Customer Company Size
Large Corporate
Region
- Europe
Country
- Switzerland
Product
- IBM Maximo Asset Management
- IBM Maximo Everyplace
Tech Stack
- Predictive Analytics
- Mobile Technology
Implementation Scale
- Enterprise-wide Deployment
Impact Metrics
- Cost Savings
- Productivity Improvements
Technology Category
- Functional Applications - Enterprise Asset Management Systems (EAM)
- Analytics & Modeling - Predictive Analytics
Applicable Industries
- Retail
Applicable Functions
- Maintenance
Use Cases
- Predictive Maintenance
- Asset Health Management (AHM)
Services
- System Integration
- Data Science Services
About The Customer
Migros Zurich (GMZ) is a major retailer in Switzerland, operating 97 stores, 26 specialty markets, and 47 food outlets. The company serves around 1.5 million customers and generates annual revenues of around CHF 2.47 billion (USD 2.5 billion). GMZ employs about 8,800 people. The company's reputation rests on its ability to provide high-quality goods and services at reasonable prices with clockwork efficiency. However, the company's maintenance practices were proving costly, leading to the recognition of the need for a proactive strategy to optimize the performance, reliability, and longevity of enterprise assets.
The Challenge
Migros Zurich (GMZ) operates a vast network of stores, specialty markets, and food outlets, serving around 1.5 million customers. The company's reputation rests on its ability to provide high-quality goods and services at reasonable prices with clockwork efficiency. However, the company's maintenance staff needed a way to aggregate, consolidate, and analyze information from asset inventories, service requests, work orders, maintenance records, equipment service contracts, warranties, service level agreements, and service and technical documentation, much of it archived in physical form in the company's central offices. These records contained thousands of data points needed to gain a comprehensive understanding of the current condition of its resources and transform its maintenance practices from reactive to proactive. In addition, to promote efficiency in the field, the company needed a mobile solution that would provide field technicians with anywhere, real-time access to the company’s asset management system.
The Solution
To transform its asset management operations, Migros Zurich engaged IBM and IBM Business Partner, Ascom Solutions, to implement an analytics-based solution built on IBM® Maximo® Asset Management and IBM Maximo Everyplace® software, which offer a comprehensive view of company assets. Ascom Solutions provided excellent consulting and implementation services during the deployment. GMZ now uses predictive analytics to assess years of maintenance data and accurately determine asset lifecycles. Maintenance analysts can assess facility, system, and equipment health across the company to better predict when systems will require maintenance, repair, or replacement. With these insights, Migros Zürich can prioritize and schedule maintenance tasks to extend the service-life of individual assets and optimize the allocation of staff needed to maintain them. The solution integrates service contracts, warranties, SLAs, and historical service records that were previously inaccessible to maintenance teams in the field. Now, technicians can access these and technical manuals and diagrams remotely using mobile devices, such as smartphones and tablets from the site of service calls, eliminating the need for time-consuming office visits to consult hardcopy documentation.
Operational Impact
Case Study missing?
Start adding your own!
Register with your work email and create a new case study profile for your business.
Related Case Studies.
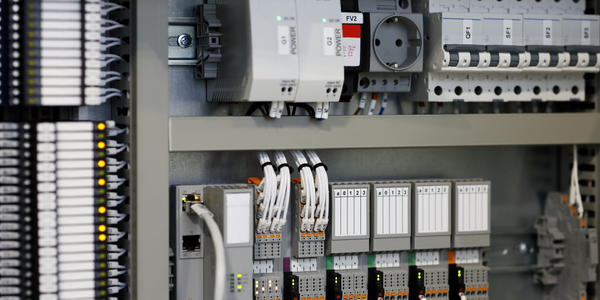
Case Study
Improving Production Line Efficiency with Ethernet Micro RTU Controller
Moxa was asked to provide a connectivity solution for one of the world's leading cosmetics companies. This multinational corporation, with retail presence in 130 countries, 23 global braches, and over 66,000 employees, sought to improve the efficiency of their production process by migrating from manual monitoring to an automatic productivity monitoring system. The production line was being monitored by ABB Real-TPI, a factory information system that offers data collection and analysis to improve plant efficiency. Due to software limitations, the customer needed an OPC server and a corresponding I/O solution to collect data from additional sensor devices for the Real-TPI system. The goal is to enable the factory information system to more thoroughly collect data from every corner of the production line. This will improve its ability to measure Overall Equipment Effectiveness (OEE) and translate into increased production efficiencies. System Requirements • Instant status updates while still consuming minimal bandwidth to relieve strain on limited factory networks • Interoperable with ABB Real-TPI • Small form factor appropriate for deployment where space is scarce • Remote software management and configuration to simplify operations
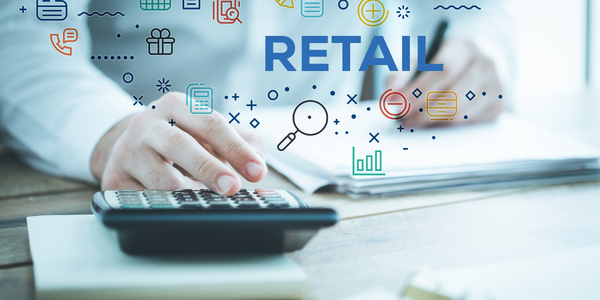
Case Study
Digital Retail Security Solutions
Sennco wanted to help its retail customers increase sales and profits by developing an innovative alarm system as opposed to conventional connected alarms that are permanently tethered to display products. These traditional security systems were cumbersome and intrusive to the customer shopping experience. Additionally, they provided no useful data or analytics.
