Technology Category
- Infrastructure as a Service (IaaS) - Cloud Databases
- Networks & Connectivity - Ethernet
Applicable Industries
- Cement
- Plastics
Applicable Functions
- Maintenance
- Product Research & Development
Use Cases
- Construction Management
- Time Sensitive Networking
Services
- System Integration
About The Customer
Precision Valley Communications (PVC) is a premier supplier of communications network mapping and engineering to the broadband industry. With over 25 years in the business and 400 years of combined field mapping experience, PVC has established itself as a trusted partner for major cable companies. The company is known for its expertise in surveying and redesigning hybrid fiber-coaxial (HFC) networks, a task that involves complex and detailed work such as physically surveying miles of conduit, manholes, and multiple dwelling units. PVC's clients include major cable companies in the United States, and their projects often involve high-profile and high-security sites such as embassies and congressional staff offices.
The Challenge
Precision Valley Communications (PVC), a leading provider of communications network mapping and engineering to the broadband industry, was tasked with a major project to survey and redesign a hybrid fiber-coaxial (HFC) network for a major cable company in Washington, D.C. The project involved a field survey of the company’s network, including 586 miles of conduit, 2,400 manholes, and over 200,000 multiple-dwelling units. The goal was to complete a major network redesign to move all equipment from manholes to breakout pedestals to reduce rented duct space and increase accessibility for field crews. However, five months into the project, only 21 percent of the 586 miles of survey was completed, putting the USD 145 million project way behind schedule. The delays were not due to a lack of skill or effort, but rather the inefficient software tool that was initially mandated for use in the project. The software resulted in significant workflow impediments and time-consuming database transactions, severely hampering productivity.
The Solution
Recognizing the need for more efficient software tools, PVC decided to switch to Bentley’s HFC network engineering solution, specifically Bentley Coax and Bentley Fiber. These tools provided a unique, seamless CAD and open GIS environment that allowed drafters to efficiently design and manage network infrastructure. The Bentley HFC solution was built for optimized integration with Oracle Spatial, enabling all network properties and geometries to be managed in Oracle Spatial through an optimized process that minimized time-consuming database transactions. This allowed for rapid layout, verification, and posting of network designs. The solution also leveraged the MicroStation platform to supply the drafting productivity tools and engineering precision for fast layouts, and it could be used to produce high-quality construction prints directly from the design environment. With the Bentley HFC solution, PVC was able to achieve the productivity and efficiencies needed to complete the project on schedule.
Operational Impact
Quantitative Benefit
Case Study missing?
Start adding your own!
Register with your work email and create a new case study profile for your business.
Related Case Studies.
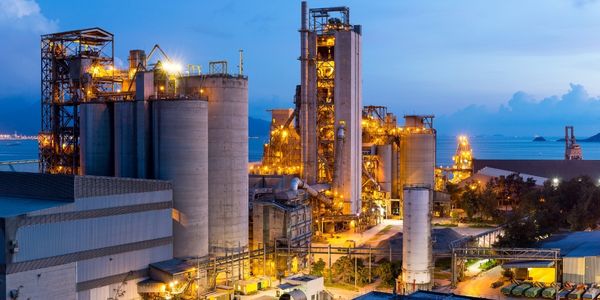
Case Study
System 800xA at Indian Cement Plants
Chettinad Cement recognized that further efficiencies could be achieved in its cement manufacturing process. It looked to investing in comprehensive operational and control technologies to manage and derive productivity and energy efficiency gains from the assets on Line 2, their second plant in India.
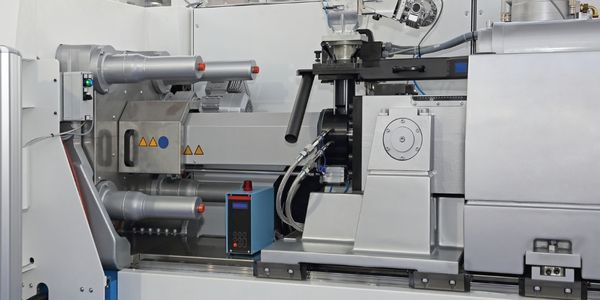
Case Study
Plastic Spoons Case study: Injection Moulding
In order to meet customer expectations by supplying a wide variety of packaging units, from 36 to 1000 spoons per package, a new production and packaging line needed to be built. DeSter wanted to achieve higher production capacity, lower cycle time and a high degree of operator friendliness with this new production line.
