Customer Company Size
Large Corporate
Region
- America
- Asia
- Europe
- Africa
Country
- United States
- Belgium
- Brazil
- China
- Colombia
- Ghana
- Mexico
- Singapore
- South Africa
Product
- JDA® Warehouse Management
- JDA® Warehouse Labor Management
- JDA® Parcel
Tech Stack
- Warehouse Management System (WMS)
- Barcode Technology
- Radio Frequency Environment
Implementation Scale
- Enterprise-wide Deployment
Impact Metrics
- Productivity Improvements
- Cost Savings
Technology Category
- Functional Applications - Warehouse Management Systems (WMS)
Applicable Industries
- Automotive
Applicable Functions
- Warehouse & Inventory Management
Use Cases
- Warehouse Automation
- Inventory Management
Services
- Software Design & Engineering Services
- Training
About The Customer
Cummins is a leading global provider of diesel and natural gas engines and related technologies, with 2015 sales of $19.1 billion. Through its Cummins Global Logistics (CGL) unit, it ensures that replacement parts are readily available to Cummins distributors and original equipment manufacturer partners around the world. Providing aftermarket support to customers in approximately 190 countries requires a sophisticated distribution network. CGL is able to accomplish this feat due to the people, processes, supply chain management strategies and systems that it employs to manage its warehouse and distribution operations.
The Challenge
Cummins Global Logistics (CGL), a unit of Cummins, a leading global provider of diesel and natural gas engines and related technologies, was facing challenges in improving the efficiency of its warehouse operations to provide better aftermarket support for its customers. The company's in-house warehouse management system (WMS) was outdated and provided less automation than what was required to support the company’s growth. The company was in need of a sophisticated distribution network that could fulfill orders quickly and accurately to support customers in approximately 190 countries.
The Solution
CGL decided to update its warehouse management capabilities by implementing JDA Warehouse Management, part of JDA Software’s Intelligent Fulfillment solution. The solution features best-in-class warehouse management and barcode technology in a radio frequency environment, which enables CGL to better control and optimize material flow throughout its facilities. The real-time, system-directed picking, packing, cartonization, QA verification, staging, and pack-and-hold management and inventory traceability capabilities support a more efficient and cost-effective warehousing environment. Today, JDA Warehouse Management is a major component of Cummins Global Logistics’ Global Systems Suite (GSS), and supports both large and small logistics distribution centers (DCs) around the globe.
Operational Impact
Quantitative Benefit
Case Study missing?
Start adding your own!
Register with your work email and create a new case study profile for your business.
Related Case Studies.
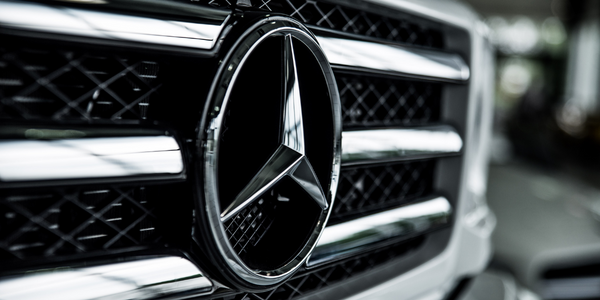
Case Study
Integral Plant Maintenance
Mercedes-Benz and his partner GAZ chose Siemens to be its maintenance partner at a new engine plant in Yaroslavl, Russia. The new plant offers a capacity to manufacture diesel engines for the Russian market, for locally produced Sprinter Classic. In addition to engines for the local market, the Yaroslavl plant will also produce spare parts. Mercedes-Benz Russia and his partner needed a service partner in order to ensure the operation of these lines in a maintenance partnership arrangement. The challenges included coordinating the entire maintenance management operation, in particular inspections, corrective and predictive maintenance activities, and the optimizing spare parts management. Siemens developed a customized maintenance solution that includes all electronic and mechanical maintenance activities (Integral Plant Maintenance).
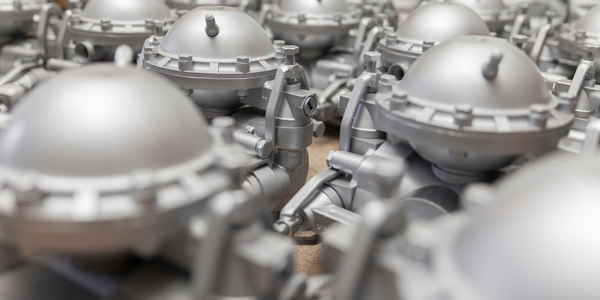
Case Study
Monitoring of Pressure Pumps in Automotive Industry
A large German/American producer of auto parts uses high-pressure pumps to deburr machined parts as a part of its production and quality check process. They decided to monitor these pumps to make sure they work properly and that they can see any indications leading to a potential failure before it affects their process.