Technology Category
- Infrastructure as a Service (IaaS) - Cloud Computing
Applicable Industries
- Automotive
- Transportation
Applicable Functions
- Logistics & Transportation
- Procurement
Use Cases
- Driver Performance Monitoring
Services
- System Integration
- Training
About The Customer
RAAF Logistics is a logistics company based in Laredo, Texas, providing door-to-door service between Mexico and the US. The company specializes in the transportation of automotive freight, with 80% of its freight for that industry. RAAF Logistics was founded in July 2018 by three friends, each contributing their unique skills and resources to the business. One of the founders was a trucking businessman in Mexico, another's family were customs brokers in Mexico and the US, and the third, Rodolfo Boehringer, took on the role of general manager. The company started with 10 new trucks and 15 trailers and has since grown to 34 trucks, 62 drivers, and 125 trailers.
The Challenge
RAAF Logistics, a Texas-based company providing door-to-door service between Mexico and the US, faced significant operational challenges. The company, which started with 10 trucks and 15 trailers, quickly grew to 34 trucks, 62 drivers, and 125 trailers. This rapid expansion led to an increase in administrative tasks, particularly in managing orders and payroll. The company's general manager, Rodolfo Boehringer, was responsible for all the paperwork, including obtaining DOT permits and running the company. The company's growth also necessitated the need for a system to keep track of orders and invoices, as losing an invoice could result in financial losses. Additionally, the company was looking to establish an EDI connection with its customers to provide regular updates on their loads.
The Solution
RAAF Logistics turned to Axon Software to streamline its operations. The software provided a comprehensive solution for managing orders, invoices, and payroll. After a two-week training period, the company was able to fully utilize the software to keep track of all its orders and ensure no invoice was lost. The software also allowed the company to run reports, providing a comprehensive view of the business operations. Axon Software also offered the option of hosting the system on the company's server or their servers, which was beneficial for RAAF Logistics as it had staff in Mexico and maintaining multiple servers and connections would have been challenging. The company chose to host the system on Axon's servers, citing the cost difference as worth it to avoid server problems. Furthermore, Axon Software was instrumental in setting up an EDI connection with one of RAAF's customers, enabling the company to provide regular updates on their loads. The software also simplified the payroll process, allowing one person to handle the payroll of over 60 drivers.
Operational Impact
Quantitative Benefit
Case Study missing?
Start adding your own!
Register with your work email and create a new case study profile for your business.
Related Case Studies.
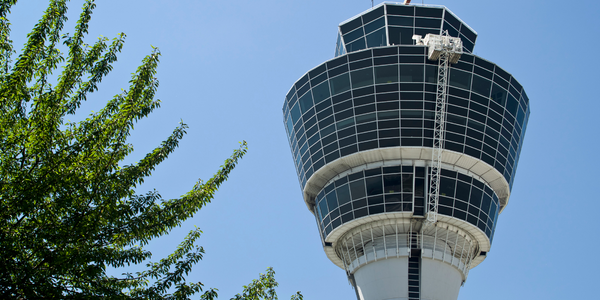
Case Study
Airport SCADA Systems Improve Service Levels
Modern airports are one of the busiest environments on Earth and rely on process automation equipment to ensure service operators achieve their KPIs. Increasingly airport SCADA systems are being used to control all aspects of the operation and associated facilities. This is because unplanned system downtime can cost dearly, both in terms of reduced revenues and the associated loss of customer satisfaction due to inevitable travel inconvenience and disruption.
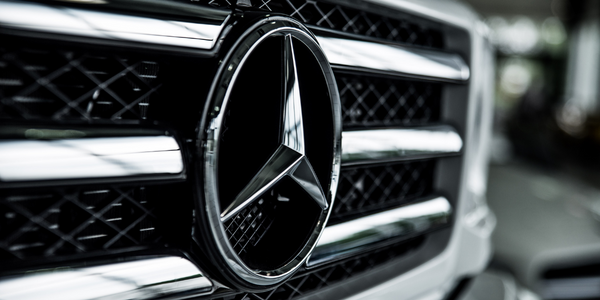
Case Study
Integral Plant Maintenance
Mercedes-Benz and his partner GAZ chose Siemens to be its maintenance partner at a new engine plant in Yaroslavl, Russia. The new plant offers a capacity to manufacture diesel engines for the Russian market, for locally produced Sprinter Classic. In addition to engines for the local market, the Yaroslavl plant will also produce spare parts. Mercedes-Benz Russia and his partner needed a service partner in order to ensure the operation of these lines in a maintenance partnership arrangement. The challenges included coordinating the entire maintenance management operation, in particular inspections, corrective and predictive maintenance activities, and the optimizing spare parts management. Siemens developed a customized maintenance solution that includes all electronic and mechanical maintenance activities (Integral Plant Maintenance).
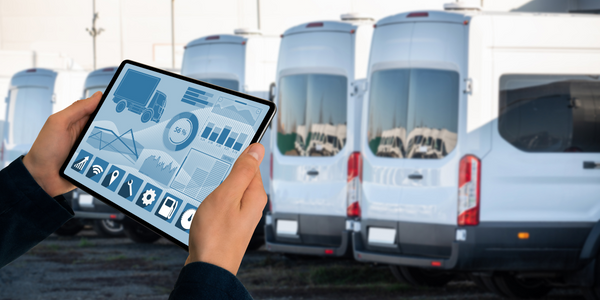
Case Study
IoT-based Fleet Intelligence Innovation
Speed to market is precious for DRVR, a rapidly growing start-up company. With a business model dependent on reliable mobile data, managers were spending their lives trying to negotiate data roaming deals with mobile network operators in different countries. And, even then, service quality was a constant concern.
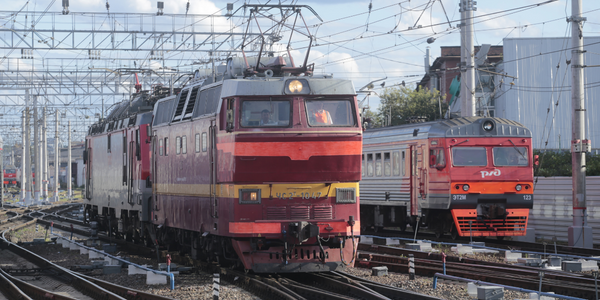
Case Study
Digitize Railway with Deutsche Bahn
To reduce maintenance costs and delay-causing failures for Deutsche Bahn. They need manual measurements by a position measurement system based on custom-made MEMS sensor clusters, which allow autonomous and continuous monitoring with wireless data transmission and long battery. They were looking for data pre-processing solution in the sensor and machine learning algorithms in the cloud so as to detect critical wear.
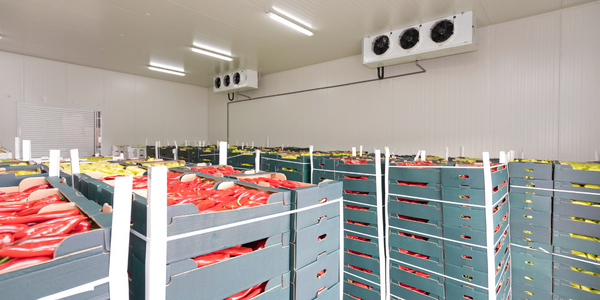
Case Study
Cold Chain Transportation and Refrigerated Fleet Management System
1) Create a digital connected transportation solution to retrofit cold chain trailers with real-time tracking and controls. 2) Prevent multi-million dollar losses due to theft or spoilage. 3) Deliver a digital chain-of-custody solution for door to door load monitoring and security. 4) Provide a trusted multi-fleet solution in a single application with granular data and access controls.