Applicable Industries
- Cement
- Pharmaceuticals
Use Cases
- Chatbots
- Leasing Finance Automation
About The Customer
Netmeds is one of India's most trusted and convenient pharmacies, with a founding family that has over 100 years of experience in dispensing quality medicines. The company experienced a significant surge in traffic during the COVID-19 pandemic, with its customer base growing tenfold. Netmeds offers a wide range of pharmaceutical products and services, and it needed a solution to manage the increased demand and provide round-the-clock support to its customers. The company is committed to providing quality customer service and aimed to improve its resolution rate and first-response time.
The Challenge
Netmeds, one of India's most trusted pharmacies, faced a significant challenge during the height of the COVID-19 pandemic. The company experienced a tenfold increase in its customer base, leading to a surge in incoming traffic and a consequent increase in agent load. The company was struggling to handle the increased demand and needed to automate simple queries to reduce the load on its agents. Additionally, Netmeds was under pressure to offer 24/7 customer support to address the round-the-clock queries about medicines, prescriptions, and more. The company also aimed to improve its resolution rate and first-response time (FRT) to enhance customer satisfaction.
The Solution
To address these challenges, Netmeds partnered with Haptik to build a chatbot capable of handling its core issues. Haptik's solution was designed to offer a strong and consistent experience to Netmeds' customers while helping the company build long-lasting relationships with its customers. The chatbot provided 24/7 support for Netmeds' 5.7 million customers, managing 4800 chats per day via automation and routing to human agents where necessary. This allowed Netmeds' customers to easily track and manage their orders and get instant information by directly chatting with the virtual assistant. The solution was designed to handle the surge in demand caused by the pandemic, saving agent hours and improving first-response time.
Operational Impact
Quantitative Benefit
Case Study missing?
Start adding your own!
Register with your work email and create a new case study profile for your business.
Related Case Studies.
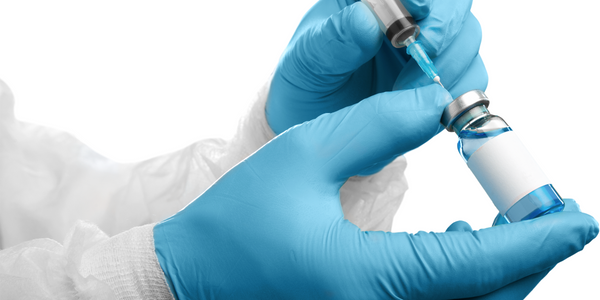
Case Study
Case Study: Pfizer
Pfizer’s high-performance computing software and systems for worldwide research and development support large-scale data analysis, research projects, clinical analytics, and modeling. Pfizer’s computing services are used across the spectrum of research and development efforts, from the deep biological understanding of disease to the design of safe, efficacious therapeutic agents.
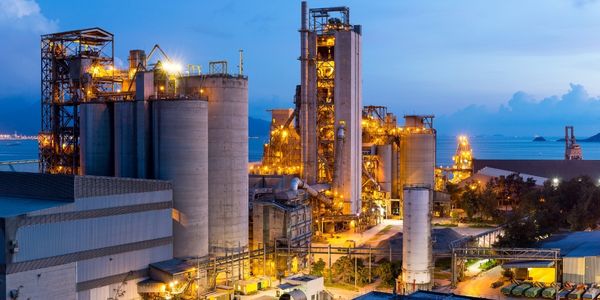
Case Study
System 800xA at Indian Cement Plants
Chettinad Cement recognized that further efficiencies could be achieved in its cement manufacturing process. It looked to investing in comprehensive operational and control technologies to manage and derive productivity and energy efficiency gains from the assets on Line 2, their second plant in India.
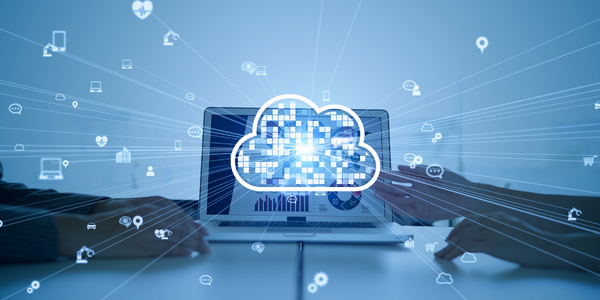
Case Study
Fusion Middleware Integration on Cloud for Pharma Major
Customer wanted a real-time, seamless, cloud based integration between the existing on premise and cloud based application using SOA technology on Oracle Fusion Middleware Platform, a Contingent Worker Solution to collect, track, manage and report information for on-boarding, maintenance and off-boarding of contingent workers using a streamlined and Integrated business process, and streamlining of integration to the back-end systems and multiple SaaS applications.
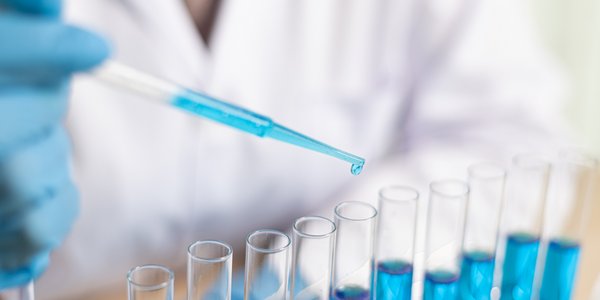
Case Study
Process Control System Support
In many automated production facilities, changes are made to SIMATIC PCS 7 projects on a daily basis, with individual processes often optimised by multiple workers due to shift changes. Documentation is key here, as this keeps workers informed about why a change was made. Furthermore, SIMATIC PCS 7 installations are generally used in locations where documentation is required for audits and certification. The ability to track changes between two software projects is not only an invaluable aid during shift changes, but also when searching for errors or optimising a PCS 7 installation. Every change made to the system is labour-intensive and time-consuming. Moreover, there is also the risk that errors may occur. If a change is saved in the project, then the old version is lost unless a backup copy was created in advance. If no backup was created, it will no longer be possible to return to the previous state if and when programming errors occur. Each backup denotes a version used by the SIMATIC PCS 7 system to operate an installation. To correctly interpret a version, information is required on WHO changed WHAT, WHERE, WHEN and WHY: - Who created the version/who is responsible for the version? - Who released the version? - What was changed in the version i.e. in which block or module of the SIMATIC PCS 7 installation were the changes made? - When was the version created? Is this the latest version or is there a more recent version? - Why were the changes made to the version? If they are part of a regular maintenance cycle, then is the aim to fix an error or to improve production processes? - Is this particular version also the version currently being used in production? The fact that SIMATIC PCS 7 projects use extremely large quantities of data complicates the situation even further, and it can take a long time to load and save information as a result. Without a sustainable strategy for operating a SIMATIC PCS 7 installation, searching for the right software version can become extremely time-consuming and the installation may run inefficiently as a result.