Technology Category
- Functional Applications - Enterprise Resource Planning Systems (ERP)
- Functional Applications - Manufacturing Execution Systems (MES)
Applicable Industries
- Automotive
- Buildings
Applicable Functions
- Maintenance
- Quality Assurance
Use Cases
- Factory Operations Visibility & Intelligence
- Visual Quality Detection
Services
- System Integration
- Testing & Certification
About The Customer
Mitsubishi Electric is a leading elevator manufacturer with over 65 years of experience in the Japanese market. The company has recently expanded its customer base to include the demanding European market, catering to various sectors including office and home buildings, hospitality, and healthcare. Mitsubishi Electric is known for its innovative approach to elevator design and manufacturing, focusing on quality, speed, and environmental sustainability. The company's elevators are designed to last 25 to 40 years, depending on the model, and have the lowest breakdown rate in the Netherlands. Mitsubishi Electric was an early adopter of Smart Factory and IoT technology, and its factory in Veenendaal, The Netherlands, is a testament to its commitment to strategic innovation and quality.
The Challenge
Mitsubishi Electric, a leading elevator manufacturer, faced a complex challenge when scaling up production for its new MOVE elevator system, designed specifically for the European market. The MOVE elevators were quite different from the standard Japanese model, requiring new assembly processes. The company needed to standardize these processes to ensure high-quality production and maintain its reputation for reliability. However, initial efforts to standardize the shop floor were burdensome for the experienced workers, who were more comfortable with their individual routines. Furthermore, the company lacked a reliable data capturing system that could provide valuable feedback for analysis. The challenge was to implement a system that could streamline the new step-by-step instructions for the MOVE models, capture data for analysis, and be easily accepted by the workforce.
The Solution
Mitsubishi Electric turned to VKS Enterprise’s digitized work instructions software to standardize their assembly line. The software provided a multifunctional system that streamlined the new step-by-step instructions for the MOVE models. It also allowed workers to physically approve critical steps through interactive forms within the work instructions, providing accountability throughout the shop floor. In case of any errors, they could be immediately traced back to the individual who performed that step. VKS’ Smart Forms feature also increased traceability in the production life cycle. The company also implemented VKS’ ToolConnect feature, which ensured proper assembly by communicating with intelligent torque tools using open protocol. This feature provided a failsafe for quality control and helped to complete a full device history record for each elevator in every batch shipped out. The VKS software not only standardized the production process but also transformed the shop floor into a fully integrated Smart Factory.
Operational Impact
Quantitative Benefit
Case Study missing?
Start adding your own!
Register with your work email and create a new case study profile for your business.
Related Case Studies.
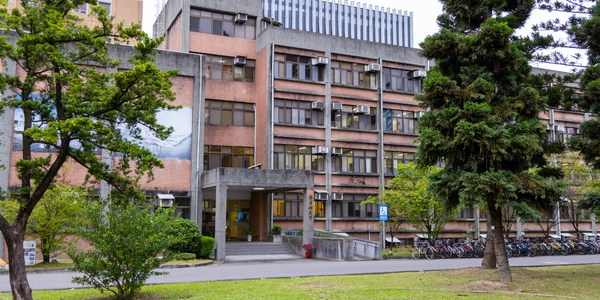
Case Study
Energy Saving & Power Monitoring System
Recently a university in Taiwan was experiencing dramatic power usage increases due to its growing number of campus buildings and students. Aiming to analyze their power consumption and increase their power efficiency across 52 buildings, the university wanted to build a power management system utilizing web-based hardware and software. With these goals in mind, they contacted Advantech to help them develop their system and provide them with the means to save energy in the years to come.
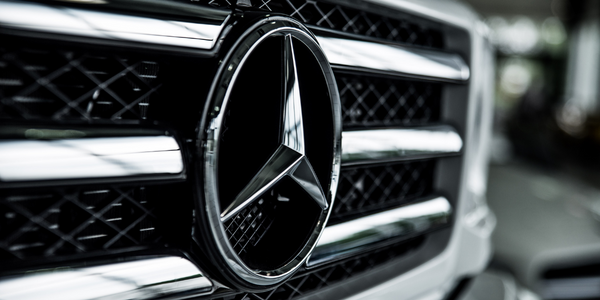
Case Study
Integral Plant Maintenance
Mercedes-Benz and his partner GAZ chose Siemens to be its maintenance partner at a new engine plant in Yaroslavl, Russia. The new plant offers a capacity to manufacture diesel engines for the Russian market, for locally produced Sprinter Classic. In addition to engines for the local market, the Yaroslavl plant will also produce spare parts. Mercedes-Benz Russia and his partner needed a service partner in order to ensure the operation of these lines in a maintenance partnership arrangement. The challenges included coordinating the entire maintenance management operation, in particular inspections, corrective and predictive maintenance activities, and the optimizing spare parts management. Siemens developed a customized maintenance solution that includes all electronic and mechanical maintenance activities (Integral Plant Maintenance).
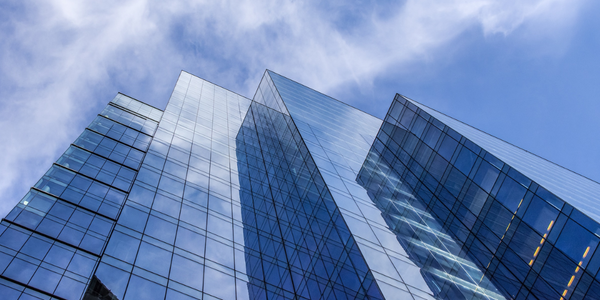
Case Study
Intelligent Building Automation System and Energy Saving Solution
One of the most difficult problems facing the world is conserving energy in buildings. However, it is not easy to have a cost-effective solution to reduce energy usage in a building. One solution for saving energy is to implement an intelligent building automation system (BAS) which can be controlled according to its schedule. In Indonesia a large university with a five floor building and 22 classrooms wanted to save the amount of energy being used.