Technology Category
- Cybersecurity & Privacy - Security Compliance
Applicable Industries
- Automotive
- Transportation
Applicable Functions
- Logistics & Transportation
- Quality Assurance
Use Cases
- Last Mile Delivery
- Leasing Finance Automation
Services
- System Integration
About The Customer
Meadow is a cannabis dispensary platform operating in the rapidly growing cannabis industry. The company serves a market that has seen a surge in demand, particularly during the pandemic. Meadow is committed to optimizing its customer experience and addressing the unique challenges of the cannabis sector, including perishable inventory, limited marketing channels, and strict compliance requirements. The company initially used a complex 'Frankenstein' model of up to six different software systems to manage its operations. However, Meadow has now adopted Onfleet's delivery management software to streamline its operations and improve efficiency.
The Challenge
The cannabis industry has seen significant growth in recent years, spurred by state-level legalization initiatives and increased demand during the pandemic. However, the sector faces unique challenges, including perishable inventory, limited marketing channels, and the need for strict compliance with rapidly evolving laws and regulations. Cannabis retailers often struggle with complex logistics, with some using up to six different software systems to manage their operations. This 'Frankenstein' model is inefficient and costly. Additionally, the industry has been marked by racial and social inequalities, with laws unequally applied across racial and economic lines.
The Solution
Meadow, a cannabis dispensary platform, has adopted Onfleet's delivery management software to optimize its customer experience and address these challenges. Onfleet's software offers a high level of automation and organization, transforming the delivery process. Customers place their orders with Meadow, and the orders are passed from Meadow’s system through to Onfleet. Onfleet’s product features are built for efficiency, including its auto dispatch feature that eliminates the need for dispatchers to manually assign tasks from the system to delivery drivers. The software supports two main delivery models: the hub-and-spoke model, where orders are dispatched in groups, and the ice-cream truck model, where orders are dispatched directly to each car in the field. This new level of automation allows operators to run leaner, make more money, and use true-retention strategies through real-time texting in regions.
Operational Impact
Case Study missing?
Start adding your own!
Register with your work email and create a new case study profile for your business.
Related Case Studies.
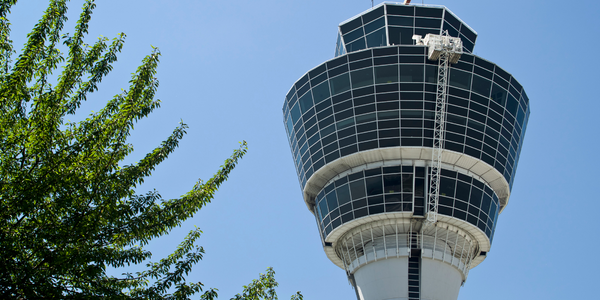
Case Study
Airport SCADA Systems Improve Service Levels
Modern airports are one of the busiest environments on Earth and rely on process automation equipment to ensure service operators achieve their KPIs. Increasingly airport SCADA systems are being used to control all aspects of the operation and associated facilities. This is because unplanned system downtime can cost dearly, both in terms of reduced revenues and the associated loss of customer satisfaction due to inevitable travel inconvenience and disruption.
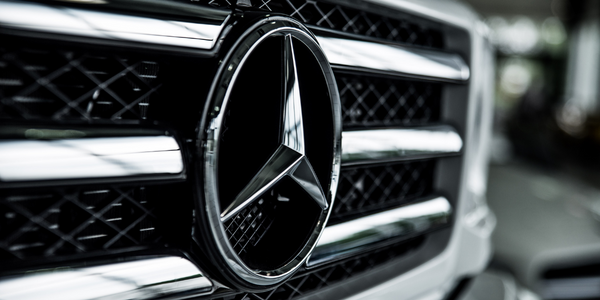
Case Study
Integral Plant Maintenance
Mercedes-Benz and his partner GAZ chose Siemens to be its maintenance partner at a new engine plant in Yaroslavl, Russia. The new plant offers a capacity to manufacture diesel engines for the Russian market, for locally produced Sprinter Classic. In addition to engines for the local market, the Yaroslavl plant will also produce spare parts. Mercedes-Benz Russia and his partner needed a service partner in order to ensure the operation of these lines in a maintenance partnership arrangement. The challenges included coordinating the entire maintenance management operation, in particular inspections, corrective and predictive maintenance activities, and the optimizing spare parts management. Siemens developed a customized maintenance solution that includes all electronic and mechanical maintenance activities (Integral Plant Maintenance).
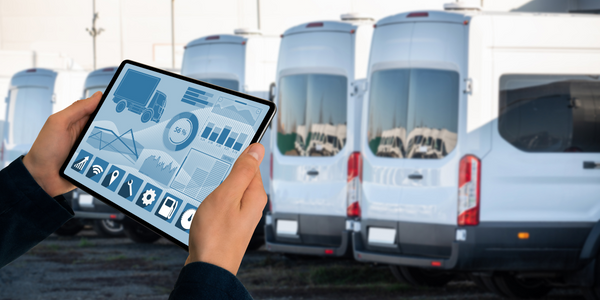
Case Study
IoT-based Fleet Intelligence Innovation
Speed to market is precious for DRVR, a rapidly growing start-up company. With a business model dependent on reliable mobile data, managers were spending their lives trying to negotiate data roaming deals with mobile network operators in different countries. And, even then, service quality was a constant concern.
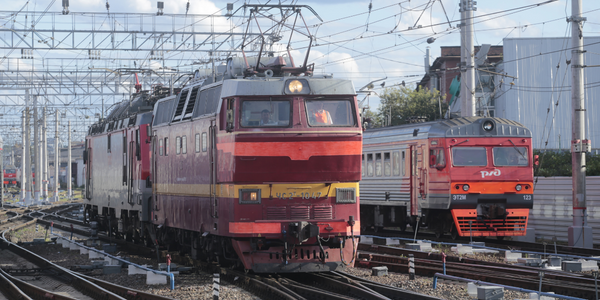
Case Study
Digitize Railway with Deutsche Bahn
To reduce maintenance costs and delay-causing failures for Deutsche Bahn. They need manual measurements by a position measurement system based on custom-made MEMS sensor clusters, which allow autonomous and continuous monitoring with wireless data transmission and long battery. They were looking for data pre-processing solution in the sensor and machine learning algorithms in the cloud so as to detect critical wear.
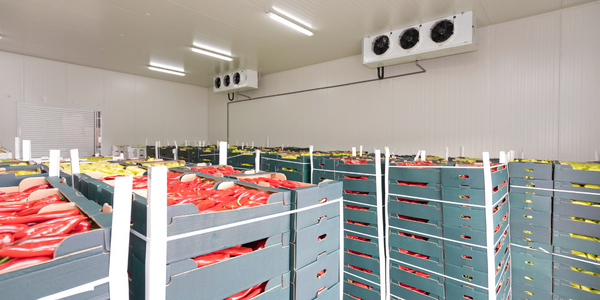
Case Study
Cold Chain Transportation and Refrigerated Fleet Management System
1) Create a digital connected transportation solution to retrofit cold chain trailers with real-time tracking and controls. 2) Prevent multi-million dollar losses due to theft or spoilage. 3) Deliver a digital chain-of-custody solution for door to door load monitoring and security. 4) Provide a trusted multi-fleet solution in a single application with granular data and access controls.