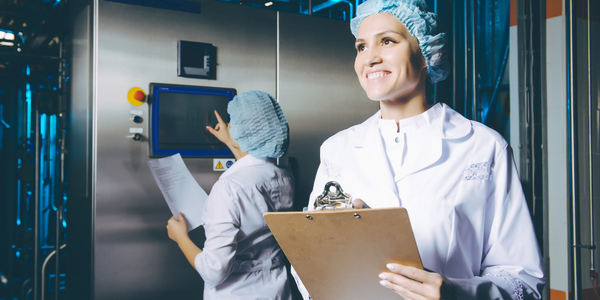
Case Study
Remote Wellhead Monitoring
Each wellhead was equipped with various sensors and meters that needed to be monitored and controlled from a central HMI, often miles away from the assets in the field. Redundant solar and wind generators were installed at each wellhead to support the electrical needs of the pumpstations, temperature meters, cameras, and cellular modules. In addition to asset management and remote control capabilities, data logging for remote surveillance and alarm notifications was a key demand from the customer. Terra Ferma’s solution needed to be power efficient, reliable, and capable of supporting high-bandwidth data-feeds. They needed a multi-link cellular connection to a central server that sustained reliable and redundant monitoring and control of flow meters, temperature sensors, power supply, and event-logging; including video and image files. This open-standard network needed to interface with the existing SCADA and proprietary network management software.
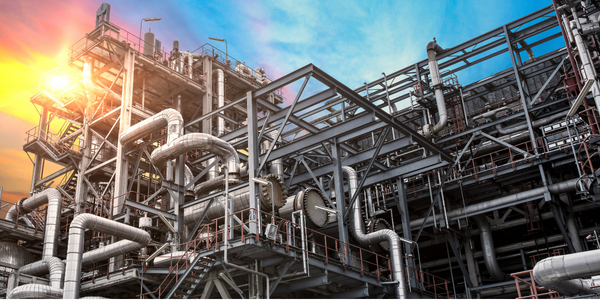
Case Study
Refinery Saves Over $700,000 with Smart Wireless
One of the largest petroleum refineries in the world is equipped to refine various types of crude oil and manufacture various grades of fuel from motor gasoline to Aviation Turbine Fuel. Due to wear and tear, eight hydrogen valves in each refinery were leaking, and each cost $1800 per ton of hydrogen vented. The plant also had leakage on nearly 30 flare control hydrocarbon valves. The refinery wanted a continuous, online monitoring system that could catch leaks early, minimize hydrogen and hydrocarbon production losses, and improve safety for maintenance.