Customer Company Size
Large Corporate
Region
- Asia
Country
- India
Product
- Our Impacts GHG accounting platform
Tech Stack
- GHG accounting platform
Implementation Scale
- Enterprise-wide Deployment
Impact Metrics
- Environmental Impact Reduction
- Brand Awareness
Technology Category
- Analytics & Modeling - Real Time Analytics
Applicable Functions
- Discrete Manufacturing
Use Cases
- Energy Management System
- Regulatory Compliance Monitoring
Services
- Data Science Services
About The Customer
Pratibha Syntex Ltd is one of the world’s largest full vertically integrated suppliers of all types of knitted textile products. The company works with around 30,000 farmers, hires 8,000 employees and supplies renowned global apparel brands from over 20 countries, including Nike, Walmart, Hanes, Lee, Ralph Lauren, Zara, Kathmandu and Woolworths. Pratibha Syntex has won accolades domestically and internationally, produces around 60 million garments every year and has a strong ambition to be seen as a leader in driving societal and environmental responsibility.
The Challenge
Pratibha Syntex Ltd, one of the world’s largest full vertically integrated suppliers of all types of knitted textile products, faced the challenge of implementing a system that formally accounts and measures the tCO2 e emitted by the company annually. The company wanted to improve the quality of its reporting to key stakeholders and enhance its business functions. The company works with around 30,000 farmers, hires 8,000 employees and supplies renowned global apparel brands from over 20 countries. It produces around 60 million garments every year and has a strong ambition to be seen as a leader in driving societal and environmental responsibility.
The Solution
Cool Earth & Ecometrica customised Our Impacts for Pratibha’s carbon accounting strategy, both at the factory level for three units in Pithampur and most importantly and uniquely, the first ever measurement of a carbon footprint at the farm level. Cool Earth worked extensively with both the farm team and the faculty management team at the factory level. Emission factors unique to India were used to ensure that calculation was accurate and complete in scope.
Operational Impact
Case Study missing?
Start adding your own!
Register with your work email and create a new case study profile for your business.
Related Case Studies.
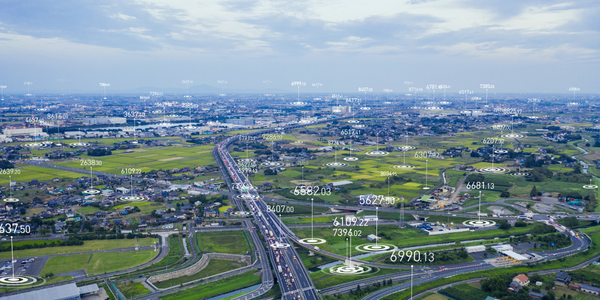
Case Study
Remote Monitoring for Environmental Compliance
Emerson wanted to provide a connected environmental analyzer to their customers. They wanted to leverage IoT technologies to provide a software solution that was easy to use, real-time and centralized. Compliance with pollution control board guidelines and the ability to remotely calibrate and troubleshoot these devices was the primary objective. Requirements - Centralized Remote Monitoring. - IoT Based Smart Environmental Analyzers. - Remote Calibration and Troubleshooting. - User Friendly Application. - Reporting & Dashboards. - Compliance with pollution control board guidelines.
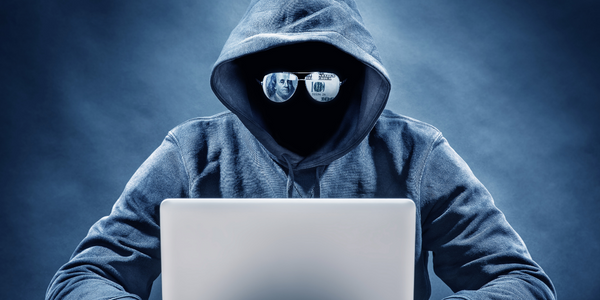
Case Study
Driving Network Efficiency and Fraud Detection Efforts
Baltimore Gas and Electric Company (BGE) wanted to optimize the deployment and ongoing health of its advanced metering infrastructure (AMI) network and identify and reduce unbilled energy usage. BGE wanted a solution to deliver an annual economic benefit of $20 million.
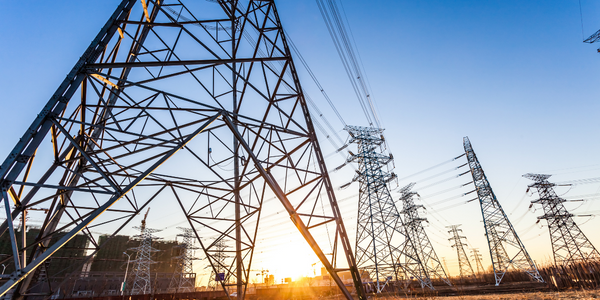
Case Study
IoT based Energy Quality Availability Monitoring Solution
There were several challenges faced:Since this data would be in the public domain, accuracy and authenticity of this data were of paramount importance. It should be able to withstand scrutiny.It is challenging to build an appliance that can withstand a wide range of voltage fluctuations from as low at 90v to as high as 320v. Since the device would be installed in remote locations, its resilience was of paramount importance.The device would have to deal with poor network coverage and have the ability to store and re-transmit data if networks were not available, which is often the case in rural India. The device could store up to 30 days of data.The platform that deals with the data should be readily available and highly reliable and never lose a packet of data.
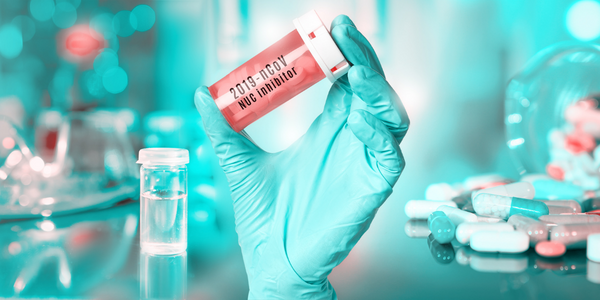
Case Study
ELI LILLY ADOPTS MICROMEDIA’S ALERT NOTIFICATION SYSTEM
Pharmaceutical production is subject to a strict set of enforced rules that must be adhered to and compliance to these standards is critically necessary. Due to the efforts of WIN 911’s strategic partner Micromedia, Lilly was able to adopt an alarm notification infrastructure that integrated smoothly with their existing workflows and emergency hardware and protocols. These raw energy sources enable the industrial process to function: electricity, WIN-911 Software | 4020 South Industrial Drive, Suite 120 | Austin, TX 78744 USA industrial steam, iced water, air mixtures of varying quality. Refrigeration towers, boilers and wastewater are monitored by ALERT. Eli Lilly identified 15000 potential variables, but limitations compelled them to chisel the variable list down to 300. This allowed all major alarms to be covered including pressure, discharge, quantity of waste water discharged,temperature, carbon dioxide content, oxygen & sulphur content, and the water’s pH.
-Systems.png)
Case Study
Product Development for Power Line Communication (PLC/BPL) Systems
The client wanted to develop a product that can acquire data from their meter units installed at the consumer's premises. A system capable of acquiring, transferring and archiving the data had to be in place, replacing the existing traditional method which was error prone and expensive to operate. The system needed to be integrated with the existing Customer Relationship Management (CRM) system for increasing the operational efficiency.