Technology Category
- Sensors - Electrical Conductivity Sensors
- Sensors - Level Sensors
Applicable Industries
- Electrical Grids
- Electronics
Use Cases
- Inventory Management
- Time Sensitive Networking
Services
- System Integration
About The Customer
KVA Group is a Queensland-based electrical company that was founded in 2015 by Ben Davis and Elliott Furlong. The company specializes in residential electrical work, commercial shop fit-outs, air conditioning, and solar collection system installations. Recently, the company has seen a significant increase in renovation work, with jobs ranging from $50,000 to high-end home renovations worth between $2 and $3 million. In just eight months, the company experienced a 65% increase in home security and automation jobs. To manage this increased workload, the company had to hire six new employees and acquire two extra vehicles. The co-directors also had to redefine their roles to manage the business more effectively.
The Challenge
KVA Group, a Queensland-based electrical company, was experiencing a significant increase in workload due to a boom in home renovation work across Australia and New Zealand. This surge was a result of the COVID-19 travel bans, which led people to invest their money in home improvements. KVA Group, which specializes in residential electrical work, commercial shop fit-outs, air conditioning, and solar collection system installations, saw a 65% increase in home security and automation jobs in just eight months. The company was struggling to manage this massive spike in workload, which led to the need for hiring six new employees and acquiring two extra vehicles. The co-directors had to redefine their roles, with one stepping into a business management role and the other becoming a construction manager. The company was also facing challenges in team management, job delegation, scheduling, and payroll.
The Solution
To manage the increased workload and streamline operations, KVA Group implemented Fergus, a job management software. This software transformed the company's operations from manual, shed meetings to cloud-based team management. Fergus enabled the co-directors to delegate tasks, schedule jobs for their staff, and manage the team remotely. The company's bookkeeper also started using Fergus, which provided all necessary information within the system, eliminating the need to consult the co-directors. This software also eased the burden of payroll management. Furthermore, KVA Group integrated Fergus with their wholesalers, including Lawrence & Hanson and Haymans, ensuring that the suppliers’ CSV price books were always accessible to the team. Fergus also helped the company manage pricing at a time when the cost of materials was fluctuating almost daily.
Operational Impact
Quantitative Benefit
Case Study missing?
Start adding your own!
Register with your work email and create a new case study profile for your business.
Related Case Studies.
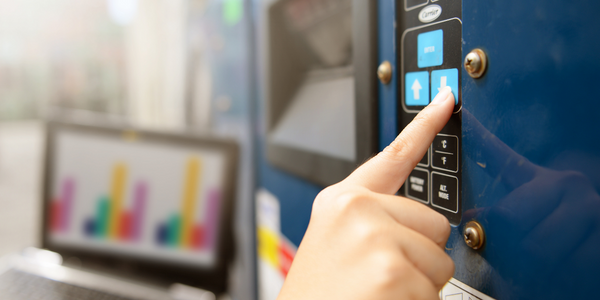
Case Study
Remote Temperature Monitoring of Perishable Goods Saves Money
RMONI was facing temperature monitoring challenges in a cold chain business. A cold chain must be established and maintained to ensure goods have been properly refrigerated during every step of the process, making temperature monitoring a critical business function. Manual registration practice can be very costly, labor intensive and prone to mistakes.
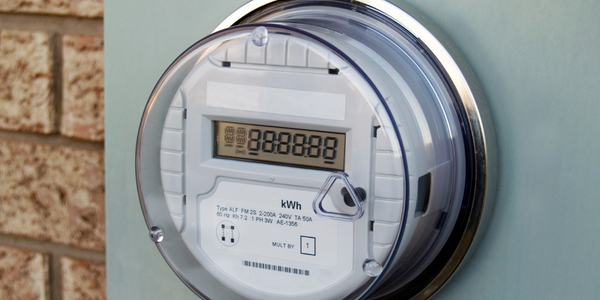
Case Study
Hydro One Leads the Way In Smart Meter Development
In 2010, Ontario’s energy board mandated that time-of-use (TOU) pricing for consumers be available for all consumers on a regulated price plan. To meet this requirement, Hydro One needed to quickly deploy a smart meter and intelligent communications network solution to meet the provincial government’s requirement at a low cost. The network needed to cover Hydro One’s expansive service territory, which has a land mass twice the size of Texas, and its customers live in a mix of urban, rural, and remote areas, some places only accessible by air, rail, boat or snowmobile. Most importantly, the network needed to enable future enterprise-wide business efficiencies, modernization of distribution infrastructure and enhanced customer service. To meet these needs, Hydro One conceptualized an end-to-end solution leveraging open standards and Internet Protocols (IP) at all communication levels. The utility drew upon industry leaders like Trilliant to realize this vision.
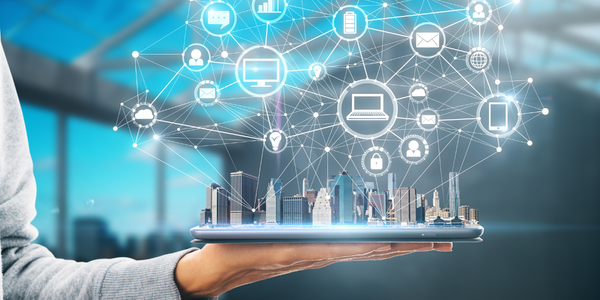
Case Study
Selling more with Whirlpool
Whirlpool wanted to add connectivity to appliances and transform the company's relationship with customers. Traditionally, Whirlpool interaction with customers was limited to purchases made once every ten years. Connected washer and dryers provide exciting new features like remote management of start times and inter-machine communication.
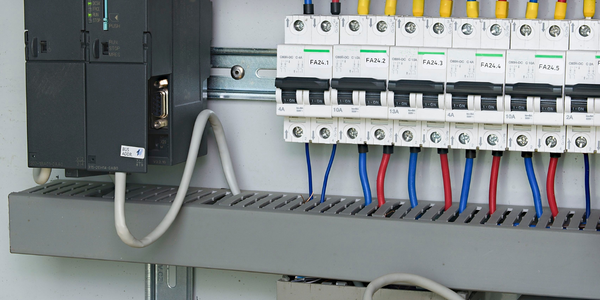
Case Study
Predictive maintenance in Schneider Electric
Schneider Electric Le Vaudreuil factory in France is recognized by the World Economic Forum as one of the world’s top nine most advanced “lighthouse” sites, applying Fourth Industrial Revolution technologies at large scale. It was experiencing machine-health and unplanned downtime issues on a critical machine within their manufacturing process. They were looking for a solution that could easily leverage existing machine data feeds, be used by machine operators without requiring complex setup or extensive training, and with a fast return on investment.