Leading Construction Equipment Manufacturer Improves Service Delivery and Revenue Using Data Virtualization
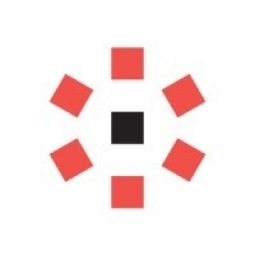
Customer Company Size
Large Corporate
Country
- United States
Product
- Denodo Platform
Tech Stack
- Data Virtualization
- Telematics
- Predictive Analytics
- Big Data
Implementation Scale
- Enterprise-wide Deployment
Impact Metrics
- Revenue Growth
- Productivity Improvements
- Customer Satisfaction
Technology Category
- Analytics & Modeling - Data-as-a-Service
- Analytics & Modeling - Predictive Analytics
Applicable Industries
- Construction & Infrastructure
- Mining
Applicable Functions
- Maintenance
- Logistics & Transportation
Use Cases
- Predictive Maintenance
- Asset Health Management (AHM)
- Fleet Management
Services
- Data Science Services
About The Customer
The Company is the world’s largest construction equipment manufacturer. It engages in the manufacture of construction and mining equipment, diesel and natural gas engines, industrial gas turbines, and diesel-electric locomotives. The Company provides technology for construction, transportation, mining, energy, logistics, and electric power generation. It distributes its products and services through a dealer network consisting of 172 dealers that serve 190 countries. The Company has over 95,000 employees and recorded $38.5B revenue in 2016. The Company is known for its manufacturing prowess and high-quality equipment. It strives to stay ahead of the competition in the Internet of Things (IoT) era by providing the highest quality field maintenance and machinery servicing.
The Challenge
The Company, a leading construction equipment manufacturer, was facing challenges due to sluggish sales and competition from low-cost alternatives. The Company's customers were demanding high returns on their investments with minimum downtime and maintenance. To meet these demands, The Company needed to optimize asset performance and reduce machinery part breakdown in the field. The Company had invested in modern tools and technologies for telematics and predictive analytics, and in field sensors and big data technology. However, the field equipment data needed to be analyzed constantly in real time against the backdrop of service life records, warranty data, and other information. Traditional data integration methods were proving to be slow and expensive. The Company needed an agile data integration and access layer that could easily integrate big data with other sources of enterprise or cloud data in real time.
The Solution
The Company adopted the Denodo Platform for data virtualization. The data virtualization layer combines the streaming data with operational data to deliver meaningful information to business users through interactive dashboards and reporting tools that sit on top of the data access layer. In addition, while the purchasing department's historical spend data is built on top of the purchasing data marts, and updated on a monthly basis using ETL processes, the data virtualization layer combines real-time analytical data and buyer information, streamlining global purchase business partners' monthly spend and order information. The data virtualization layer is also the foundation for creating The Company's telematics data service, which can be sold to The Company's customers and distributors in a Data-as-a-Service (DaaS) model.
Operational Impact
Quantitative Benefit
Case Study missing?
Start adding your own!
Register with your work email and create a new case study profile for your business.
Related Case Studies.
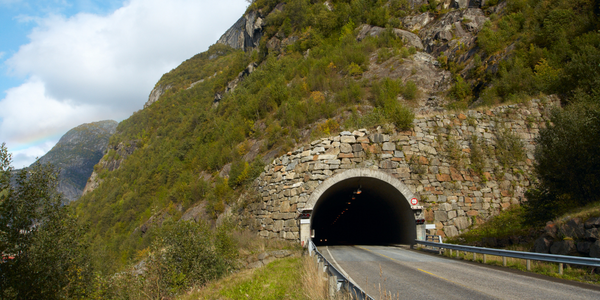
Case Study
IoT System for Tunnel Construction
The Zenitaka Corporation ('Zenitaka') has two major business areas: its architectural business focuses on structures such as government buildings, office buildings, and commercial facilities, while its civil engineering business is targeted at structures such as tunnels, bridges and dams. Within these areas, there presented two issues that have always persisted in regard to the construction of mountain tunnels. These issues are 'improving safety" and "reducing energy consumption". Mountain tunnels construction requires a massive amount of electricity. This is because there are many kinds of electrical equipment being used day and night, including construction machinery, construction lighting, and ventilating fan. Despite this, the amount of power consumption is generally not tightly managed. In many cases, the exact amount of power consumption is only ascertained when the bill from the power company becomes available. Sometimes, corporations install demand-monitoring equipment to help curb the maximum power demanded. However, even in these cases, the devices only allow the total volume of power consumption to be ascertained, or they may issue warnings to prevent the contracted volume of power from being exceeded. In order to tackle the issue of reducing power consumption, it was first necessary to obtain an accurate breakdown of how much power was being used in each particular area. In other words, we needed to be able to visualize the amount of power being consumed. Safety, was also not being managed very rigorously. Even now, tunnel construction sites often use a 'name label' system for managing entry into the work site. Specifically, red labels with white reverse sides that bear the workers' names on both sides are displayed at the tunnel work site entrance. The workers themselves then flip the name label to the appropriate side when entering or exiting from the work site to indicate whether or not they are working inside the tunnel at any given time. If a worker forgets to flip his or her name label when entering or exiting from the tunnel, management cannot be performed effectively. In order to tackle the challenges mentioned above, Zenitaka decided to build a system that could improve the safety of tunnel construction as well as reduce the amount of power consumed. In other words, this new system would facilitate a clear picture of which workers were working in each location at the mountain tunnel construction site, as well as which processes were being carried out at those respective locations at any given time. The system would maintain the safety of all workers while also carefully controlling the electrical equipment to reduce unnecessary power consumption. Having decided on the concept, our next concern was whether there existed any kind of robust hardware that would not break down at the construction work site, that could move freely in response to changes in the working environment, and that could accurately detect workers and vehicles using radio frequency identification (RFID). Given that this system would involve many components that were new to Zenitaka, we decided to enlist the cooperation of E.I.Sol Co., Ltd. ('E.I.Sol') as our joint development partner, as they had provided us with a highly practical proposal.
