Customer Company Size
SME
Region
- America
Country
- United States
Product
- E2 Pro
- E2 Shop System
Tech Stack
- SaaS
Implementation Scale
- Enterprise-wide Deployment
Impact Metrics
- Productivity Improvements
- Cost Savings
Technology Category
- Platform as a Service (PaaS) - Application Development Platforms
Applicable Industries
- Aerospace
- Automotive
- Oil & Gas
Applicable Functions
- Discrete Manufacturing
- Quality Assurance
Use Cases
- Manufacturing System Automation
- Predictive Maintenance
Services
- Software Design & Engineering Services
- System Integration
About The Customer
Prototype Casting is a manufacturing company that was founded in 1995 by Mike Kaiser. They specialize in manufacturing metal components as prototypes and low-volume production. The company also offers metal and aluminum casting services at their full-service machine shop in Denver, CO. Prototype Casting serves a wide range of industries including automotive, aerospace, defense, medical, robotics, and oil and gas. In 2008, the ownership of the company changed when Chad TeBeest bought the company after working in the shop for seven years.
The Challenge
Prototype Casting was struggling with their previous ERP system, JobBoss, which wasn't providing a comprehensive view of their operations. They were unable to efficiently track time spent on jobs or their employees' time. Additionally, they couldn't see the profit from the jobs they did every day. Without visibility into job costs and profits, it was hard for Prototype Casting to measure their performance. They needed a solution that could provide a full picture of their shop, track time efficiently, and provide clear visibility into job costs and profits.
The Solution
Prototype Casting decided to switch to the E2 Pro in 2012 and later upgraded to the E2 Shop System, Shoptech’s SaaS software, in 2016. The decision to choose E2 was based on the price and how the capabilities fit their company’s needs so well. The transition from E2 Pro to E2 Shop was smooth and they only dealt with a few basic questions regarding the upgrade. They currently use both the Quality and Scheduling Modules in the E2 Shop system. The Quality Module ensures that they save time, no steps are missed on jobs, and everything in the production process is done correctly.
Operational Impact
Case Study missing?
Start adding your own!
Register with your work email and create a new case study profile for your business.
Related Case Studies.
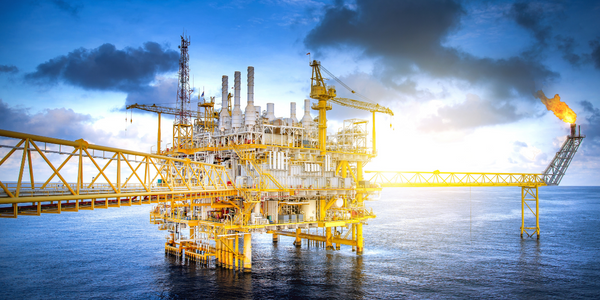
Case Study
Taking Oil and Gas Exploration to the Next Level
DownUnder GeoSolutions (DUG) wanted to increase computing performance by 5 to 10 times to improve seismic processing. The solution must build on current architecture software investments without sacrificing existing software and scale computing without scaling IT infrastructure costs.
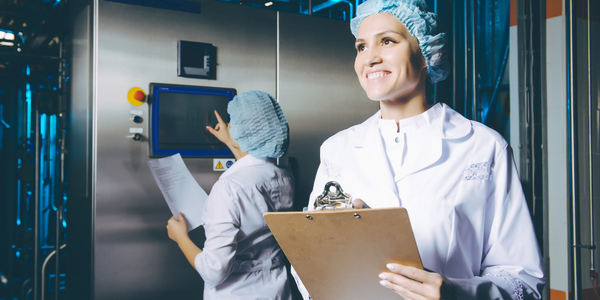
Case Study
Remote Wellhead Monitoring
Each wellhead was equipped with various sensors and meters that needed to be monitored and controlled from a central HMI, often miles away from the assets in the field. Redundant solar and wind generators were installed at each wellhead to support the electrical needs of the pumpstations, temperature meters, cameras, and cellular modules. In addition to asset management and remote control capabilities, data logging for remote surveillance and alarm notifications was a key demand from the customer. Terra Ferma’s solution needed to be power efficient, reliable, and capable of supporting high-bandwidth data-feeds. They needed a multi-link cellular connection to a central server that sustained reliable and redundant monitoring and control of flow meters, temperature sensors, power supply, and event-logging; including video and image files. This open-standard network needed to interface with the existing SCADA and proprietary network management software.
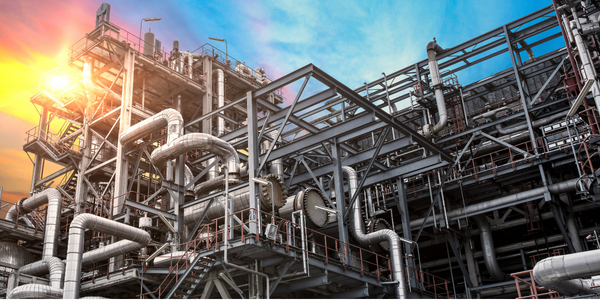
Case Study
Refinery Saves Over $700,000 with Smart Wireless
One of the largest petroleum refineries in the world is equipped to refine various types of crude oil and manufacture various grades of fuel from motor gasoline to Aviation Turbine Fuel. Due to wear and tear, eight hydrogen valves in each refinery were leaking, and each cost $1800 per ton of hydrogen vented. The plant also had leakage on nearly 30 flare control hydrocarbon valves. The refinery wanted a continuous, online monitoring system that could catch leaks early, minimize hydrogen and hydrocarbon production losses, and improve safety for maintenance.
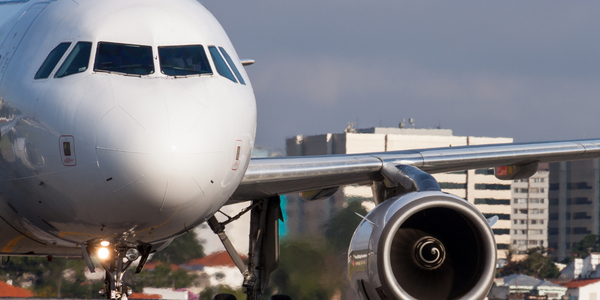
Case Study
Airbus Soars with Wearable Technology
Building an Airbus aircraft involves complex manufacturing processes consisting of thousands of moving parts. Speed and accuracy are critical to business and competitive advantage. Improvements in both would have high impact on Airbus’ bottom line. Airbus wanted to help operators reduce the complexity of assembling cabin seats and decrease the time required to complete this task.
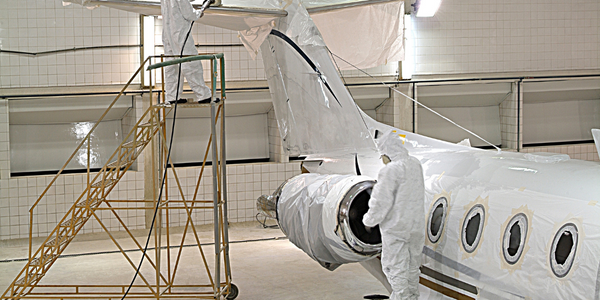
Case Study
Aircraft Predictive Maintenance and Workflow Optimization
First, aircraft manufacturer have trouble monitoring the health of aircraft systems with health prognostics and deliver predictive maintenance insights. Second, aircraft manufacturer wants a solution that can provide an in-context advisory and align job assignments to match technician experience and expertise.