Applicable Industries
- Consumer Goods
About The Customer
The customer in this case study is Kimberly-Clark, a multinational personal care corporation that produces mostly paper-based consumer products. Kimberly-Clark brand name products include Kleenex facial tissue, Kotex feminine hygiene products, Cottonelle, Scott and Andrex toilet paper, Wypall utility wipes, KimWipes scientific cleaning wipes, and Huggies disposable diapers and baby wipes. Scott Duramax is one of the products under the Kimberly-Clark umbrella. The company was looking to launch Scott Duramax, a semi-disposable cloth, in a new market and needed a strategy to generate brand awareness and convince consumers to choose their product over others.
The Challenge
In 2015, Scott Duramax, a product of Kimberly-Clark, was faced with the challenge of entering a new market. The company was looking for a way to generate brand awareness, instigate experimentation, ensure product visibility, and establish a close relationship with consumers. The ultimate goal was to convince the Brazilian consumer that Scott Duramax is the best option of semi-disposable cloths. The challenge was not only to introduce a new product but also to create a memorable brand image that would resonate with the consumers and encourage them to choose Scott Duramax over other brands.
The Solution
To overcome the challenge, a unique marketing strategy was implemented. A comedic three-part series was created, showcasing real-life comic situations in the life of a couple. The different parts of the series highlighted the difference between normal rags and Scott Duramax, creating memorable characters for the consumer to relate to. This innovative approach was designed to not only promote the product but also to engage the consumers on a deeper level. By using humor and relatable situations, the campaign aimed to create a strong connection between the consumers and the brand, thereby increasing the chances of product adoption.
Operational Impact
Quantitative Benefit
Case Study missing?
Start adding your own!
Register with your work email and create a new case study profile for your business.
Related Case Studies.
.png)
Case Study
Improving Vending Machine Profitability with the Internet of Things (IoT)
The vending industry is undergoing a sea change, taking advantage of new technologies to go beyond just delivering snacks to creating a new retail location. Intelligent vending machines can be found in many public locations as well as company facilities, selling different types of goods and services, including even computer accessories, gold bars, tickets, and office supplies. With increasing sophistication, they may also provide time- and location-based data pertaining to sales, inventory, and customer preferences. But at the end of the day, vending machine operators know greater profitability is driven by higher sales and lower operating costs.
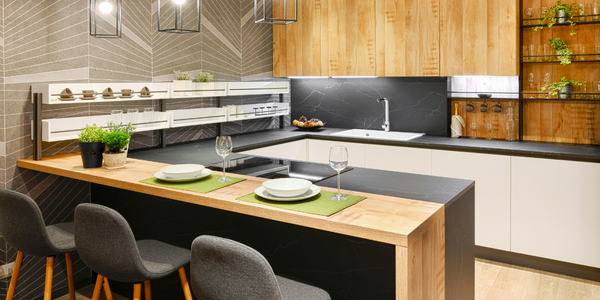
Case Study
Series Production with Lot-size-1 Flexibility
Nobilia manufactures customized fitted kitchens with a lot size of 1. They require maximum transparency of tracking design data and individual processing steps so that they can locate a particular piece of kitchen furniture in the sequence of processes.
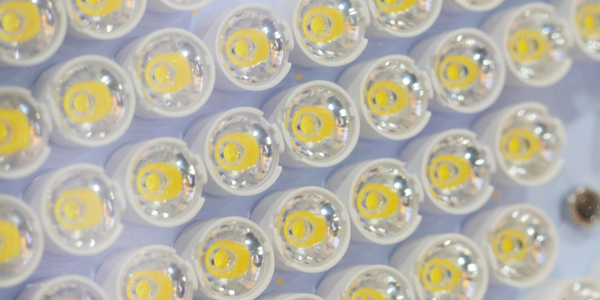
Case Study
American Eagle Achieves LEED with GE LED Lighting Fixtures
American Eagle Outfitters (AEO) was in the process of building a new distribution center. The AEO facility management team decided to look at alternate options for lighting layout that could provide energy and maintenance savings. AEO would need a full-time maintenance employee just to replace burned-out fluorescent tubes.
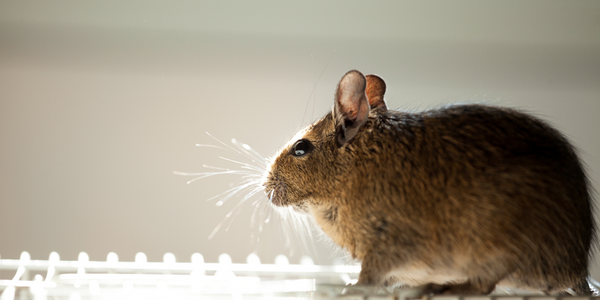
Case Study
Revolutionizing Rodent Control
From pet- and child-safe traps, to touch-free and live-catch rodent control solutions, Victor continues to stay committed to producing superior products that meet the varying needs of today’s pest control professionals. And, with a long standing history supporting customers in the food processing, service, and retail settings, Victor knew that strict regulations were costing organizations thousands of dollars in excess overhead trying to manage their rodent-control solutions. Trap inspections in these environments are often difficult and time consuming, requiring personnel to manually check a trap’s status multiple times per day, amounting to over six hours of manual labor. Victor is looking for an innovative way to increase operational efficiencies with the use of technology.