Technology Category
- Drones - Drone Payloads & Accessories
- Functional Applications - Manufacturing Execution Systems (MES)
Applicable Industries
- Education
- Paper & Pulp
Applicable Functions
- Maintenance
- Quality Assurance
Use Cases
- Additive Manufacturing
- Manufacturing Process Simulation
Services
- Testing & Certification
- Training
About The Customer
Republic Manufacturing is a world-class producer of industrial blowers and vacuum pumps. Since 1962, they have been pushing the boundaries of modern manufacturing, leading them to design and create their own line of advanced products that continue to bring innovation to the industrial market. They are committed to providing value for both the customer and the company, understanding the importance of quality manufacturing and how work instruction software pushes quality to a new level. The company is known for its dedication to advancing the quality standards of the industry.
The Challenge
Republic Manufacturing, a leading producer of industrial blowers and vacuum pumps, was facing challenges in maintaining the highest levels of quality for their customers. Their inspection process was twofold, involving operators recording quality data and performing inspections during assembly, followed by Quality Control inspectors verifying the product once completed. This process, while ensuring quality, was time-consuming and complicated due to the use of paper-based inspection reports. The company was also struggling with training their workforce due to frequent product changes and variations. The traditional paper-based methods were not only inefficient but also prone to errors and loss of data.
The Solution
Republic Manufacturing turned to VKS, a work instruction software, to improve their quality methods, inspection processes, and workforce capabilities. The company implemented four methods that significantly improved their quality standards, productivity, and reduced total inspection time. Firstly, they digitized their inspection process, reducing quality control inspection times by 75%. Secondly, they used pictures to accurately show personnel the key inspection points, ensuring proper review. Thirdly, they digitized quality data such as serial numbers, torque specifications, and belt tensions, making them easy to access and impossible to lose. Lastly, they leveraged VKS to provide detailed inspection guidebooks for each unit, reducing the risk of inspectors forgetting to check something and enabling new inspectors to get on the floor sooner. The company also plans to implement VKS ToolConnect to apply correct torque values automatically while recording data for quality control.
Operational Impact
Quantitative Benefit
Case Study missing?
Start adding your own!
Register with your work email and create a new case study profile for your business.
Related Case Studies.
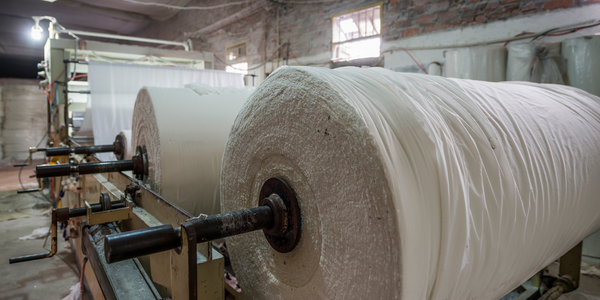
Case Study
Wireless Improves Efficiency in Compressed Air Systems
Hollingsworth and Vose wanted to improve the efficiency of their compressed air system, lower the electricity expense component of manufacturing cost in their commodity industry, and conserve energy leading to lowered greenhouse gas emissions. Compressed air systems degrade over time and become leaky and inefficient. Hollingsworth and Vose wanted to increase the frequency of system inspections without paying the high cost of manual labor.
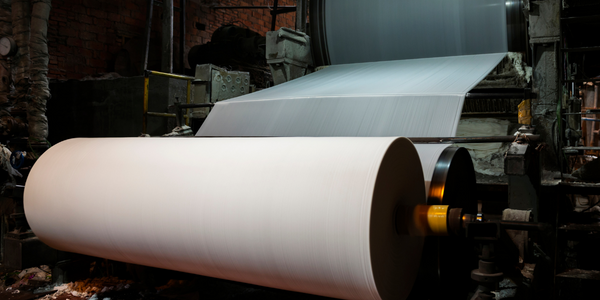
Case Study
Process Predictive Analysis in Pulp and Paper Mill
Common paper breaks consequently lead up to 60 minutes of downtime, delaying a potential $10K per hour of production value process. Thus, defective products cause financial and damage company's reputation. Improving quality and reducing defect rates can generate millions of dollars of revenue per year for your company.
