SFI Speeds Response Times and Business Growth with aPriori
Customer Company Size
Large Corporate
Region
- America
Country
- United States
Product
- aPriori
Tech Stack
- 3D CAD Models
- Pro/ENGINEER
- CATIA v5
- Siemens NX
- Solidworks
- SolidEdge
- Inventor
Implementation Scale
- Enterprise-wide Deployment
Impact Metrics
- Productivity Improvements
- Customer Satisfaction
- Digital Expertise
Technology Category
- Functional Applications - Product Lifecycle Management Systems (PLM)
- Analytics & Modeling - Predictive Analytics
- Application Infrastructure & Middleware - Data Exchange & Integration
Applicable Industries
- Automotive
- Construction & Infrastructure
Applicable Functions
- Product Research & Development
- Quality Assurance
- Sales & Marketing
Use Cases
- Predictive Maintenance
- Process Control & Optimization
- Digital Twin
Services
- Software Design & Engineering Services
- System Integration
- Training
About The Customer
SFI (Steel Fabrication Inc.) provides contract design, development, supply and value-added services for medium to heavy gauge components to a select group of original equipment manufacturers (OEM) in the agricultural, automotive, construction, industrial, transportation and defense industries. This includes welded parts for commercial automotive manufacturers and vehicle sub-frames for the U.S. military. Since its founding in 1956, the company has grown to become the leading OEM parts manufacturer in the nation. Today it employs over 600 skilled professionals and operates three locations in Memphis, Tennessee; Conway, Arkansas and New Boston, Ohio. Together these facilities provide over one million square feet of state-of-the-art production space fully dedicated to steel fabrication solutions. This enables SFI to offer a full spectrum of process operations, including press brake, roll forming, coil processing, laser cutting, stamping, welding, machining, powder coat painting and assembly. Whether an OEM needs press braking capability up to 28 feet, stamping presses up to 2000 tons or a 5 axis machining center to handle a 40 ton part, SFI has all the capabilities to handle it quickly and efficiently.
The Challenge
For any contract manufacturer, accurate and timely project quoting is a critical success factor. It can make the difference between winning and losing business and making and losing money. And like many others, SFI’s estimators used its own unique blend of different cost calculators, spreadsheets and off-the-shelf cost management tools. It was all very manual and time consuming. In most cases, SFI’s Cost Estimators had to analyze a series of 2-D drawings and then add in each, different attributes, runs rates, parts and labor costs. A big project with 500 different parts could takes weeks or more to quote. In some cases, SFI was getting 3-D models from customers and then taking the time to turn them into 2-D prints. This created a lot of unnecessary extra work and extended the quoting time frame from days to weeks. All this manual effort meant more time spent responding to customer quote requests, more overhead, difficult tradeoffs on priorities and even “no-quoting” some jobs which negatively impacted potential future business. SFI’s estimating team felt it was always playing catch up. Every customer wanted their quotes yesterday because they were likely already behind on their own schedule.
The Solution
Sale engineers and cost management expert Hashim Alsaffar joined SFI in September 2010. At that time, SFI was piloting a new product cost management solution from aPriori. He remembers hearing about it when he was interviewing and he was intrigued. With aPriori, SFI said it could quickly and accurately cost out any part or product from a CAD model. It was very compelling to me as a candidate and I saw a lot of potential with the capability. If it did what they said it could, we could really accelerate our response time and accuracy on project quotes. It seemed like a really big competitive advantage. Since then, Alsaffar has become the go to person at SFI for all things related to aPriori. With aPriori, we get ahead of the whole process,” says Alsaffar. We can respond more quickly to customer requests for quotes, respond to more requests overall, and equally important, see immediately whether or not a job is really in our sweet spot. This is good for both SFI and the customer. It makes us a better, value-added supplier because aPriori makes our team and our customers more knowledgeable about the requirements of a project. It also has a positive effect on the customer's overall time to market. The key is aPriori’s ability to quickly analyze any part or product from a CAD model and break it down to the lowest possible level of cost detail. aPriori also provides complete CAD independence. It can work with 3D CAD models generated by any major CAD modeling system on the market today, including: Pro/ENGINEER, CATIA v5, Siemens NX, Solidworks, SolidEdge and Inventor to name a few. So, no matter what type of CAD model the customer sends, aPriori can quickly open that model and generate a cost estimate in seconds. You don’t even have to own a license of the source CAD system to open the model in aPriori.
Operational Impact
Quantitative Benefit
Case Study missing?
Start adding your own!
Register with your work email and create a new case study profile for your business.
Related Case Studies.
