Technology Category
- Platform as a Service (PaaS) - Application Development Platforms
- Sensors - Autonomous Driving Sensors
Applicable Industries
- Automotive
- Retail
Applicable Functions
- Logistics & Transportation
- Procurement
Use Cases
- Smart Parking
- Vehicle-to-Infrastructure
Services
- System Integration
About The Customer
Carvana is a revolutionary online used car retailer that is changing the way people buy cars. Founded in 2012 and headquartered in Tempe, Arizona, the company has over 1300 employees. Carvana's e-commerce platform, unique car vending machines, and home delivery service offer consumers an easier and more convenient way to buy a used car. Customers can search through an inventory of over 7,300 cars, finance, purchase, and trade in a car, all online. In 2016, customers who purchased a car through Carvana saved an average of $1,430 compared to the Kelley Blue Book suggested retail value. The company has experienced rapid growth, expanding from eight to 33 markets and a total of 40 business locations across the US in just 18 months.
The Challenge
Carvana, a fast-growing online used car retailer, was facing a communication challenge. The company's unique business model, which includes home delivery of vehicles and car vending machines, was being hampered by outdated communication practices. Carvana's External Advocates, the employees who deliver cars to customers' homes, were using their personal cell phones to communicate with customers. This led to a situation where post-delivery queries from customers, such as how to register the vehicle or operate its navigation system, were directed to these External Advocates who did not necessarily have the answers. The company needed a solution that would direct these calls to the right place, ensuring that customers received accurate and timely information. Additionally, the company's hardware-based PBX system was not scalable enough to support Carvana's rapid expansion from eight to 33 markets and 40 business locations across the US in just 18 months.
The Solution
Carvana's Director of Technology Services, Imran Kazi, decided to replace the company's hardware-based PBX system with RingCentral. This cloud-based communication platform offered the mobility support that Carvana needed, with the RingCentral Mobile app solving the problem of External Advocates receiving post-delivery calls on their personal cell phones. The scalability of the RingCentral platform was also a key factor in its selection, as it could support Carvana's rapid growth. Furthermore, RingCentral's integrations with G Suite and Okta were beneficial. The integration with Okta enabled Carvana to automate the provisioning of new RingCentral users directly from Carvana's Okta directory, streamlining the process of adding new employees. RingCentral was deployed across the organization, including at the Carvana headquarters, regional locations, and to the External Advocates.
Operational Impact
Quantitative Benefit
Case Study missing?
Start adding your own!
Register with your work email and create a new case study profile for your business.
Related Case Studies.
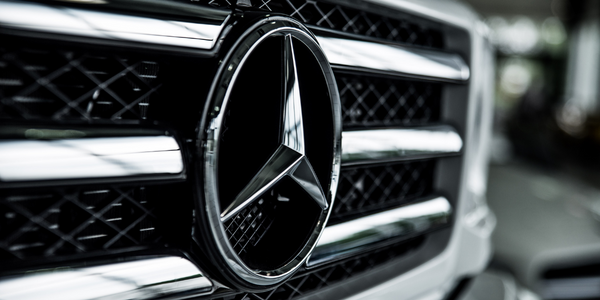
Case Study
Integral Plant Maintenance
Mercedes-Benz and his partner GAZ chose Siemens to be its maintenance partner at a new engine plant in Yaroslavl, Russia. The new plant offers a capacity to manufacture diesel engines for the Russian market, for locally produced Sprinter Classic. In addition to engines for the local market, the Yaroslavl plant will also produce spare parts. Mercedes-Benz Russia and his partner needed a service partner in order to ensure the operation of these lines in a maintenance partnership arrangement. The challenges included coordinating the entire maintenance management operation, in particular inspections, corrective and predictive maintenance activities, and the optimizing spare parts management. Siemens developed a customized maintenance solution that includes all electronic and mechanical maintenance activities (Integral Plant Maintenance).
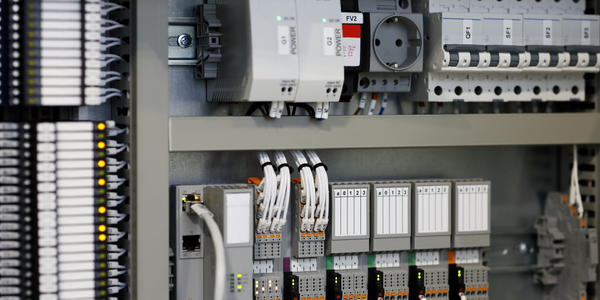
Case Study
Improving Production Line Efficiency with Ethernet Micro RTU Controller
Moxa was asked to provide a connectivity solution for one of the world's leading cosmetics companies. This multinational corporation, with retail presence in 130 countries, 23 global braches, and over 66,000 employees, sought to improve the efficiency of their production process by migrating from manual monitoring to an automatic productivity monitoring system. The production line was being monitored by ABB Real-TPI, a factory information system that offers data collection and analysis to improve plant efficiency. Due to software limitations, the customer needed an OPC server and a corresponding I/O solution to collect data from additional sensor devices for the Real-TPI system. The goal is to enable the factory information system to more thoroughly collect data from every corner of the production line. This will improve its ability to measure Overall Equipment Effectiveness (OEE) and translate into increased production efficiencies. System Requirements • Instant status updates while still consuming minimal bandwidth to relieve strain on limited factory networks • Interoperable with ABB Real-TPI • Small form factor appropriate for deployment where space is scarce • Remote software management and configuration to simplify operations