Streamlining Operations with End-to-End Supply Chain Optimization in Pharmaceutical Industry: A Case Study of Nomeco
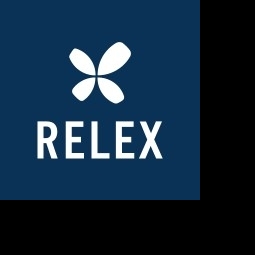
Technology Category
- Cybersecurity & Privacy - Identity & Authentication Management
- Functional Applications - Inventory Management Systems
Applicable Industries
- Pharmaceuticals
- Transportation
Applicable Functions
- Logistics & Transportation
- Warehouse & Inventory Management
Use Cases
- Inventory Management
- Picking, Sorting & Positioning
Services
- System Integration
About The Customer
Nomeco is the preferred pharmaceutical wholesaler for pharmacies, supplier for hospitals, and strategic service partner for the pharmaceutical industry in Denmark. They provide vendor managed inventory services (VMI) for approximately 350 pharmacies across Denmark and the Faero Islands through three distribution centers. With a turnover of EUR 1 billion (USD 1.07 billion), they manage over 22,000 SKUs. Nomeco’s pharmacy customers have considerable autonomy in deciding assortments, delivery schedules, delivery sizes, and other parameters in order to optimize the operations of each individual pharmacy.
The Challenge
Nomeco, a leading pharmaceutical wholesaler in Denmark, was facing challenges with its legacy replenishment and ERP systems which had become difficult to maintain and develop. The planning tools were unable to integrate with each other, leading to unnecessary manual steps throughout their process. This was particularly problematic every two weeks when prescription drug prices and pharmacy assortments needed to be updated across their network of pharmacies. Furthermore, Nomeco’s pharmacy customers have considerable autonomy in deciding assortments, delivery schedules, delivery sizes, and other parameters. This made forecasting demand and ensuring optimal inventory levels for pharmaceuticals immensely complex and time-consuming. Additionally, the unstable supply chains and frequent supplier stock-outs of prescription medications required providers to identify appropriate pharmaceutical substitutions to meet their customer demand. Nomeco’s systems were not able to support optimally in these situations, which required their planners to manually identify the ideal replacements for these medications.
The Solution
After an extensive vendor selection process, Nomeco decided to implement RELEX, a platform that provides end-to-end supply chain integration and optimizes their forecasting and replenishment processes. The implementation of the RELEX solution was heavily impacted by the COVID-19 pandemic as Nomeco had to focus their attention on business-critical activities and manage the build-up of national reserve stock during the height of the pandemic. However, since implementation, they have been able to significantly reduce manual processes, which also reduced the amount of time—and weekend overtime—spent on VMI-related tasks. Through RELEX’s advanced assortment logic, their pharmacy substitution processes are optimized to make fast, data-driven replacement decisions in the event of vendor stock-outs.
Operational Impact
Quantitative Benefit
Case Study missing?
Start adding your own!
Register with your work email and create a new case study profile for your business.
Related Case Studies.
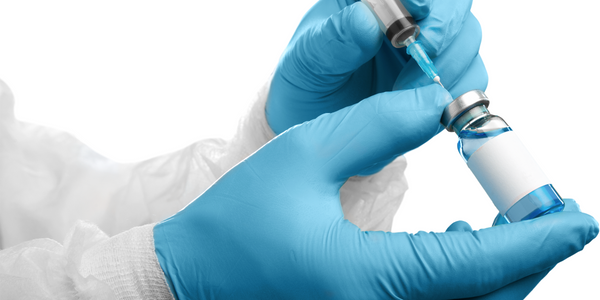
Case Study
Case Study: Pfizer
Pfizer’s high-performance computing software and systems for worldwide research and development support large-scale data analysis, research projects, clinical analytics, and modeling. Pfizer’s computing services are used across the spectrum of research and development efforts, from the deep biological understanding of disease to the design of safe, efficacious therapeutic agents.
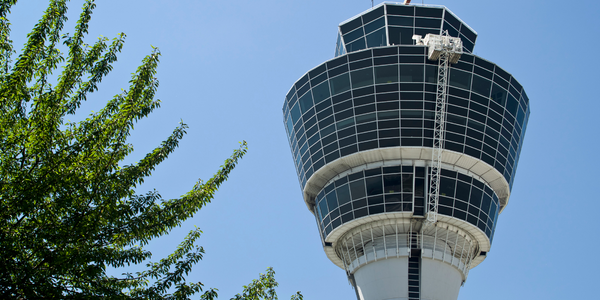
Case Study
Airport SCADA Systems Improve Service Levels
Modern airports are one of the busiest environments on Earth and rely on process automation equipment to ensure service operators achieve their KPIs. Increasingly airport SCADA systems are being used to control all aspects of the operation and associated facilities. This is because unplanned system downtime can cost dearly, both in terms of reduced revenues and the associated loss of customer satisfaction due to inevitable travel inconvenience and disruption.
