Technology Category
- Application Infrastructure & Middleware - Data Visualization
- Sensors - Level Sensors
Applicable Industries
- Automotive
- Transportation
Applicable Functions
- Logistics & Transportation
Use Cases
- Last Mile Delivery
- Supply Chain Visibility
About The Customer
Schmitz Cargobull AG is a family-run German company and Europe’s leading manufacturer of semi-trailers and trailers. The company attributes its success to its comprehensive brand strategy, consistent quality standards, and fulfilment of delivery promises despite short lead times and high demand volatility. The company operates on a global scale, with plants across Europe and Asia, and requires optimal network transparency to handle longer, more complex supply chains featuring greater interdependencies. Schmitz Cargobull has a broad supplier base located in 19 countries; these suppliers input to a total of 8 production facilities, and there are drop-off points for finished trailers in 25 countries.
The Challenge
Schmitz Cargobull AG, Europe’s leading manufacturer of semi-trailers and trailers, faced a significant challenge in managing its complex supply chain. The company, which produces over 45,000 vehicles annually and has a turnover of €1.6 billion, operates on a global scale with plants across Europe and Asia. Following rapid business growth and expansion into new geographies, Schmitz Cargobull needed better supply chain visibility and transparency on logistics flows, right down to component level. The company's trailer customers can typically change their order right up to the point of production, and some custom-built items must be urgently produced within 18 hours. The trailer subsector also features high demand volatility, requiring just-in-time and 100% make-to-order inbound supply chain processes. Schmitz Cargobull aimed to obtain a global yet detailed view of daily events, especially those impacting their own production sites or their global supplier base. They also wanted to improve efficiency and reduce logistics costs by building awareness and knowledge of Tier 1 suppliers and the outbound distribution network.
The Solution
Everstream Analytics provided Schmitz Cargobull with an interactive global map of its end-to-end supply chain to capture the logic of network interdependencies both upstream and downstream. This solution provided a multi-tiered view of all key component suppliers and logistical locations. Easy-to-use search and filter capabilities enabled Schmitz Cargobull supply chain executives to monitor products, parts, materials, and other sub-network attributes. For Schmitz Cargobull, supply chain visualization identified two significant risks: potential bottlenecks in the road network located in the southeastern region of Europe and the relative unfamiliarity of operating in China. Everstream customized a supply chain incident monitoring platform that provides 24/7 near real-time alerting and feedback loops on disruption occurring anywhere in the world. The platform also provides a feature to manually add incidents, enabling Schmitz Cargobull to quickly disseminate information about its network incidents across the organization. The flexibility of the Everstream Analytics solution meets Schmitz Cargobull’s specific needs, including a customized product view that connects sites and products according to the customer’s organizational structure.
Operational Impact
Quantitative Benefit
Case Study missing?
Start adding your own!
Register with your work email and create a new case study profile for your business.
Related Case Studies.
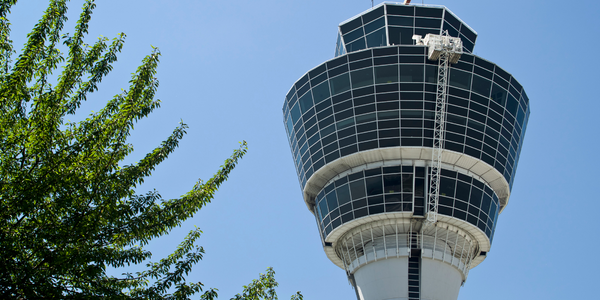
Case Study
Airport SCADA Systems Improve Service Levels
Modern airports are one of the busiest environments on Earth and rely on process automation equipment to ensure service operators achieve their KPIs. Increasingly airport SCADA systems are being used to control all aspects of the operation and associated facilities. This is because unplanned system downtime can cost dearly, both in terms of reduced revenues and the associated loss of customer satisfaction due to inevitable travel inconvenience and disruption.
