Customer Company Size
Mid-size Company
Region
- America
Country
- United States
Product
- Plex Manufacturing Cloud
Tech Stack
- Cloud ERP
Implementation Scale
- Enterprise-wide Deployment
Impact Metrics
- Customer Satisfaction
- Digital Expertise
- Productivity Improvements
Technology Category
- Functional Applications - Enterprise Resource Planning Systems (ERP)
- Infrastructure as a Service (IaaS) - Cloud Computing
Applicable Industries
- Automotive
Applicable Functions
- Discrete Manufacturing
- Quality Assurance
Use Cases
- Factory Operations Visibility & Intelligence
- Manufacturing System Automation
- Predictive Maintenance
Services
- Cloud Planning, Design & Implementation Services
- System Integration
About The Customer
Ralco Industries, Inc., based in Auburn Hills, is a tier 2 automotive supplier that has been operating since 1970. The company specializes in the design, prototyping, production, and distribution of high-tolerance metal stampings and welded assemblies. Ralco is known for setting a high standard of product and process quality in the industry, achieving a defect rate of less than one part-per-million for eight consecutive years. This achievement is a testament to the company's commitment to continuous innovation and improvement in its operations. Ralco's management has prioritized fostering a culture of quality, providing personnel with the resources needed to drive improvements. Over the years, the company has invested significant time and capital in maturing its process capabilities and adopting next-generation ERP solutions to enhance its operations.
The Challenge
Ralco Industries, a tier 2 automotive supplier, has been committed to maintaining a high standard of quality in its products and processes since its inception. The company has achieved a defect rate of less than one part-per-million for eight consecutive years, which requires continuous innovation and improvement in people, processes, and technology. As the company matured its process capabilities, it recognized the need for a next-generation ERP solution to support its quality-centric culture. The challenge was to find a solution that would enable operators and leaders to take responsibility for the quality and success of processes, allowing them to make necessary improvements. In 2001, Ralco chose the Plex Manufacturing Cloud as its ERP solution, recognizing the potential of cloud technology to stay ahead of the competition.
The Solution
Ralco Industries implemented the Plex Manufacturing Cloud as its ERP solution in 2001, taking a progressive approach to its ERP implementation. The company recognized the potential of cloud technology to stay ahead of the competition and chose Plex Systems for its comprehensive and integrated platform. The solution supports nearly all aspects of Ralco's operations, from sales to purchasing, inventory, production, HR, training, reporting, and customer complaints. Ralco has also been working towards developing a 'smart' manufacturing environment by integrating its equipment and machinery with the Plex Systems solution. The integrated platform provides superior control over operations, ensuring operators meet training requirements, enabling serialized traceability, and offering minute-by-minute performance indicators. The system's holistic nature allows for remote interaction with equipment and streamlines alerts for corrective actions, fostering a proactive approach to quality and continuous improvement.
Operational Impact
Quantitative Benefit
Case Study missing?
Start adding your own!
Register with your work email and create a new case study profile for your business.
Related Case Studies.
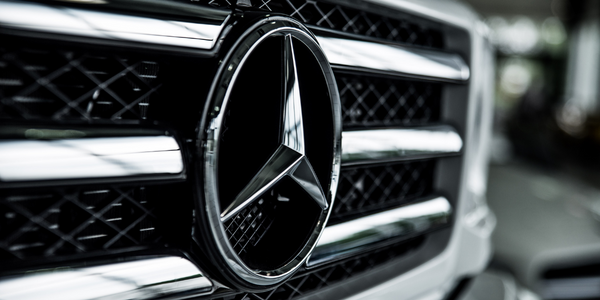
Case Study
Integral Plant Maintenance
Mercedes-Benz and his partner GAZ chose Siemens to be its maintenance partner at a new engine plant in Yaroslavl, Russia. The new plant offers a capacity to manufacture diesel engines for the Russian market, for locally produced Sprinter Classic. In addition to engines for the local market, the Yaroslavl plant will also produce spare parts. Mercedes-Benz Russia and his partner needed a service partner in order to ensure the operation of these lines in a maintenance partnership arrangement. The challenges included coordinating the entire maintenance management operation, in particular inspections, corrective and predictive maintenance activities, and the optimizing spare parts management. Siemens developed a customized maintenance solution that includes all electronic and mechanical maintenance activities (Integral Plant Maintenance).
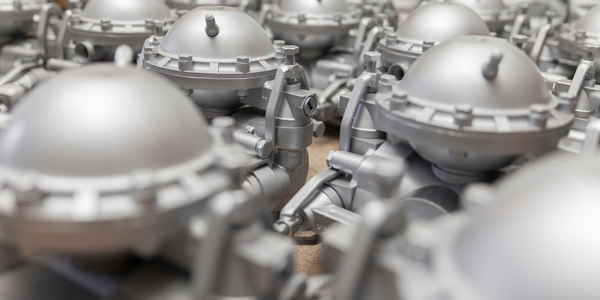
Case Study
Monitoring of Pressure Pumps in Automotive Industry
A large German/American producer of auto parts uses high-pressure pumps to deburr machined parts as a part of its production and quality check process. They decided to monitor these pumps to make sure they work properly and that they can see any indications leading to a potential failure before it affects their process.