Technology Category
- Analytics & Modeling - Real Time Analytics
- Sensors - Temperature Sensors
Applicable Industries
- Electrical Grids
- Renewable Energy
Applicable Functions
- Maintenance
- Product Research & Development
Use Cases
- Construction Management
- Digital Twin
About The Customer
Sterlite Power Transmission Limited is a leading global developer of India's energy transmission infrastructure projects. The company was awarded the NER-II Transmission Limited Project by the Ministry of Power as part of India's commitment to economic development in the northeast region and to renewable energy targets aimed at quickly reducing carbon emissions. The project was aimed at serving a population of over 30 million residents in India's most remote areas, aiming to improve reliability of the power supply, reduce intermittency, and accelerate the penetration of renewables in the northeast region. Sterlite Power's mission was to remove infrastructure bottlenecks and create a conducive environment for sustainable power supply.
The Challenge
Sterlite Power Transmission Limited was tasked with the NER-II Transmission Limited Project, a INR 1.95 billion renewable energy initiative aimed at serving over 30 million residents in India's most remote areas. The project involved developing transmission lines spanning 448 kilometers and constructing a 400-kilovolt/132 kilovolt substation in the state of Tripura. The substation was critical for delivering power to Tripura and needed to be completed quickly. However, the project faced several challenges. The geographical and environmental conditions were complex, with the project site located at the foothills of the Himalayas amid dense forest subject to heavy rains and flooding. The tight timeline and resistance from the indigenous population added to the complexity. Sterlite Power's traditional 2D design methods for substation planning had minimal data-sharing potential and did not support the design team's needs for detecting potential clearance problems between electrical components and support structures. Their conventional software had limited capability in terms of managing interdependencies and linking design, planning, and construction works. These inefficiencies posed enormous risks in the substation timeline, prolonging inspection, stakeholder approval, and handovers.
The Solution
To overcome these challenges, Sterlite Power adopted digital twin technology and established an open, connected data environment using Bentley's OpenUtilities Substation and ProjectWise. This switch allowed them to establish a 3D collaborative modeling environment to streamline design workflows, facilitate accurate information sharing, and enable early clash detection among structures and equipment. They developed a digital component library that provided traceability and accountability for design, exporting these component models as symbols to develop the entire substation model layout and ensure proper connection among the equipment. This approach facilitated seamless and accurate information sharing among the team and stakeholders, helping to overcome the design challenges and secure permission from local authorities to lay the transmission lines. To further refine design and enhance construction planning, Sterlite Power adopted 4D BIM technology using SYNCHRO, performing real-time, virtual construction monitoring and simulation. This software allowed for robust planning, linking design and scheduling processes and then mapping all project activities to the 3D model for greater visibility into the project plan. The digital model helped visualize the impact of design changes, facilitating accurate, data-driven decisions and avoiding construction errors on site.
Operational Impact
Quantitative Benefit
Case Study missing?
Start adding your own!
Register with your work email and create a new case study profile for your business.
Related Case Studies.

Case Study
Remote Monitoring & Predictive Maintenance App for a Solar Energy System
The maintenance & tracking of various modules was an overhead for the customer due to the huge labor costs involved. Being an advanced solar solutions provider, they wanted to ensure early detection of issues and provide the best-in-class customer experience. Hence they wanted to automate the whole process.
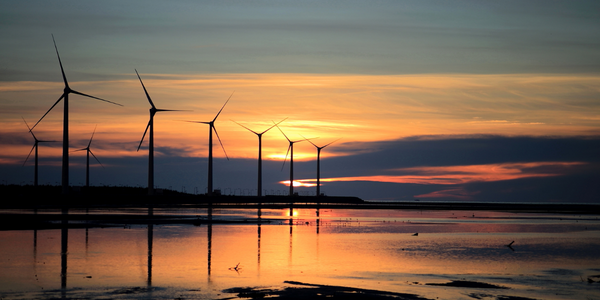
Case Study
Vestas: Turning Climate into Capital with Big Data
Making wind a reliable source of energy depends greatly on the placement of the wind turbines used to produce electricity. Turbulence is a significant factor as it strains turbine components, making them more likely to fail. Vestas wanted to pinpoint the optimal location for wind turbines to maximize power generation and reduce energy costs.