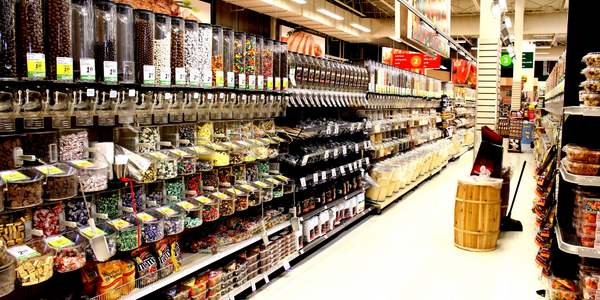
Case Study
How Sirqul’s IoT Platform is Crafting Carrefour’s New In-Store Experiences
Carrefour Taiwan’s goal is to be completely digital by end of 2018. Out-dated manual methods for analysis and assumptions limited Carrefour’s ability to change the customer experience and were void of real-time decision-making capabilities. Rather than relying solely on sales data, assumptions, and disparate systems, Carrefour Taiwan’s CEO led an initiative to find a connected IoT solution that could give the team the ability to make real-time changes and more informed decisions. Prior to implementing, Carrefour struggled to address their conversion rates and did not have the proper insights into the customer decision-making process nor how to make an immediate impact without losing customer confidence.
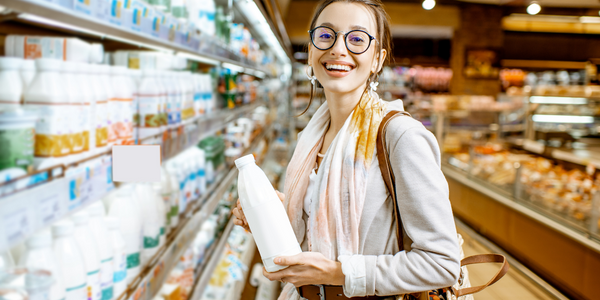
Case Study
Ensures Cold Milk in Your Supermarket
As of 2014, AK-Centralen has over 1,500 Danish supermarkets equipped, and utilizes 16 operators, and is open 24 hours a day, 365 days a year. AK-Centralen needed the ability to monitor the cooling alarms from around the country, 24 hours a day, 365 days a year. Each and every time the door to a milk cooler or a freezer does not close properly, an alarm goes off on a computer screen in a control building in southwestern Odense. This type of alarm will go off approximately 140,000 times per year, equating to roughly 400 alarms in a 24-hour period. Should an alarm go off, then there is only a limited amount of time to act before dairy products or frozen pizza must be disposed of, and this type of waste can quickly start to cost a supermarket a great deal of money.
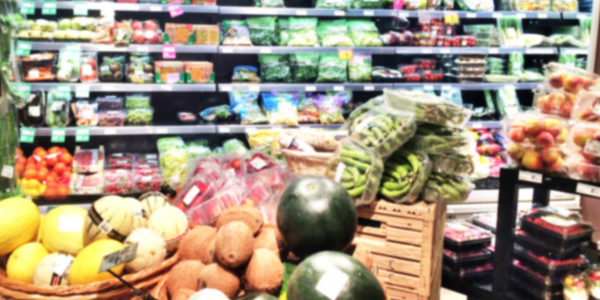
Case Study
Supermarket Energy Savings
The client had previously deployed a one-meter-per-store monitoring program. Given the manner in which energy consumption changes with external temperature, hour of the day, day of week and month of year, a single meter solution lacked the ability to detect the difference between a true problem and a changing store environment. Most importantly, a single meter solution could never identify root cause of energy consumption changes. This approach never reduced the number of truck-rolls or man-hours required to find and resolve issues.