Customer Company Size
Large Corporate
Region
- America
Country
- United States
Product
- SimSci-Esscor Connoisseur Online Optimization
Tech Stack
- Model Predictive Control
- Neural Network Based controller
Implementation Scale
- Enterprise-wide Deployment
Impact Metrics
- Cost Savings
- Environmental Impact Reduction
- Productivity Improvements
Technology Category
- Analytics & Modeling - Predictive Analytics
Applicable Industries
- Utilities
Applicable Functions
- Maintenance
- Discrete Manufacturing
Use Cases
- Predictive Maintenance
- Energy Management System
Services
- System Integration
About The Customer
The Southern Mississippi Electric Power Association (SMEPA) is a power generation company based in Hattiesburg, Mississippi. They operate the R.D. Morrow Generating Station, which utilizes two parallel boiler-turbine units with a capacity of 204 MW at 2400 psig. The Riley Stoker Corporation manufactures each steam generator unit. Each has a turbo-furnace design with balanced draft operation, and is front and rear fired. Nominal steam conditions at HP turbine inlet are 2400 psig at 1005 DEGF and 1000 DEGF at the IP turbine inlet. Maximum continuous steam rate is 1,575,000 lhs/hr. The fuel is pulverized coal from three Riley doubleend ball tube mills fed by six Stock Gravimetric feeders.
The Challenge
The Southern Mississippi Electric Power Association (SMEPA) was facing a challenge of improving the heat rate and boiler efficiency while maintaining low NOx emissions at their R.D. Morrow Generating Station. The station utilizes two parallel boiler-turbine units with a capacity of 204 MW at 2400 psig. The fuel is pulverized coal from three Riley doubleend ball tube mills fed by six Stock Gravimetric feeders. The objective was to determine the most profitable operating point for the boiler and mills, as defined by a set of values for the controlled and manipulated variables in the process model.
The Solution
SMEPA implemented the Model Predictive and Neural Network Based controller, Connoisseur™ to improve efficiency at their Hattiesburg station. Both furnace and ball mill controls were optimized with coordinated multivariable control. Heat rate improvements were achieved through reduced dry gas losses and lower loss-on-ignition (LOI). In addition, the improved mill regulation increased maximum generation capability, particularly for lower grade coal. An Expert System Soot Blower Advisory supplements the heat rate benefits of applying Connoisseur™ by suggesting which blower to activate in order to maximize heat transfer area in the furnace. Ball mill optimization improves the grind in the mill, lowers LOI and improves the mill’s impact on the energy efficiency of the furnace.
Operational Impact
Quantitative Benefit
Case Study missing?
Start adding your own!
Register with your work email and create a new case study profile for your business.
Related Case Studies.

Case Study
IoT Solutions for Smart City | Internet of Things Case Study
There were several challenges faced: It is challenging to build an appliance that can withstand a wide range of voltage fluctuations from as low at 90v to as high as 320v. Since the device would be installed in remote locations, its resilience was of paramount importance. The device would have to deal with poor network coverage and have the ability to store and re-transmit data if networks were not available, which is often the case in rural India. The device could store up to 30 days of data.
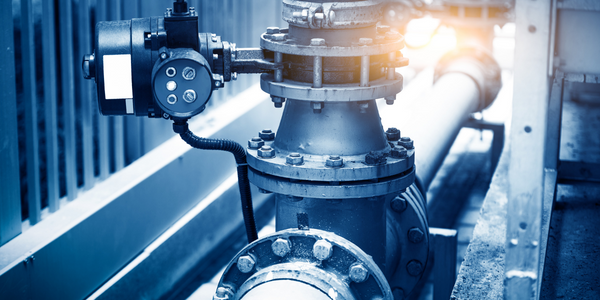
Case Study
Automation of the Oguz-Gabala-Baku water pipeline, Azerbaijan
The Oguz-Gabala-Baku water pipeline project dates back to plans from the 1970’s. Baku’s growth was historically driven by the booming oil industry and required the import of drinking water from outside of the city. Before the construction of the pipeline, some 60 percent of the city’s households received water for only a few hours daily. After completion of the project, 75 percent of the two million Baku residents are now served around the clock with potable water, based on World Health Organization (WHO) standards. The 262-kilometer pipeline requires no pumping station, but uses the altitude differences between the Caucasian mountains and the capital to supply 432,000 m³/d to the Ceyranbatan water reservoir. To the people of Baku, the pipeline is “the most important project not only in 2010, but of the last 20 years.”