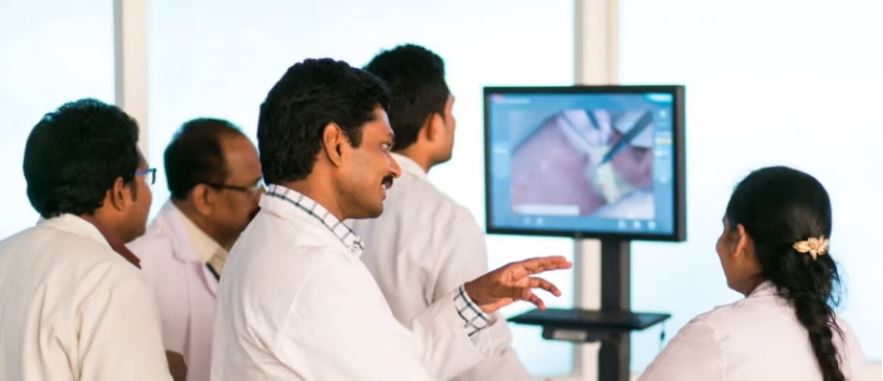
Case Study
Revolutionizing Medical Training in India: GSL Smart Lab and the LAP Mentor
The GSL SMART Lab, a collective effort of the GSL College of Medicine and the GSL College of Nursing and Health Science, was facing a challenge in providing superior training to healthcare professionals. As clinical medicine was becoming more focused on patient safety and quality of care, the need for medical simulation to bridge the educational gap between the classroom and the clinical environment was becoming increasingly apparent. Dr. Sandeep Ganni, the director of the GSL SMART Lab, envisioned a world-class surgical and medical training center where physicians and healthcare professionals could learn skills through simulation training. He was looking for different simulators for different specialties to provide both basic and advanced simulation training. For laparoscopic surgery, he was interested in a high fidelity simulator that could provide basic surgical and suturing skills training for international accreditation as well as specific hands-on training in complex laparoscopic procedures for practicing physicians in India.
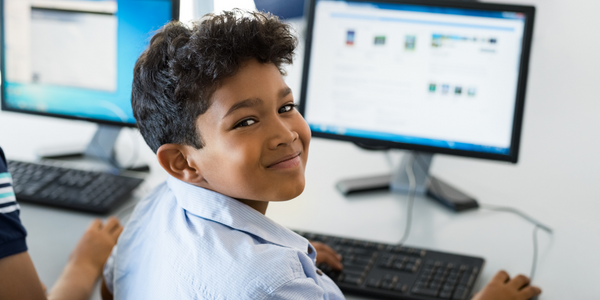
Case Study
IoT platform Enables Safety Solutions for U.S. School Districts
Designed to alert drivers when schoolchildren are present, especially in low-visibility conditions, school-zone flasher signals are typically updated manually at each school. The switching is based on the school calendar and manually changed when an unexpected early dismissal occurs, as in the case of a weather-event altering the normal schedule. The process to reprogram the flashers requires a significant effort by school district personnel to implement due to the large number of warning flashers installed across an entire school district.
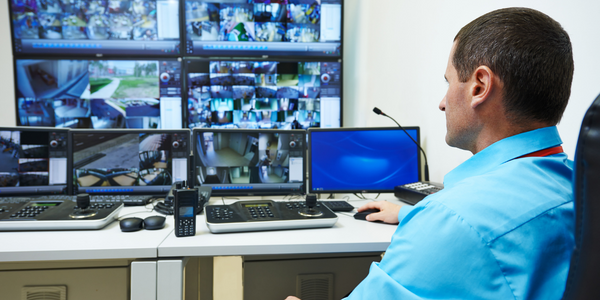
Case Study
Industrial Video Monitoring for Security and Regulatory Compliance
Because of the Stevenson mill’s proximity to the Tennessee River, WestRock was required by the USCG to comply with the Maritime Security 33CFR (MARSEC) regulations. WestRock needed a video security system but wanted to add other applications not required by the government, such as video process monitoring, condition monitoring, and wireless network management. WestRock needed a reliable video solution to avoid the compliance fines and possible security risks – but the solution needed to be implemented in the most cost-effective manner possible.