Technology Category
- Platform as a Service (PaaS) - Application Development Platforms
Applicable Industries
- Apparel
- Transportation
Use Cases
- Real-Time Location System (RTLS)
- Time Sensitive Networking
About The Customer
Estes Express Lines is a prominent transportation company that delivers countless shipments across the United States, Canada, Mexico, Puerto Rico, and the Caribbean. The company is heavily reliant on reliable, timely data to ensure on-time delivery of shipments every day. To streamline the integration between its core systems and improve operational efficiency, Estes leveraged the Denodo Platform to establish a logical data fabric. This enabled the company to seamlessly integrate data across disparate sources in real time, providing Estes leaders with real-time visibility of shipments to optimize customer experiences.
The Challenge
Estes Express Lines, a major transportation company operating across the United States, Canada, Mexico, Puerto Rico, and the Caribbean, was facing significant challenges due to the storage of data across numerous data silos. This led to a number of issues including the need for IT to physically move data before it could be put into production, spending time, money, and resources on redundant hardware and code, and handling data security separately by different teams. Furthermore, business users were dependent on IT to furnish their data requests, which negatively impacted the company's agility and efficiency.
The Solution
To overcome these challenges, Estes Express Lines leveraged the Denodo Platform to establish a logical data fabric. This platform, powered by data virtualization, created a single data-access layer above all of the company’s disparate sources. This not only integrated data across the company’s disparate sources in real time, but also provided timely, self-service access to all data. As a result, Estes was able to streamline operations, improve data security, and enhance the efficiency of its IT and business operations. Additionally, the company was able to deliver APIs in a matter of days, a process that previously took 4-6 weeks.
Operational Impact
Quantitative Benefit
Case Study missing?
Start adding your own!
Register with your work email and create a new case study profile for your business.
Related Case Studies.
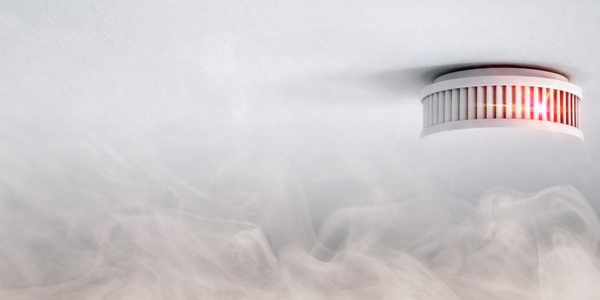
Case Study
Fire Alarm System and Remote Monitoring Sytem
Fire alarm systems are essential in providing an early warning in the event of fire. They help to save lives and protect property whilst also fulfilling the needs of insurance companies and government departments.Fire alarm systems typically consist of several inter-linked components, such as smoke detectors, heat detector, carbon monoxide, manual call points, sounders, alarm and buzzer. The fire alarm system should give immediate information in order to prevent the fire spread and protect live and property.To get maximum protection a shoe manufacturer in Indonesia opted for a new fire alarm system to monitor 13 production sites spread over 160 hectars. Although the company had an existing fire alarm system, it could not be monitored remotely.It was essential that the new system would be able to be monitored from a central control room. It needed to be able to connect to the existing smoke detector and manual call point. Information should be easily collected and passed on to the Supervisory Control and Data Acquisition (SCADA) system. Furthermore, the system should have several features such as alarm management, auto reporting, being connected to many client computers without additional cost, and run 24/7 without fails. The company also needed a system which could be implemented without changing the architecture of the existing fire alarm system.
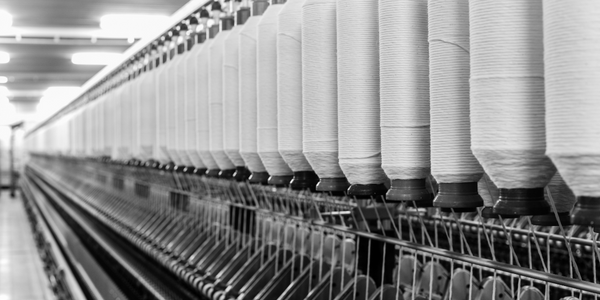
Case Study
IoT Applications and Upgrades in Textile Plant
At any given time, the textile company’s manufacturing facility has up to 2,000 textile carts in use. These carts are pushed from room to room, carrying materials or semi-finished products. Previously, a paper with a hand-written description was attached to each cart. This traditional method of processing made product tracking extremely difficult. Additionally, making sure that every cart of materials or semi-finished products went to its correct processing work station was also a problem. Therefore, the company desired an intelligent solution for tracking assets at their factories. They also wanted a solution that would help them collect process data so they could improve their manufacturing efficiency.