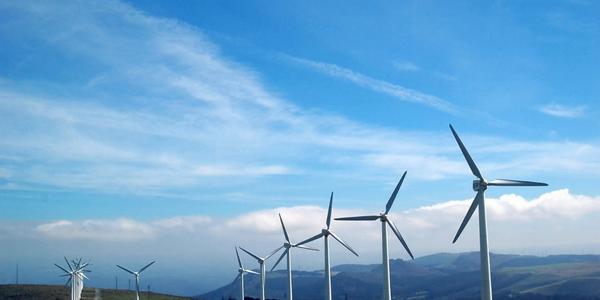
Case Study
Siemens Wind Power
Wind provides clean, renewable energy. The core concept is simple: wind turbines spin blades to generate power. However, today's systems are anything but simple. Modern wind turbines have blades that sweep a 120 meter circle, cost more than 1 million dollars and generate multiple megawatts of power. Each turbine may include up to 1,000 sensors and actuators – integrating strain gages, bearing monitors and power conditioning technology. The turbine can control blade speed and power generation by altering the blade pitch and power extraction. Controlling the turbine is a sophisticated job requiring many cooperating processors closing high-speed loops and implementing intelligent monitoring and optimization algorithms. But the real challenge is integrating these turbines so that they work together. A wind farm may include hundreds of turbines. They are often installed in difficult-to-access locations at sea. The farm must implement a fundamentally and truly distributed control system. Like all power systems, the goal of the farm is to match generation to load. A farm with hundreds of turbines must optimize that load by balancing the loading and generation across a wide geography. Wind, of course, is dynamic. Almost every picture of a wind farm shows a calm sea and a setting sun. But things get challenging when a storm goes through the wind farm. In a storm, the control system must decide how to take energy out of gusts to generate constant power. It must intelligently balance load across many turbines. And a critical consideration is the loading and potential damage to a half-billion-dollar installed asset. This is no environment for a slow or undependable control system. Reliability and performance are crucial.
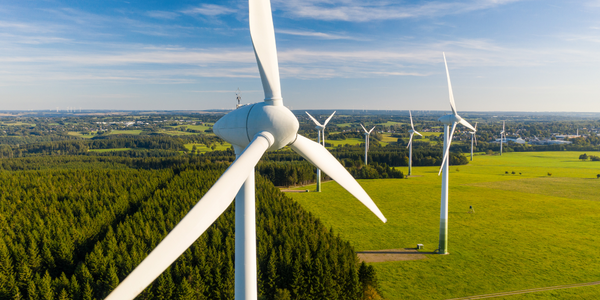
Case Study
Remote Monitoring and Control for a Windmill Generator
As concerns over global warming continue to grow, green technologies are becoming increasingly popular. Wind turbine companies provide an excellent alternative to burning fossil fuels by harnessing kinetic energy from the wind and converting it into electricity. A typical wind farm may include over 80 wind turbines so efficient and reliable networks to manage and control these installations are imperative. Each wind turbine includes a generator and a variety of serial components such as a water cooler, high voltage transformer, ultrasonic wind sensors, yaw gear, blade bearing, pitch cylinder, and hub controller. All of these components are controlled by a PLC and communicate with the ground host. Due to the total integration of these devices into an Ethernet network, one of our customers in the wind turbine industry needed a serial-to-Ethernet solution that can operate reliably for years without interruption.
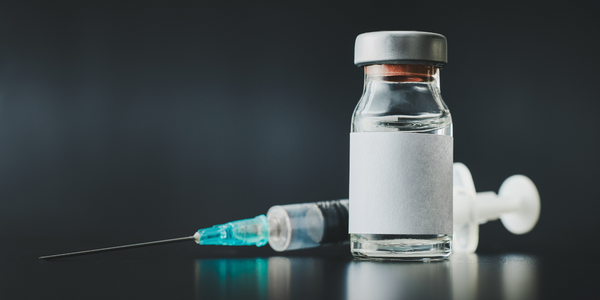
Case Study
Temperature monitoring for vaccine fridges
Dulas wanted a way to improve the reliability of the cold chain, facilitating maintenance and ensuring fewer vaccines are spoiled. Dulas wanted an M2M solution which would enable them to record and report the temperature inside vaccine refrigerators.
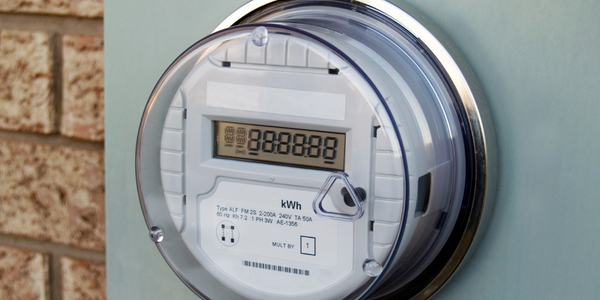
Case Study
Hydro One Leads the Way In Smart Meter Development
In 2010, Ontario’s energy board mandated that time-of-use (TOU) pricing for consumers be available for all consumers on a regulated price plan. To meet this requirement, Hydro One needed to quickly deploy a smart meter and intelligent communications network solution to meet the provincial government’s requirement at a low cost. The network needed to cover Hydro One’s expansive service territory, which has a land mass twice the size of Texas, and its customers live in a mix of urban, rural, and remote areas, some places only accessible by air, rail, boat or snowmobile. Most importantly, the network needed to enable future enterprise-wide business efficiencies, modernization of distribution infrastructure and enhanced customer service. To meet these needs, Hydro One conceptualized an end-to-end solution leveraging open standards and Internet Protocols (IP) at all communication levels. The utility drew upon industry leaders like Trilliant to realize this vision.