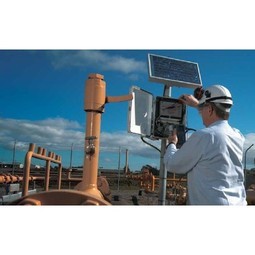
Case Study
GPRS Mobile Network for Smart Metering
Around the world, the electricity supply industry is turning to ‘smart’ meters to lower costs, reduce emissions and improve the management of customer supplies. Smart meters collect detailed consumption information and using this feedback consumers can better understand their energy usage which in turn enables them to modify their consumption to save money and help to cut carbon emissions. A smart meter can be defined in many ways, but generally includes an element of two-way communication between the household meter and the utility provider to efficiently collect detailed energy usage data. Some implementations include consumer feedback beyond the energy bill to include online web data, SMS text messages or an information display in consumers’ premises. Providing a cost-effective, reliable communications mechanism is one of the most challenging aspects of a smart meter implementation. In New Zealand, the utilities have embraced smart metering and designed cost effective ways for it to be implemented. The New Zealand government has encouraged such a move to smart metering by ensuring the energy legislation is consistent with the delivery of benefits to the consumer while allowing innovation in this area. On the ground, AMS is a leader in the deployment of smart metering and associated services. Several of New Zealand’s energy retailers were looking for smart metering services for their residential and small business customers which will eventually account for over 500,000 meters when the multi-year national deployment program is concluded. To respond to these requirements, AMS needed to put together a solution that included data communications between each meter and the central data collection point and the solution proposed by Vodafone satisfied that requirement.
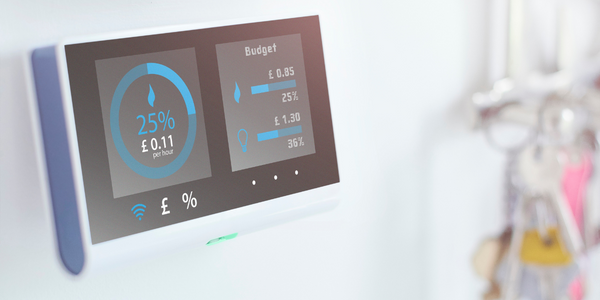
Case Study
NB-IoT connected smart meters to improve gas metering in Shenzhen
Shenzhen Gas has a large fleet of existing gas meters, which are installed in a variety of hard to reach locations, such as indoors and underground, meaning that existing communications networks have struggled to maintain connectivity with all meters. The meter success rate is low, data transmissions are so far unstable and power consumption is too high. Against this background, Shenzhen Gas, China Telecom, Huawei, and Goldcard have jointly trialed NB-IoT gas meters to try and solve some of the challenges that the industry faces with today’s smart gas meters.
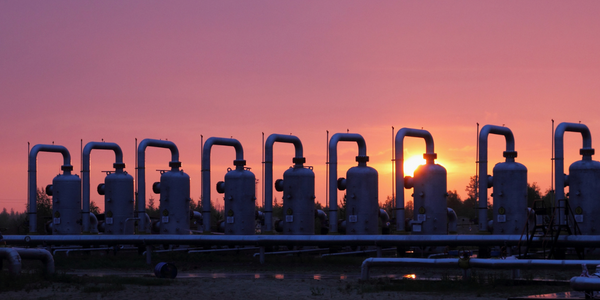
Case Study
British Gas Modernizes its Operations with Innovative Smart Metering Deployment
The UK government has mandated that smart meters are rolled out as standard across Great Britain by end of 2020, and this roll-out is estimated to create £14 billion in net benefits to the UK in consumer energy savings and lower energy generation demand, according to the Oxford Economics report, “The Value of Smart Metering to Great Britain.” While smart-metering systems have been deployed in many countries, the roll-out in Great Britain is unique because it is led by energy retailers, who have responsibility for the Electricity and Gas meters. The decision to have a retailer-led roll out was made by DECC (Department of Energy and Climate Change) to improve customer experience and drive consumer benefits. It has also led to some unique system-level requirements to support the unique local regulatory model.
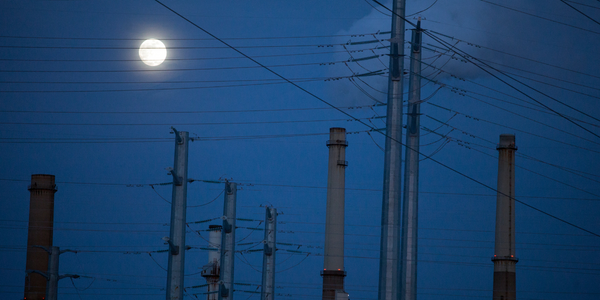
Case Study
OneWireless Enabled Performance Guarantee Test
Tata Power's power generation equipment OEMs (M/s BHEL) is required to provide all of the instrumentation and measurement devices for conducting performance guarantee and performance evaluation tests. M/s BHEL faced a number of specific challenges in conducting PG tests: employing high-accuracy digital communications for instrumentation, shortening setup and dismantling time, reducing hardware required, making portable instrument setup, avoiding temporary cabling work and the material waste costs