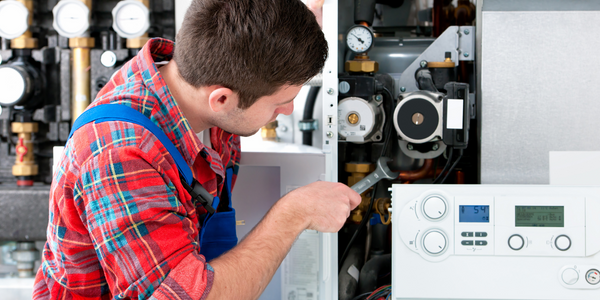
Case Study
Boiler Control System for Plastic Manufacturing Applications
Factory automation applications must be equipped to handle and monitor the myriads of information from attached devices. For plastic manufacturing applications, the boiler control system plays a critical role by gathering and regulating information to ensure production is accurate and smooth. In this particular case, the customer combines eight subsystems that include power meters, water meters, alarm output, displays, and I/O status to be controlled by several intelligent controllers with Modbus RTU interface. The Modbus TCP protocol is used for this application due to the distance. System Requirements: • Modbus serial to Modbus TCP translation • Multiple slaves/masters support • Automatic Modbus TCP response time detection
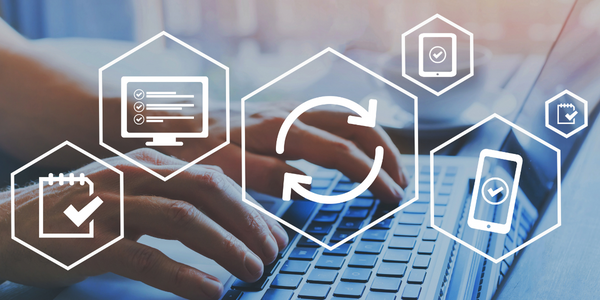
Case Study
Ascend Performance Materials Case Study
Ascend operations must access multiple software systems to manage day-to-day operations in an effective and secure manner. These systems generate large sets of data which contain critical information pertaining to management systems, planning and cost information in business systems and energy consumption. As a result, Ascend management was challenged with creating relevant reports reflecting performance measures in overall context of their operational process. The company’s previous process entailed collecting and analyzing data manually which was not effective, since the information collected was generated after the fact, and was too complex for collaborative use across the organization.
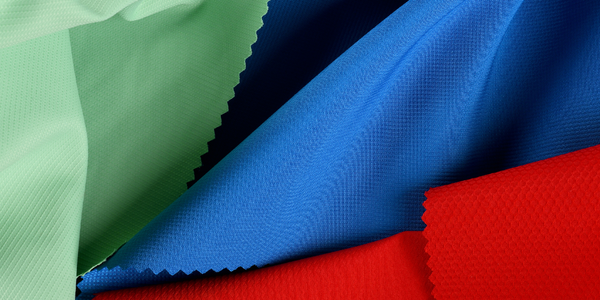
Case Study
Remake Enterprise-to-production System
The client was running a legacy material flow tracking system and wanted to replace the system with a more effective one as the system was increasingly expensive to maintain and support and also was not extendable. The client's IT landscape was filled with modern applications and it was difficult to interface the material flow tracking system with modern applications.
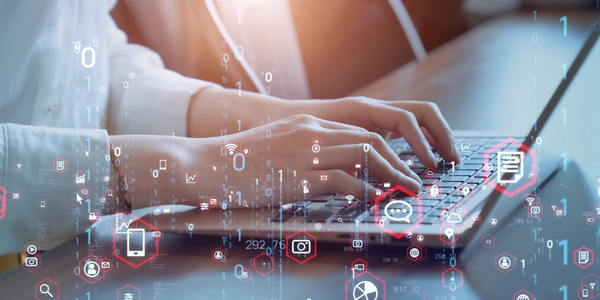
Case Study
Digital Transformation of Atlanta Grout & Tile: An IoT Case Study
Atlanta Grout & Tile, a Tile, Stone & Grout restoration company based in Woodstock, Georgia, was facing challenges with its traditional business model. Despite steady growth over the years, the company was falling behind the web revolution and missing out on the opportunity to tap into a new consumer base. They were using independent software from different vendors for each of their department information and workforce management. This resulted in a lot of manual work on excel and the need to export/import data between different systems. This not only increased overhead costs but also slowed down their response to clients. The company also had to prepare numerous reports manually and lacked access to customer trends for effective business decision-making.