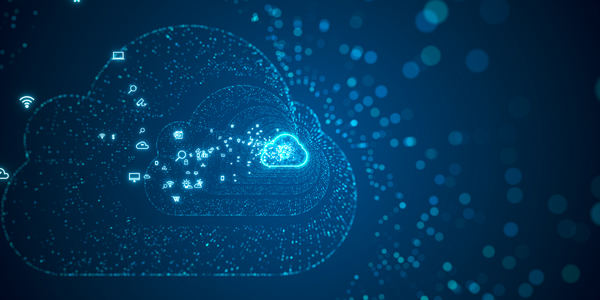
Case Study
Splunk Partnership Ties Together Big Data & IoT Services
Splunk was faced with the need to meet emerging customer demands for interfacing IoT projects to its suite of services. The company required an IoT partner that would be able to easily and quickly integrate with its Splunk Enterprise platform, rather than allocating development resources and time to building out an IoT interface and application platform.
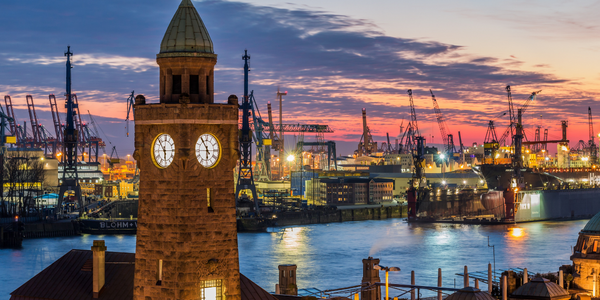
Case Study
Bridge monitoring in Hamburg Port
Kattwyk Bridge is used for both rail and road transport, and it has played an important role in the Port of Hamburg since 1973. However, the increasing pressure from traffic requires a monitoring solution. The goal of the project is to assess in real-time the bridge's status and dynamic responses to traffic and lift processes.
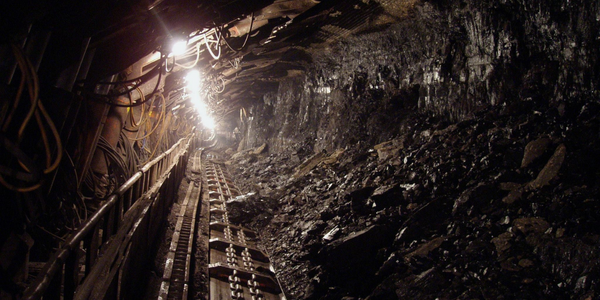
Case Study
Underground Mining Safety
The goal was to produce a safety system to monitor and support underground mining operations; existing systems were either too simple (i.e. phone line) or overly complex and expensive, inhibiting deployment, and providing little-to-no support in event of an accident. Given the dangerous nature of the mining work environment and the strict regulations placed on the industry, the solution would have to comply with Mine Safety and Health Administration (MSHA) regulations. Yet the product needed to allow for simple deployment to truly be a groundbreaking solution - increasing miner safety and changing daily operations for the better.
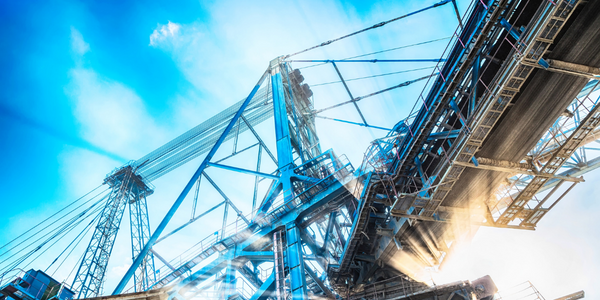
Case Study
Mining Firm Quadruples Production, with Internet of Everything
Dundee Precious Metal’s flagship mine, in Chelopech, Bulgaria, produces a gold, copper, and silver concentrate set a goal to increase production by 30%. Dundee wanted to increase production quality and output without increasing headcount and resources, improve miner safety, and minimize cost.
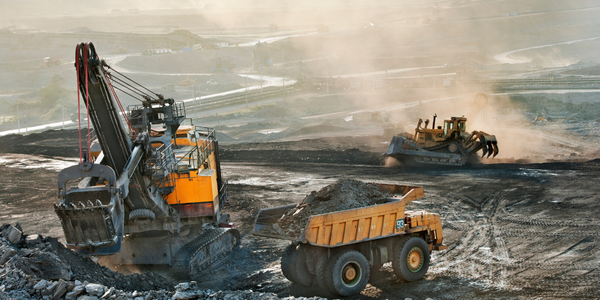
Case Study
Fastenal Builds the Future of Manufacturing with MachineMetrics
Fastenal's objective was to better understand their machine downtime, utilization, quality issues, and to embrace cutting-edge manufacturing technology/process improvement capabilities to bring their team to the next level. However, there was a lack of real-time data, visualization, and actionable insights made this transition impossible.