Service Center Wheel Alignment Coupon
Customer Company Size
Large Corporate
Region
- America
Country
- United States
Product
- APT Test & Learn software
Tech Stack
- Business Experimentation Software
- Data Analytics
Implementation Scale
- Departmental Deployment
Impact Metrics
- Revenue Growth
- Customer Satisfaction
- Productivity Improvements
Technology Category
- Analytics & Modeling - Predictive Analytics
- Analytics & Modeling - Real Time Analytics
Applicable Industries
- Automotive
Applicable Functions
- Sales & Marketing
- Business Operation
Use Cases
- Predictive Replenishment
Services
- Data Science Services
- System Integration
About The Customer
The customer is a large chain of auto service centers that provides various automotive services, including wheel alignments. The company is interested in leveraging promotions and coupons to increase customer traffic and drive incremental business. With a significant number of locations, the company aims to understand the effectiveness of its marketing strategies and optimize them for better profitability. The auto service centers cater to a diverse customer base, including both new and loyal customers, and operate in various competitive and income-diverse areas.
The Challenge
A large chain of auto service centers wanted to use coupons to drive traffic to its locations. The company offered targeted coupons for its wheel alignment service, redeemable during a month-long period. The challenge was to determine if the promotion drove incremental transactions or merely subsidized existing purchasing behavior. The inherent noise in daily invoices data made it difficult to isolate the coupon's impact, complicating the understanding of whether the coupon was driving new business or just giving away money to customers who would have purchased anyway.
The Solution
The auto service center utilized APT’s Test & Learn software to analyze an in-market business experiment measuring the impact of the targeted wheel alignment coupon. The software compared 'test centers' that distributed the coupon to 'control centers' that did not, isolating the incremental impact of the promotion. The analysis revealed a 12.1% increase in wheel alignment invoices during the redemption period without a pull-forward effect in the following month. However, the increase in invoices did not offset the decline in margin per transaction, leading to a moderate overall margin decline. Further analysis showed the coupon was profitable due to a significant increase in rest-of-basket margin, driven by new customers. The software identified service center attributes associated with higher invoice lifts, such as competitive areas, lower income areas, and fewer past promotional events. APT software then generated a list of service centers predicted to respond best to the coupon, enabling targeted future rollouts and driving an incremental $1.6MM in annual margin.
Operational Impact
Quantitative Benefit
Case Study missing?
Start adding your own!
Register with your work email and create a new case study profile for your business.
Related Case Studies.
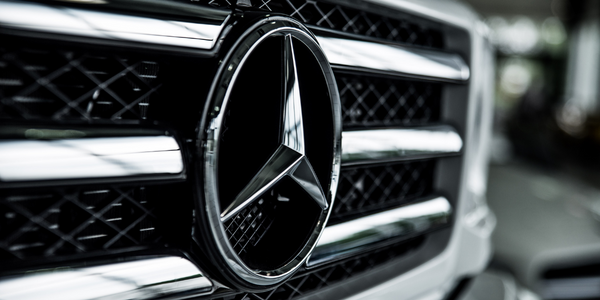
Case Study
Integral Plant Maintenance
Mercedes-Benz and his partner GAZ chose Siemens to be its maintenance partner at a new engine plant in Yaroslavl, Russia. The new plant offers a capacity to manufacture diesel engines for the Russian market, for locally produced Sprinter Classic. In addition to engines for the local market, the Yaroslavl plant will also produce spare parts. Mercedes-Benz Russia and his partner needed a service partner in order to ensure the operation of these lines in a maintenance partnership arrangement. The challenges included coordinating the entire maintenance management operation, in particular inspections, corrective and predictive maintenance activities, and the optimizing spare parts management. Siemens developed a customized maintenance solution that includes all electronic and mechanical maintenance activities (Integral Plant Maintenance).
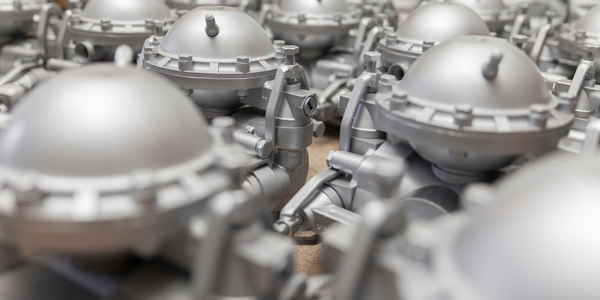
Case Study
Monitoring of Pressure Pumps in Automotive Industry
A large German/American producer of auto parts uses high-pressure pumps to deburr machined parts as a part of its production and quality check process. They decided to monitor these pumps to make sure they work properly and that they can see any indications leading to a potential failure before it affects their process.