Technology Category
- Infrastructure as a Service (IaaS) - Cloud Databases
- Processors & Edge Intelligence - Microcontrollers & Printed Circuit Boards
Applicable Industries
- Agriculture
- Electronics
Applicable Functions
- Product Research & Development
Use Cases
- Agriculture Disease & Pest Management
- Time Sensitive Networking
Services
- Hardware Design & Engineering Services
About The Customer
Leica Geosystems is a company that specializes in precision farming applications. Their motto is 'when it has to be right,' reflecting their commitment to delivering high-quality, precise solutions. One of their products is the Leica mojoRTK, an auto-steer guidance system designed to enhance precision in farming operations. The company is known for its innovative approach to product development and its commitment to leveraging the latest technology to improve its offerings. Despite facing challenges in the development process, Leica Geosystems is committed to delivering products that meet their high standards and the needs of their customers in the agriculture industry.
The Challenge
Leica Geosystems, a company known for its precision farming applications, faced a significant challenge during the development of the Leica mojoRTK, an auto-steer guidance system. The company had outsourced one of its boards to a contractor, a decision that soon proved to be a mistake. The board was returned behind schedule and failed to meet any of its design and manufacturing requirements. This left Leica Geosystems with a defunct PCB and a looming product launch. The company was faced with a critical decision: risk going back to the contractor, or overhaul the design and complete it in-house. The latter option was not going to be easy as the engineers needed to recapture the board design, translate files, and carefully recreate the PCB.
The Solution
Scott Gemmell, Engineering Manager at Leica Geosystems Agriculture, decided to complete the design in-house. The team had recently upgraded to Altium Designer and decided to leverage its latest features. The most significant change was the introduction of integrated database libraries, which allowed the team to link directly to inventory and components stored in their external databases. This feature enabled engineers to choose and place components from various databases, while creating a library specific to the project. They could also easily update and manage these databases from within their own design space. The integrated libraries also helped the team to source and cost components, reducing product turn-around time. The MCAD-ECAD collaboration technology in Altium Designer allowed the team to reduce revisions and work more closely with its industrial design team. The 3D visualization engine in Altium Designer helped build confidence around the design of the Leica mojoRTK.
Operational Impact
Case Study missing?
Start adding your own!
Register with your work email and create a new case study profile for your business.
Related Case Studies.
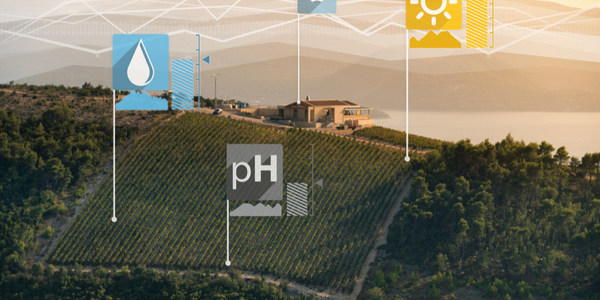
Case Study
Intelligent Farming with ThingWorx Analytics
Z Farms was facing three challenges: costly irrigation systems with water as a limited resource, narrow optimal ranges of soil moisture for growth with difficult maintenance and farm operators could not simply turn on irrigation systems like a faucet.
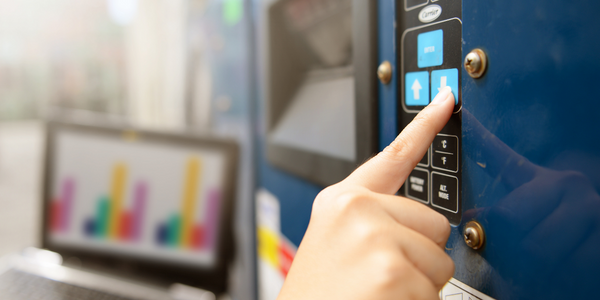
Case Study
Remote Temperature Monitoring of Perishable Goods Saves Money
RMONI was facing temperature monitoring challenges in a cold chain business. A cold chain must be established and maintained to ensure goods have been properly refrigerated during every step of the process, making temperature monitoring a critical business function. Manual registration practice can be very costly, labor intensive and prone to mistakes.
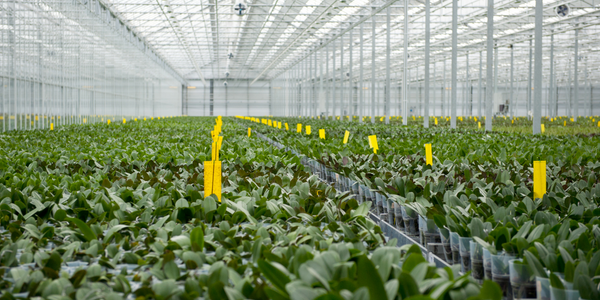
Case Study
Greenhouse Intelligent Monitoring and Control Solution
Farming Orchids is the most successful form of precision farming in Taiwan, and also the most exported flower. Orchids need a specific temperature and humidity conditions to grow and bloom, and its flowering time may not be in line with market demands, so the price collapses when there is overproduction. Therefore, some farmers began to import automated greenhouse control systems for breeding and forcing, which not only improves quality, but also effectively controls the production period and yield to ensure revenue. In 2012, an orchid farmer built a Forcing Greenhouse of about 200 pings (approximately 661 Square Meters) in Tainan, Taiwan. The system integrator adopted Advantech’s APAX-5000 series programmable automation controllers to build the control platform, coupled with Advantech WebAccess HMI/SCADA software, to achieve cloud monitoring. The staff of the orchid field can monitor important data anytime via smart phone, iPad, and other handheld devices, and control the growth and flowering conditions. System requirements: In the past, most environmental control systems of orchid greenhouses in Taiwan used PLCs (Programmable Logic Controller) with poorscalability and control, and could not be connected to the Internet formonitoring from the cloud. For advanced database analysis and networking capability, the PC platform must be adopted. Therefore, PAC Systems (Programmable Automation Controller) with both PLC programming capabilities andPC functions is a better choice.The environmental control of the Orchid greenhouse switches on and off devices like fan, shade net, cooling/heat pump, liquid flow control, water-cooling wall etc. It is controlled by a control panel of electric controllers, and is driven by a motor, to adjust the greenhouse temperature, humidity, and other environmental conditions to the set parameters.