Technology Category
- Functional Applications - Inventory Management Systems
- Sensors - Voltage Sensors
Applicable Industries
- Automotive
- Buildings
Applicable Functions
- Procurement
- Warehouse & Inventory Management
Use Cases
- Inventory Management
- Time Sensitive Networking
About The Customer
The customer is an online retailer that sells office equipment products to medium and small-sized business offices. They provide next-day delivery services, ensuring that their customers receive their orders promptly. The company imports and delivers products directly to local distribution centers (DCs), from where the products are then delivered to the customers. They were facing challenges with inventory management and delivery services, with each DC at risk of having excess inventory or running out of stock. To mitigate these risks, the company was in the process of building a replenishment center to streamline their delivery process.
The Challenge
The customer, an online retailer of office equipment, was facing challenges with their inventory management and delivery services. They were importing and delivering products directly to local distribution centers (DCs), which put each DC at risk of having excess inventory or running out of stock. The company was trying to mitigate these risks by building a replenishment center and delivering products from this center to each DC. However, the accuracy of their received sales plan was low and relied heavily on lagging indicators. Additionally, truck loading planning was done manually, a time-consuming process that often resulted in miscalculations of the required number of trucks. Lastly, the management of the minimum order quantity and complicated ordering conditions, considering the container’s capacity, were managed in Excel, which was not efficient.
The Solution
The company adopted o9, a single integrated, cloud-native platform, to improve their operations. With o9, they were able to improve the accuracy of their sales plan by creating a forecast using “Prophet”, a tool developed by Facebook. This platform also automated the truck loading planning process, estimating the number of trucks needed by considering the loading rate of trucks and the number of pallets. Furthermore, o9 reduced the grunt work by automatically creating order requests considering various ordering conditions, enabling the issuing of an accurate order request. The o9 Enterprise Knowledge Graph was used to build market, demand, and supply-knowledge models, allowing for running all key planning processes for all products and DCs, across all time horizons in a single integrated platform. o9 leveraged its open architecture to incorporate proprietary developed forecasting algorithms, safety stock logic, and truck loading logic in R and Python.
Operational Impact
Quantitative Benefit
Case Study missing?
Start adding your own!
Register with your work email and create a new case study profile for your business.
Related Case Studies.
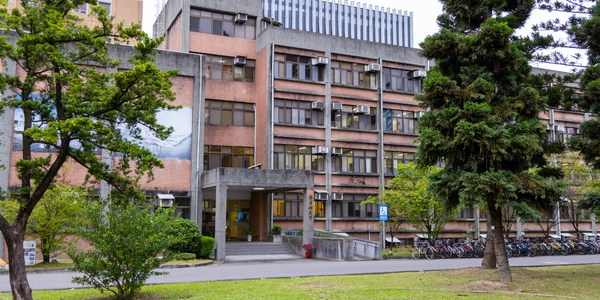
Case Study
Energy Saving & Power Monitoring System
Recently a university in Taiwan was experiencing dramatic power usage increases due to its growing number of campus buildings and students. Aiming to analyze their power consumption and increase their power efficiency across 52 buildings, the university wanted to build a power management system utilizing web-based hardware and software. With these goals in mind, they contacted Advantech to help them develop their system and provide them with the means to save energy in the years to come.
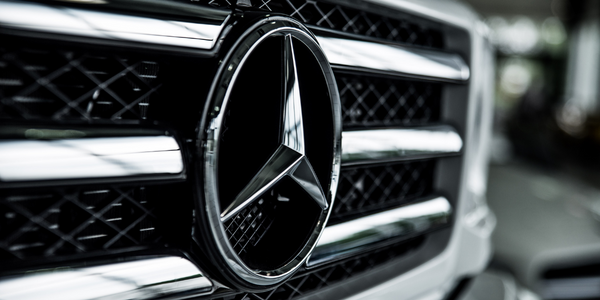
Case Study
Integral Plant Maintenance
Mercedes-Benz and his partner GAZ chose Siemens to be its maintenance partner at a new engine plant in Yaroslavl, Russia. The new plant offers a capacity to manufacture diesel engines for the Russian market, for locally produced Sprinter Classic. In addition to engines for the local market, the Yaroslavl plant will also produce spare parts. Mercedes-Benz Russia and his partner needed a service partner in order to ensure the operation of these lines in a maintenance partnership arrangement. The challenges included coordinating the entire maintenance management operation, in particular inspections, corrective and predictive maintenance activities, and the optimizing spare parts management. Siemens developed a customized maintenance solution that includes all electronic and mechanical maintenance activities (Integral Plant Maintenance).
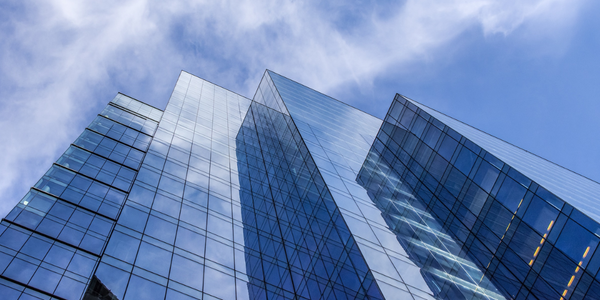
Case Study
Intelligent Building Automation System and Energy Saving Solution
One of the most difficult problems facing the world is conserving energy in buildings. However, it is not easy to have a cost-effective solution to reduce energy usage in a building. One solution for saving energy is to implement an intelligent building automation system (BAS) which can be controlled according to its schedule. In Indonesia a large university with a five floor building and 22 classrooms wanted to save the amount of energy being used.