Technology Category
- Networks & Connectivity - Gateways
- Robots - Autonomous Guided Vehicles (AGV)
Applicable Industries
- Automotive
- Telecommunications
Applicable Functions
- Product Research & Development
Use Cases
- Time Sensitive Networking
- Vehicle Performance Monitoring
Services
- Hardware Design & Engineering Services
- System Integration
About The Customer
The customer in this case study is a specialty vehicle manufacturer. They operate in a highly fragmented market, producing vehicles with unique requirements and capabilities such as ambulances, fire trucks, snow plows, and taxi cabs. Each of these vehicles has its own external hardware that interacts with the vehicle and its controls in a unique way. The manufacturer was struggling with the high cost and time-consuming process of creating custom gateway modules for each new vehicle or equipment model. They approached Flex with the aim of reducing their production costs and time to market.
The Challenge
Specialty vehicle manufacturers face a unique set of challenges due to the highly fragmented nature of their market. The design and production requirements for an ambulance, a fire truck, a snow plow, or a taxi cab are vastly different, each with its own unique external hardware that interacts with the vehicle and its controls. The gateway modules that connect this hardware to the vehicle are custom-made for each new vehicle or equipment model. This customization significantly increases the cost of design and production for specialty vehicle makers. Additionally, it also extends the time it takes to bring a specialty vehicle to market, with outfitters spending up to 18 months configuring the necessary custom hardware and software. One such manufacturer approached Flex, seeking a solution to reduce its production costs and time to market.
The Solution
Flex proposed a revolutionary solution to the client's problem - the Smart Gateway Module and FlexConfig app. This system replaces the traditional custom gateway module, eliminating the need for a new hardware and/or software configuration for every new specialty vehicle model. Instead, Flex's solution is a single, highly-configurable box that can be used across any new vehicle. The manufacturer, who previously required complex electrical engineering skills or even outsourcing to configure a gateway module, was now able to directly upgrade the software itself using the FlexConfig app that ships with the module. FlexConfig provides a simple graphical programming interface, enabling the manufacturer to cut valuable time from its production cycle by configuring the Smart Gateway Module to suit its own needs. Additionally, Flex also provided a telemetry system that enabled the vehicle to communicate effectively with central dispatch, offering real-time status updates and control over certain operational aspects.
Operational Impact
Quantitative Benefit
Case Study missing?
Start adding your own!
Register with your work email and create a new case study profile for your business.
Related Case Studies.
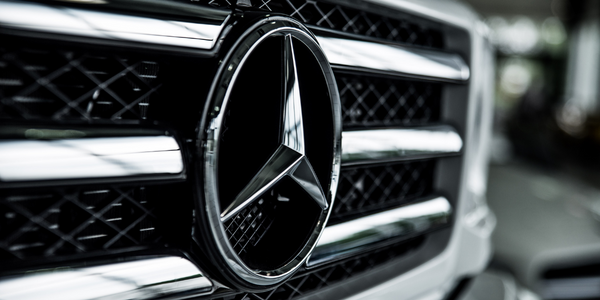
Case Study
Integral Plant Maintenance
Mercedes-Benz and his partner GAZ chose Siemens to be its maintenance partner at a new engine plant in Yaroslavl, Russia. The new plant offers a capacity to manufacture diesel engines for the Russian market, for locally produced Sprinter Classic. In addition to engines for the local market, the Yaroslavl plant will also produce spare parts. Mercedes-Benz Russia and his partner needed a service partner in order to ensure the operation of these lines in a maintenance partnership arrangement. The challenges included coordinating the entire maintenance management operation, in particular inspections, corrective and predictive maintenance activities, and the optimizing spare parts management. Siemens developed a customized maintenance solution that includes all electronic and mechanical maintenance activities (Integral Plant Maintenance).
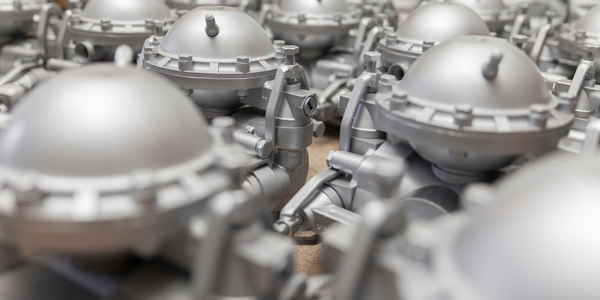
Case Study
Monitoring of Pressure Pumps in Automotive Industry
A large German/American producer of auto parts uses high-pressure pumps to deburr machined parts as a part of its production and quality check process. They decided to monitor these pumps to make sure they work properly and that they can see any indications leading to a potential failure before it affects their process.