Customer Company Size
Large Corporate
Region
- Europe
Country
- France
Product
- Blue Yonder’s Luminate™ Planning suite
Tech Stack
- Inventory Management Software
- Supply Chain Management Software
Implementation Scale
- Enterprise-wide Deployment
Impact Metrics
- Cost Savings
- Productivity Improvements
Technology Category
- Functional Applications - Inventory Management Systems
- Functional Applications - Enterprise Resource Planning Systems (ERP)
Applicable Industries
- Automotive
Applicable Functions
- Logistics & Transportation
- Procurement
Use Cases
- Supply Chain Visibility
- Inventory Management
Services
- Software Design & Engineering Services
- System Integration
About The Customer
Renault is a European automotive company that has built a reputation for quality, innovation, and service. A critical part of this equation is the automaker’s spare parts business. They pledge to deliver any one of 200,000 spare parts overnight through a multi-echelon distribution network. Renault’s spare parts operations are supported by two master warehouses and a network of dozens of distribution centers scattered across Europe. The company has a complex European distribution network, which includes up to five tiers of suppliers, dealers and regional distribution centers. Renault is focused on innovation and was looking for a major breakthrough in their spare parts logistics.
The Challenge
Renault, a European automotive company, has built a reputation for quality, innovation, and service. A critical part of this equation is the automaker’s spare parts business. They pledge to deliver any one of 200,000 spare parts overnight through a multi-echelon distribution network. Renault maintained multiple layers of redundant safety stock in order to meet its overnight delivery promise even though its own supplier lead times range from two to eight weeks. Renault wanted to reduce inventory levels to free up cashflow without degrading its spare parts delivery commitment. Renault’s spare parts operations are supported by two master warehouses and a network of dozens of distribution centers scattered across Europe. Historically, Renault was able to honor its customer overnight delivery commitment by maintaining high spare parts inventory levels across its complex European distribution network, which includes up to five tiers of suppliers, dealers and regional distribution centers. This required stocking large amounts of redundant safety stock since supplier lead times vary from two to eight weeks. This was costly.
The Solution
When Renault decided to free up cashflow by reducing inventory levels, without impacting their overnight delivery promise, they looked for technology help. They found it in Blue Yonder’s Luminate™ Planning suite. The Blue Yonder solutions have allowed Renault to achieve a centralized calculation of inventory drivers, replenishments and forecasts while also being able to understand the local nuances of its distribution centers. Renault has been able to maintain its same levels of product availability while dramatically reducing its redundant safety stocks. Renault’s focus on innovation was also an important consideration. “Blue Yonder has a product that is very famous in retail. We wanted to bring the best ideas in retail to our spare parts logistics. We were looking for a major breakthrough, and we wanted to make it happen quickly.”
Operational Impact
Quantitative Benefit
Case Study missing?
Start adding your own!
Register with your work email and create a new case study profile for your business.
Related Case Studies.
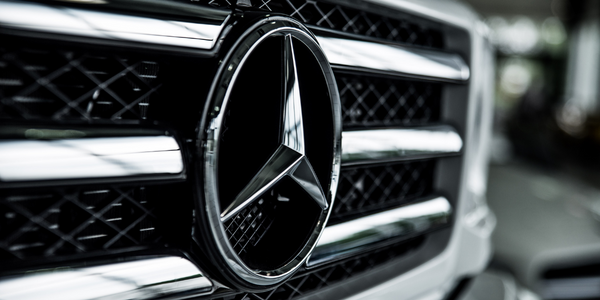
Case Study
Integral Plant Maintenance
Mercedes-Benz and his partner GAZ chose Siemens to be its maintenance partner at a new engine plant in Yaroslavl, Russia. The new plant offers a capacity to manufacture diesel engines for the Russian market, for locally produced Sprinter Classic. In addition to engines for the local market, the Yaroslavl plant will also produce spare parts. Mercedes-Benz Russia and his partner needed a service partner in order to ensure the operation of these lines in a maintenance partnership arrangement. The challenges included coordinating the entire maintenance management operation, in particular inspections, corrective and predictive maintenance activities, and the optimizing spare parts management. Siemens developed a customized maintenance solution that includes all electronic and mechanical maintenance activities (Integral Plant Maintenance).
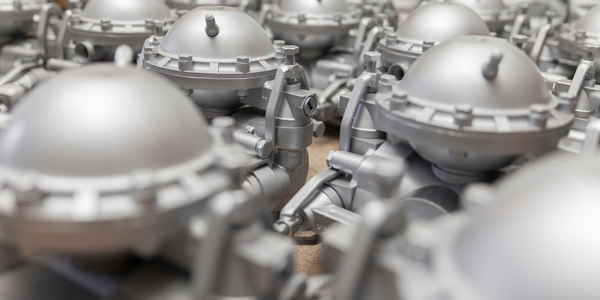
Case Study
Monitoring of Pressure Pumps in Automotive Industry
A large German/American producer of auto parts uses high-pressure pumps to deburr machined parts as a part of its production and quality check process. They decided to monitor these pumps to make sure they work properly and that they can see any indications leading to a potential failure before it affects their process.