Röchling Automotive Enhances Production with Stratus Avance High-Availability Software
Customer Company Size
Large Corporate
Region
- Europe
Country
- Germany
Product
- Stratus Avance® high-availability software
- SAP® application software
- Oracle® database
Tech Stack
- Virtualization
- High-availability systems
- x86 servers
Implementation Scale
- Enterprise-wide Deployment
Impact Metrics
- Cost Savings
- Productivity Improvements
Technology Category
- Application Infrastructure & Middleware - Data Exchange & Integration
- Platform as a Service (PaaS) - Device Management Platforms
Applicable Industries
- Automotive
Applicable Functions
- Process Manufacturing
- Quality Assurance
Use Cases
- Predictive Maintenance
- Process Control & Optimization
Services
- Software Design & Engineering Services
- System Integration
About The Customer
Röchling Automotive is a leading supplier in the automotive industry, specializing in the production of door panels for major car manufacturers like Volkswagen (VW). The company operates a high-demand production facility in Wolfsburg, Germany, where it produces door panels for approximately 2,000 vehicles daily. Röchling's operations are characterized by a just-in-time and just-in-sequence production model, requiring precise timing and coordination to meet the assembly line demands of the adjacent VW plant. The company is committed to maintaining high standards of quality and efficiency, leveraging advanced IT systems to manage its complex production processes. Röchling Automotive's reputation and success depend on its ability to deliver components accurately and on time, making IT system reliability a critical aspect of its operations.
The Challenge
Röchling Automotive faced a critical challenge in maintaining uninterrupted IT processes for production control. The company needed to ensure continuous data flow across all production areas, from receiving orders via EDI to sending confirmation messages to the SAP system. The production of door panels for VW vehicles required precise timing and sequencing, with no room for delays or errors. Any interruption in IT availability could lead to significant operational disruptions, contractual penalties, and damage to the company's reputation. The existing backup system was inadequate, as it took too long to become functional, leading to data loss and time-consuming manual reconciliation. The company needed a robust solution to eliminate downtime and ensure high availability of its IT systems.
The Solution
In response to its IT challenges, Röchling Automotive implemented Stratus Avance, a high-availability solution designed for virtualization. The solution was deployed on two high-performance Hewlett-Packard server workstations, ensuring continuous synchronization and protection against downtime. The Avance software dynamically synchronizes the servers, allowing seamless failover in case of hardware faults or system failures. This setup ensures that both servers are always up-to-date, minimizing the time required for database reconciliation. The implementation was supported by MTS, which provided comprehensive project support, including migration of legacy systems and failover testing. The solution's simplicity and remote management capabilities have significantly improved system administration, allowing for efficient maintenance and fault management. Röchling Automotive now benefits from a robust IT infrastructure that guarantees high availability and operational continuity.
Operational Impact
Quantitative Benefit
Case Study missing?
Start adding your own!
Register with your work email and create a new case study profile for your business.
Related Case Studies.
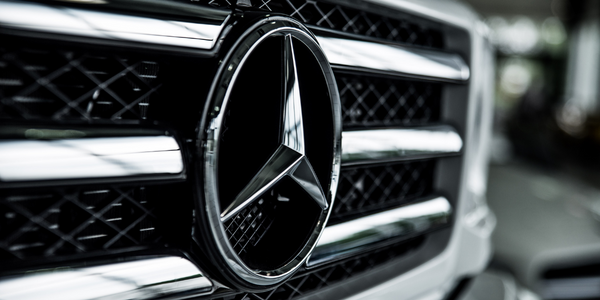
Case Study
Integral Plant Maintenance
Mercedes-Benz and his partner GAZ chose Siemens to be its maintenance partner at a new engine plant in Yaroslavl, Russia. The new plant offers a capacity to manufacture diesel engines for the Russian market, for locally produced Sprinter Classic. In addition to engines for the local market, the Yaroslavl plant will also produce spare parts. Mercedes-Benz Russia and his partner needed a service partner in order to ensure the operation of these lines in a maintenance partnership arrangement. The challenges included coordinating the entire maintenance management operation, in particular inspections, corrective and predictive maintenance activities, and the optimizing spare parts management. Siemens developed a customized maintenance solution that includes all electronic and mechanical maintenance activities (Integral Plant Maintenance).
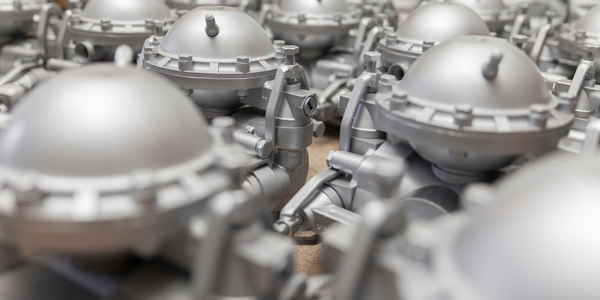
Case Study
Monitoring of Pressure Pumps in Automotive Industry
A large German/American producer of auto parts uses high-pressure pumps to deburr machined parts as a part of its production and quality check process. They decided to monitor these pumps to make sure they work properly and that they can see any indications leading to a potential failure before it affects their process.