Technology Category
- Functional Applications - Inventory Management Systems
- Functional Applications - Warehouse Management Systems (WMS)
Applicable Industries
- Electronics
- Marine & Shipping
Applicable Functions
- Logistics & Transportation
- Warehouse & Inventory Management
Use Cases
- Inventory Management
- Picking, Sorting & Positioning
About The Customer
The customer is a specialist marine electronics company that provides navigation, marine instruments, and fish finding equipment to both the recreational and commercial marine sectors. The company was struggling with siloed processes, lack of end-to-end visibility, and inefficient inventory management. They were unable to respond effectively to changing market dynamics and frequently experienced both inventory excess and shortages. The company's demand forecasting, especially for new product introductions, was also inaccurate.
The Challenge
The marine electronics company, a specialist in providing navigation, marine instruments, and fish finding equipment to both the recreational and commercial marine sectors, was facing significant challenges in its supply chain management. The company was unable to integrate commercial, supply, and demand planning due to many siloed processes, leading to lost sales and excess inventory. The lack of end-to-end (E2E) visibility and the inability to respond to changing market dynamics further exacerbated the situation. The company was unable to create true E2E visibility across the supply chain due to a variety of disconnected planning systems operating in a siloed environment. Additionally, the company frequently experienced both inventory excess and shortages, with only 10% of the SKUs having healthy inventory across the network. The forecast accuracy for demand, especially in connection to new product introduction, was rather low.
The Solution
The company partnered with o9 to leverage their highly differentiated Enterprise Knowledge Graph to integrate various planning functions and regions across the organization. This reduced overall E2E planning cycles and increased visibility and efficiency. The company improved its inventory management significantly by implementing statistical and supply-based safety stock calculations with o9. Supply planning was streamlined across its distribution network, including the creation of purchase orders and transfer orders. The company’s demand forecasting capability increased significantly through the implementation of rule-based demand forecasting depending on the product type. There were further improvements in the highly collaborative consensus forecast process across functions and regions. Leveraging o9’s digital planning and decision-making platform, the company was able to improve forecast accuracy, inventory health, and planner productivity through the implementation of a best-in-class integrated demand and supply planning solution. In addition, o9’s Control Tower implemented at the company provides tracking of key operational KPIs as well as providing tactical execution recommendations in the short term thereby improving customer OTIFs.
Operational Impact
Quantitative Benefit
Case Study missing?
Start adding your own!
Register with your work email and create a new case study profile for your business.
Related Case Studies.
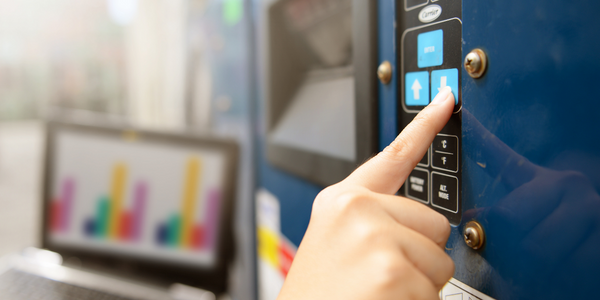
Case Study
Remote Temperature Monitoring of Perishable Goods Saves Money
RMONI was facing temperature monitoring challenges in a cold chain business. A cold chain must be established and maintained to ensure goods have been properly refrigerated during every step of the process, making temperature monitoring a critical business function. Manual registration practice can be very costly, labor intensive and prone to mistakes.
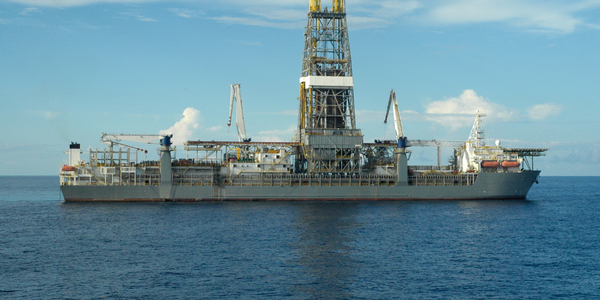
Case Study
Drill ship power challenge: hybrid solution solves distribution issues
Aspin Kemp & Associates (AKA), a manufacturer of electrical power and control systems headquartered in Montague, PEI, encountered one with its hybrid power initiative, the first hybrid drill floor destined for installation on ultra-deepwater drill ships operated by Transocean, Swiss offshore drilling contractors. Since on-site modification was impossible and scrap recycling of any modifications was unacceptable, the enclosures had to arrive ready-to-install.
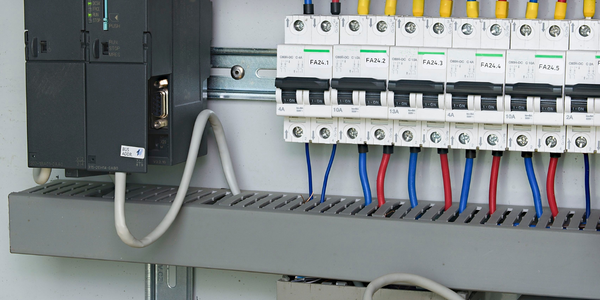
Case Study
Predictive maintenance in Schneider Electric
Schneider Electric Le Vaudreuil factory in France is recognized by the World Economic Forum as one of the world’s top nine most advanced “lighthouse” sites, applying Fourth Industrial Revolution technologies at large scale. It was experiencing machine-health and unplanned downtime issues on a critical machine within their manufacturing process. They were looking for a solution that could easily leverage existing machine data feeds, be used by machine operators without requiring complex setup or extensive training, and with a fast return on investment.
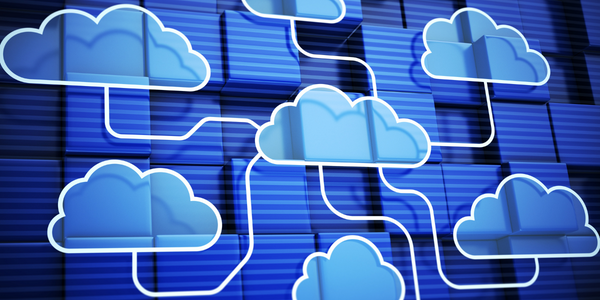
Case Study
Cloud Solution for Energy Management Platform-Schneider Electric
Schneider Electric required a cloud solution for its energy management platform to manage high computational operations, which were essential for catering to client requirements. As the business involves storage and analysis of huge amounts of data, the company also needed a convenient and scalable storage solution to facilitate operations efficiently.