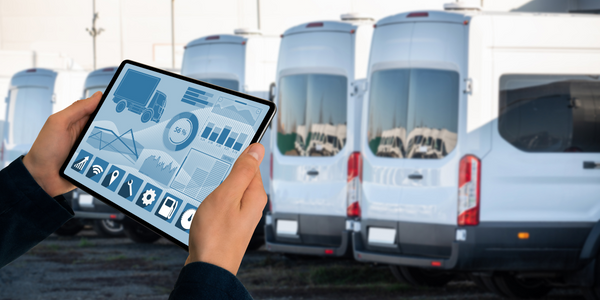
Case Study
IoT-based Fleet Intelligence Innovation
Speed to market is precious for DRVR, a rapidly growing start-up company. With a business model dependent on reliable mobile data, managers were spending their lives trying to negotiate data roaming deals with mobile network operators in different countries. And, even then, service quality was a constant concern.
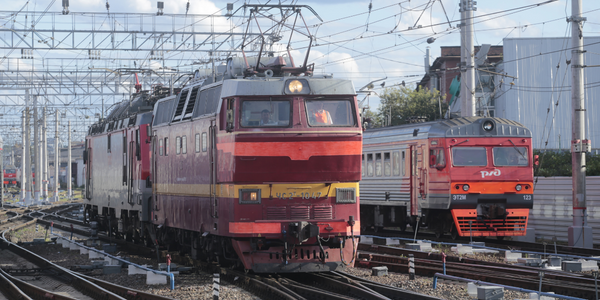
Case Study
Digitize Railway with Deutsche Bahn
To reduce maintenance costs and delay-causing failures for Deutsche Bahn. They need manual measurements by a position measurement system based on custom-made MEMS sensor clusters, which allow autonomous and continuous monitoring with wireless data transmission and long battery. They were looking for data pre-processing solution in the sensor and machine learning algorithms in the cloud so as to detect critical wear.
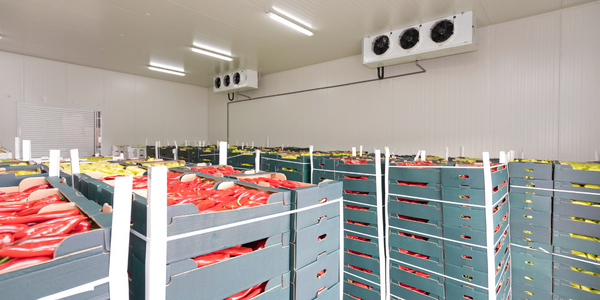
Case Study
Cold Chain Transportation and Refrigerated Fleet Management System
1) Create a digital connected transportation solution to retrofit cold chain trailers with real-time tracking and controls. 2) Prevent multi-million dollar losses due to theft or spoilage. 3) Deliver a digital chain-of-custody solution for door to door load monitoring and security. 4) Provide a trusted multi-fleet solution in a single application with granular data and access controls.
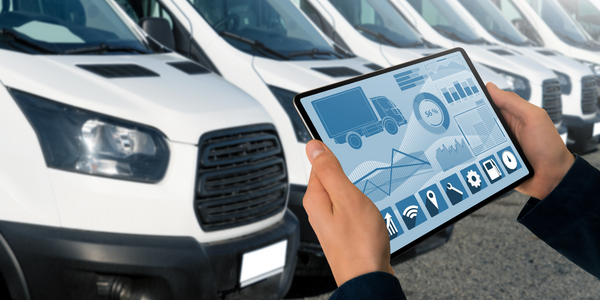
Case Study
Vehicle Fleet Analytics
Organizations frequently implement a maintenance strategy for their fleets of vehicles using a combination of time and usage based maintenance schedules. While effective as a whole, time and usage based schedules do not take into account driving patterns, environmental factors, and sensors currently deployed within the vehicle measuring crank voltage, ignition voltage, and acceleration, all of which have a significant influence on the overall health of the vehicle.In a typical fleet, a large percentage of road calls are related to electrical failure, with battery failure being a common cause. Battery failures result in unmet service agreement levels and costly re-adjustment of scheduled to provide replacement vehicles. To reduce the impact of unplanned maintenance, the transportation logistics company was interested in a trial of C3 Vehicle Fleet Analytics.