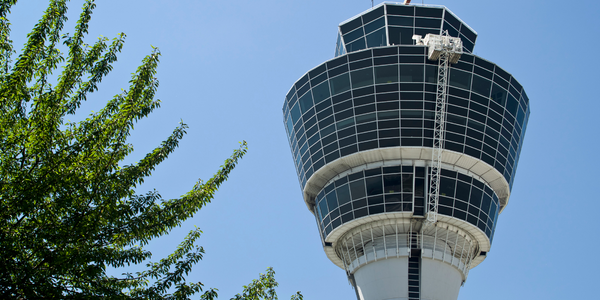
Case Study
Airport SCADA Systems Improve Service Levels
Modern airports are one of the busiest environments on Earth and rely on process automation equipment to ensure service operators achieve their KPIs. Increasingly airport SCADA systems are being used to control all aspects of the operation and associated facilities. This is because unplanned system downtime can cost dearly, both in terms of reduced revenues and the associated loss of customer satisfaction due to inevitable travel inconvenience and disruption.
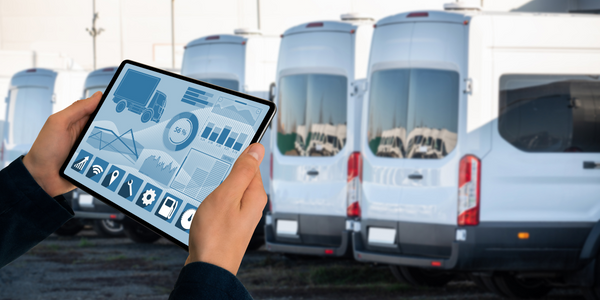
Case Study
IoT-based Fleet Intelligence Innovation
Speed to market is precious for DRVR, a rapidly growing start-up company. With a business model dependent on reliable mobile data, managers were spending their lives trying to negotiate data roaming deals with mobile network operators in different countries. And, even then, service quality was a constant concern.
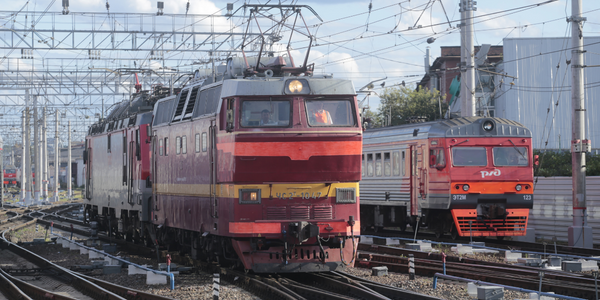
Case Study
Digitize Railway with Deutsche Bahn
To reduce maintenance costs and delay-causing failures for Deutsche Bahn. They need manual measurements by a position measurement system based on custom-made MEMS sensor clusters, which allow autonomous and continuous monitoring with wireless data transmission and long battery. They were looking for data pre-processing solution in the sensor and machine learning algorithms in the cloud so as to detect critical wear.
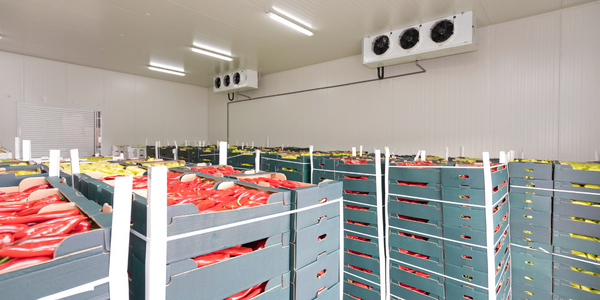
Case Study
Cold Chain Transportation and Refrigerated Fleet Management System
1) Create a digital connected transportation solution to retrofit cold chain trailers with real-time tracking and controls. 2) Prevent multi-million dollar losses due to theft or spoilage. 3) Deliver a digital chain-of-custody solution for door to door load monitoring and security. 4) Provide a trusted multi-fleet solution in a single application with granular data and access controls.