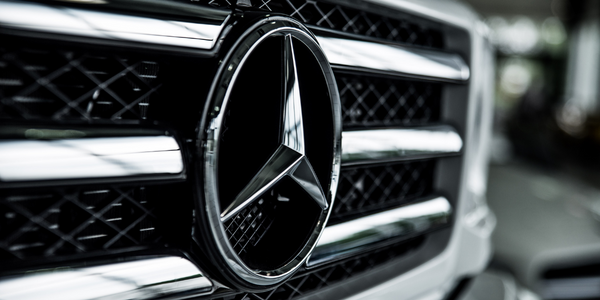
Case Study
Integral Plant Maintenance
Mercedes-Benz and his partner GAZ chose Siemens to be its maintenance partner at a new engine plant in Yaroslavl, Russia. The new plant offers a capacity to manufacture diesel engines for the Russian market, for locally produced Sprinter Classic. In addition to engines for the local market, the Yaroslavl plant will also produce spare parts. Mercedes-Benz Russia and his partner needed a service partner in order to ensure the operation of these lines in a maintenance partnership arrangement. The challenges included coordinating the entire maintenance management operation, in particular inspections, corrective and predictive maintenance activities, and the optimizing spare parts management. Siemens developed a customized maintenance solution that includes all electronic and mechanical maintenance activities (Integral Plant Maintenance).
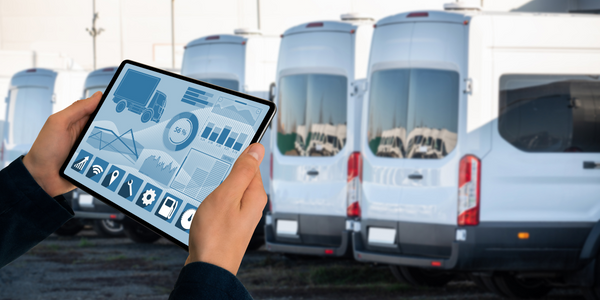
Case Study
IoT-based Fleet Intelligence Innovation
Speed to market is precious for DRVR, a rapidly growing start-up company. With a business model dependent on reliable mobile data, managers were spending their lives trying to negotiate data roaming deals with mobile network operators in different countries. And, even then, service quality was a constant concern.
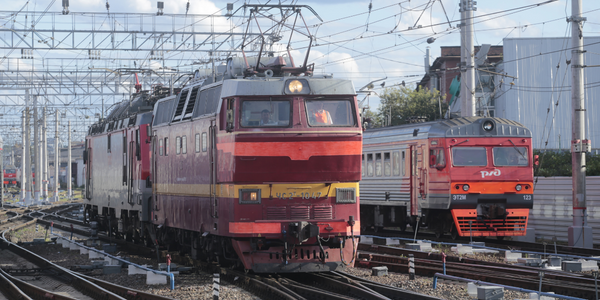
Case Study
Digitize Railway with Deutsche Bahn
To reduce maintenance costs and delay-causing failures for Deutsche Bahn. They need manual measurements by a position measurement system based on custom-made MEMS sensor clusters, which allow autonomous and continuous monitoring with wireless data transmission and long battery. They were looking for data pre-processing solution in the sensor and machine learning algorithms in the cloud so as to detect critical wear.
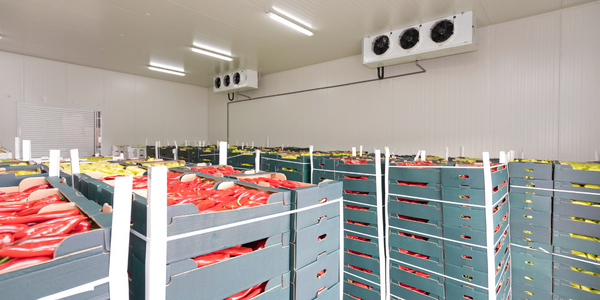
Case Study
Cold Chain Transportation and Refrigerated Fleet Management System
1) Create a digital connected transportation solution to retrofit cold chain trailers with real-time tracking and controls. 2) Prevent multi-million dollar losses due to theft or spoilage. 3) Deliver a digital chain-of-custody solution for door to door load monitoring and security. 4) Provide a trusted multi-fleet solution in a single application with granular data and access controls.