Technology Category
- Functional Applications - Inventory Management Systems
- Functional Applications - Warehouse Management Systems (WMS)
Applicable Industries
- Electronics
- Semiconductors
Applicable Functions
- Procurement
- Warehouse & Inventory Management
Use Cases
- Digital Twin
- Inventory Management
About The Customer
The customer is a global technology company that designs and manufactures semiconductors and software. They sell their products to electronic design engineers and manufacturers in markets worldwide. The company operates on an outsourced fabless model, which means they design and sell hardware devices and semiconductor chips but outsource the fabrication (or 'fab') of the devices and chips to a specialized manufacturer called a semiconductor foundry. This model requires extensive coordination and accurate planning to ensure efficiency and profitability.
The Challenge
The global technology company, a designer and manufacturer of semiconductors and software, was grappling with a highly manual and disconnected approach to managing their forecasts. The company relied heavily on spreadsheets, the Adexa system, and emails, which made the process inefficient and prone to errors. The supply side, which included inventory planning, order planning, and scheduling, was also entirely manual, necessitating extensive coordination due to the outsourced fabless model. The company's demand planning processes were not agile enough and lacked high accuracy levels. Furthermore, wafer inventory was challenging to manage and often too high due to the large dependency on manual planning. The order commit accuracy was poor, as the overall planning did not consider constraints and business rules.
The Solution
The company adopted the o9 platform to streamline their forecasting and planning processes. The platform enabled the company to create forecasts for all time horizons — weekly, monthly, quarterly, and annually — in both units and dollars. The o9 platform also improved the planning process for buffer planning and wafer planning on a fully integrated cloud-native platform, leading to more efficient and agile inventory management and reducing wafer inventory. The o9 Solver Capability was used to model constraints and business rules, such as customer-specific configurations, sourcing splits, inventory sweep, into the planning process. This made the overall planning more accurate and increased order promising performance. The o9’s Enterprise Knowledge Graph was used to optimize demand, buffer (MEIO), wafer, and supply planning. The company also replaced the Adexa system, homegrown solutions, and Excel with the o9 platform.
Operational Impact
Quantitative Benefit
Case Study missing?
Start adding your own!
Register with your work email and create a new case study profile for your business.
Related Case Studies.
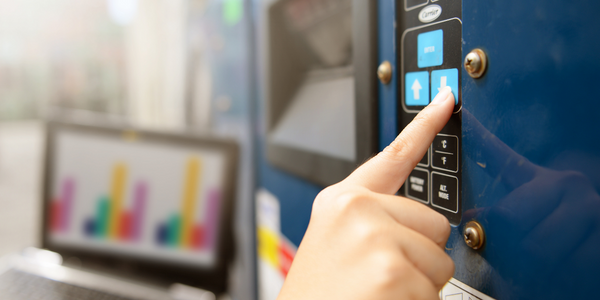
Case Study
Remote Temperature Monitoring of Perishable Goods Saves Money
RMONI was facing temperature monitoring challenges in a cold chain business. A cold chain must be established and maintained to ensure goods have been properly refrigerated during every step of the process, making temperature monitoring a critical business function. Manual registration practice can be very costly, labor intensive and prone to mistakes.
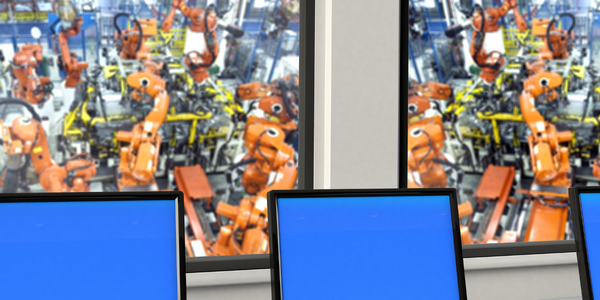
Case Study
KINESYS Semiconductor Factory Automation Software
KINESYS Software provides both Integrated Device Manufacturer (IDM) and Original Equipment Manufacturer (OEM) customers world-class software products and solutions for advanced wafer and device traceability and process management. KINESYS offers state of the art database technology with a core focus on SEMI standards. KINESYS’ challenge was to make back-end processing failure-free and easy to use for clients while supporting licensing models more adaptable to changing industry needs.
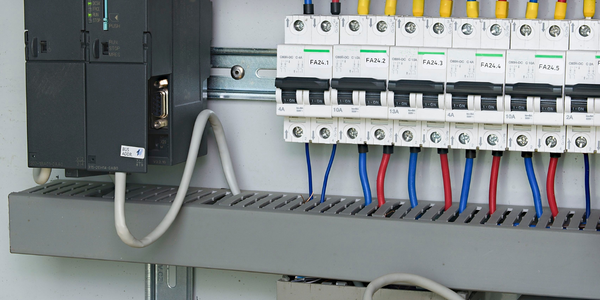
Case Study
Predictive maintenance in Schneider Electric
Schneider Electric Le Vaudreuil factory in France is recognized by the World Economic Forum as one of the world’s top nine most advanced “lighthouse” sites, applying Fourth Industrial Revolution technologies at large scale. It was experiencing machine-health and unplanned downtime issues on a critical machine within their manufacturing process. They were looking for a solution that could easily leverage existing machine data feeds, be used by machine operators without requiring complex setup or extensive training, and with a fast return on investment.
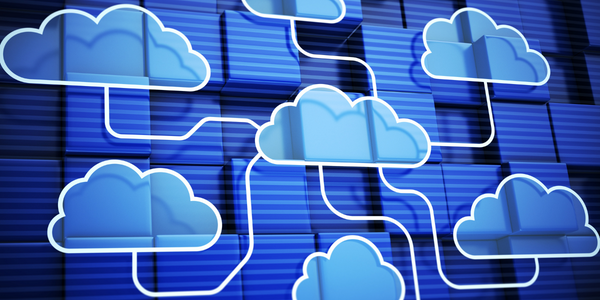
Case Study
Cloud Solution for Energy Management Platform-Schneider Electric
Schneider Electric required a cloud solution for its energy management platform to manage high computational operations, which were essential for catering to client requirements. As the business involves storage and analysis of huge amounts of data, the company also needed a convenient and scalable storage solution to facilitate operations efficiently.