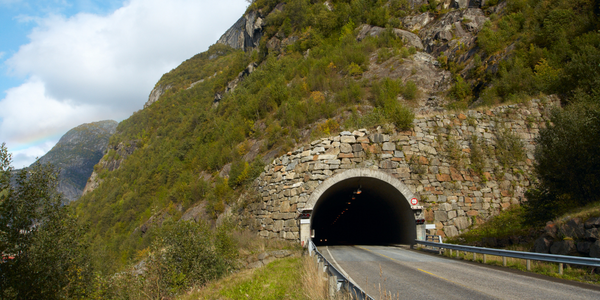
Case Study
IoT System for Tunnel Construction
The Zenitaka Corporation ('Zenitaka') has two major business areas: its architectural business focuses on structures such as government buildings, office buildings, and commercial facilities, while its civil engineering business is targeted at structures such as tunnels, bridges and dams. Within these areas, there presented two issues that have always persisted in regard to the construction of mountain tunnels. These issues are 'improving safety" and "reducing energy consumption". Mountain tunnels construction requires a massive amount of electricity. This is because there are many kinds of electrical equipment being used day and night, including construction machinery, construction lighting, and ventilating fan. Despite this, the amount of power consumption is generally not tightly managed. In many cases, the exact amount of power consumption is only ascertained when the bill from the power company becomes available. Sometimes, corporations install demand-monitoring equipment to help curb the maximum power demanded. However, even in these cases, the devices only allow the total volume of power consumption to be ascertained, or they may issue warnings to prevent the contracted volume of power from being exceeded. In order to tackle the issue of reducing power consumption, it was first necessary to obtain an accurate breakdown of how much power was being used in each particular area. In other words, we needed to be able to visualize the amount of power being consumed. Safety, was also not being managed very rigorously. Even now, tunnel construction sites often use a 'name label' system for managing entry into the work site. Specifically, red labels with white reverse sides that bear the workers' names on both sides are displayed at the tunnel work site entrance. The workers themselves then flip the name label to the appropriate side when entering or exiting from the work site to indicate whether or not they are working inside the tunnel at any given time. If a worker forgets to flip his or her name label when entering or exiting from the tunnel, management cannot be performed effectively. In order to tackle the challenges mentioned above, Zenitaka decided to build a system that could improve the safety of tunnel construction as well as reduce the amount of power consumed. In other words, this new system would facilitate a clear picture of which workers were working in each location at the mountain tunnel construction site, as well as which processes were being carried out at those respective locations at any given time. The system would maintain the safety of all workers while also carefully controlling the electrical equipment to reduce unnecessary power consumption. Having decided on the concept, our next concern was whether there existed any kind of robust hardware that would not break down at the construction work site, that could move freely in response to changes in the working environment, and that could accurately detect workers and vehicles using radio frequency identification (RFID). Given that this system would involve many components that were new to Zenitaka, we decided to enlist the cooperation of E.I.Sol Co., Ltd. ('E.I.Sol') as our joint development partner, as they had provided us with a highly practical proposal.
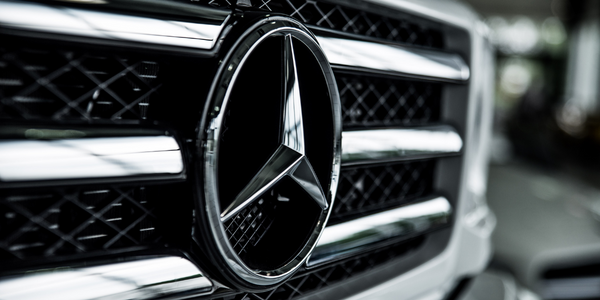
Case Study
Integral Plant Maintenance
Mercedes-Benz and his partner GAZ chose Siemens to be its maintenance partner at a new engine plant in Yaroslavl, Russia. The new plant offers a capacity to manufacture diesel engines for the Russian market, for locally produced Sprinter Classic. In addition to engines for the local market, the Yaroslavl plant will also produce spare parts. Mercedes-Benz Russia and his partner needed a service partner in order to ensure the operation of these lines in a maintenance partnership arrangement. The challenges included coordinating the entire maintenance management operation, in particular inspections, corrective and predictive maintenance activities, and the optimizing spare parts management. Siemens developed a customized maintenance solution that includes all electronic and mechanical maintenance activities (Integral Plant Maintenance).
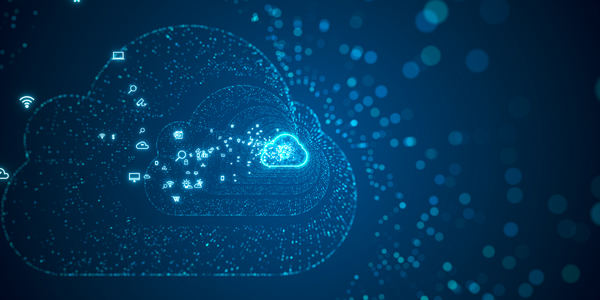
Case Study
Splunk Partnership Ties Together Big Data & IoT Services
Splunk was faced with the need to meet emerging customer demands for interfacing IoT projects to its suite of services. The company required an IoT partner that would be able to easily and quickly integrate with its Splunk Enterprise platform, rather than allocating development resources and time to building out an IoT interface and application platform.