Customer Company Size
Mid-size Company
Region
- America
Country
- United States
Product
- Sage ERP X3
Tech Stack
- Enterprise Resource Planning (ERP)
Implementation Scale
- Enterprise-wide Deployment
Impact Metrics
- Customer Satisfaction
- Productivity Improvements
Technology Category
- Functional Applications - Enterprise Resource Planning Systems (ERP)
Applicable Industries
- Automotive
Applicable Functions
- Discrete Manufacturing
- Sales & Marketing
Use Cases
- Supply Chain Visibility
- Demand Planning & Forecasting
Services
- System Integration
About The Customer
Sonnax Industries, Inc. is a manufacturer and distributor of components to the automatic transmission aftermarket. The company is based in Bellows Falls, Vermont, and employs around 200 people. Sonnax utilizes a unique collaborative professional network of design engineers, technical experts, and shop technicians to analyze mechanical problems in existing units and respond to them with innovative, durable, cost-effective replacement parts. The company has built its reputation on quality and customer service. Its 800 customers nationwide depend on fast delivery of replacement parts to get their customers’ cars out of the shop and back on the road as quickly as possible.
The Challenge
Sonnax Industries, a Vermont-based company that designs, produces, and supplies components to the automatic transmission aftermarket, was facing challenges with its nearly decade-old enterprise software. The software was struggling to keep up with the company's steady growth and meet the requirements for fast turnaround of more than 40,000 shipments a year. Sonnax knew that the system would not be able to handle the increased demand for aftermarket parts that it saw coming in the next decade or process orders quickly enough to keep its customers satisfied. Updating the system to the current version would require a major investment in hardware, software, and integration. Therefore, Sonnax decided to look for alternatives and replace the system with new technology.
The Solution
Sonnax contracted a consultant from the Vermont Manufacturing Extension Center (VMEC) to determine the best enterprise solution for its business. VMEC recommended using an enterprise resource planning (ERP) and business software planning site that helps businesses select the right system and provides up-to-date, objective software data for businesses. Sage ERP X3 was identified as the solution that met Sonnax’s requirements for tight integration, ease of configuration, and advanced functionality. Unlike many enterprise software packages that consist of separate products bolted together from different sources, Sage ERP X3 offers tightly integrated applications that provide a quick turnaround for customer inquiries and ensure that an order is ready to ship within no more than six hours after receipt.
Operational Impact
Case Study missing?
Start adding your own!
Register with your work email and create a new case study profile for your business.
Related Case Studies.
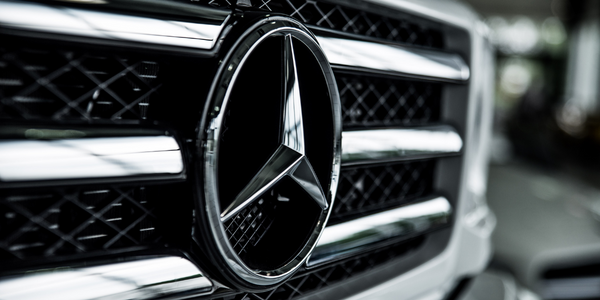
Case Study
Integral Plant Maintenance
Mercedes-Benz and his partner GAZ chose Siemens to be its maintenance partner at a new engine plant in Yaroslavl, Russia. The new plant offers a capacity to manufacture diesel engines for the Russian market, for locally produced Sprinter Classic. In addition to engines for the local market, the Yaroslavl plant will also produce spare parts. Mercedes-Benz Russia and his partner needed a service partner in order to ensure the operation of these lines in a maintenance partnership arrangement. The challenges included coordinating the entire maintenance management operation, in particular inspections, corrective and predictive maintenance activities, and the optimizing spare parts management. Siemens developed a customized maintenance solution that includes all electronic and mechanical maintenance activities (Integral Plant Maintenance).
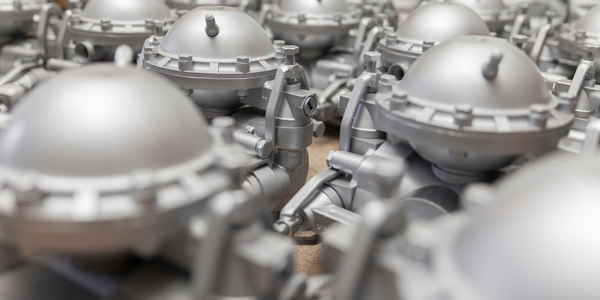
Case Study
Monitoring of Pressure Pumps in Automotive Industry
A large German/American producer of auto parts uses high-pressure pumps to deburr machined parts as a part of its production and quality check process. They decided to monitor these pumps to make sure they work properly and that they can see any indications leading to a potential failure before it affects their process.