SYSPRO Case Study: Green-Tek
Customer Company Size
SME
Region
- America
Country
- United States
Product
- SYSPRO ERP
- SYSPRO Material Yield System
- Great Plains Dynamics
- MAX ERP
Tech Stack
- ERP
- CRM
- ODBC
- MRP
Implementation Scale
- Enterprise-wide Deployment
Impact Metrics
- Cost Savings
- Customer Satisfaction
- Productivity Improvements
- Waste Reduction
- Environmental Impact Reduction
Technology Category
- Functional Applications - Enterprise Resource Planning Systems (ERP)
- Functional Applications - Inventory Management Systems
- Functional Applications - Computerized Maintenance Management Systems (CMMS)
- Functional Applications - Product Data Management Systems
Applicable Industries
- Packaging
- Construction & Infrastructure
Applicable Functions
- Business Operation
- Sales & Marketing
Use Cases
- Inventory Management
- Process Control & Optimization
Services
- System Integration
- Software Design & Engineering Services
About The Customer
Green-Tek, Inc., based in Edgerton, WI, is a privately-owned company specializing in the conversion, fabrication, and distribution of packaging materials, greenhouse coverings, thermal glazing, and materials handling products. The company benefits from its central US location, which provides access to a skilled labor force and efficient shipping lanes across North America. Green-Tek's product offerings include polycarbonate multi-wall and corrugated sheeting, shade cloth, and poly films with UV protection capabilities. These products are cut to order based on customer specifications, serving a diverse customer base that includes distributors and greenhouse growers. The company is led by President and co-owner Paul Jacobson, who is actively involved in sales alongside in-house sales representatives and a vice president of sales. Green-Tek is committed to customer service, with a full-time trouble shooter dedicated to tracking orders and ensuring on-time deliveries.
The Challenge
Green-Tek faced several challenges with their existing ERP software, including cumbersome sales procedures, lost sales history, stagnant inventory, limited visibility into processes, and wasted scrap materials. The company had been using a combination of MAX ERP software and Great Plains Dynamics since 2000, but these systems were unyielding and failed to maintain order histories. This required re-orders to be treated as new orders, leading to inefficiencies and increased scrap. A re-implementation of the MAX software in 2002 did not produce the desired results, prompting Green-Tek to search for a new solution.
The Solution
After an intensive search for a new ERP solution, Green-Tek selected SYSPRO ERP due to its extensive inventory capabilities, particularly the SYSPRO Material Yield System. This system is designed to reclaim remnants from larger cuts and return them to inventory, allowing customer-specific dimensional requirements to be matched against existing inventory. The SYSPRO Material Yield System was initially developed for Tri Star Plastics, which faced a similar remnant problem. The system's ability to maximize the use of remnants significantly reduces the amount of scrap relegated to landfills, providing both economic and environmental benefits. Green-Tek implemented the SYSPRO software, including the Material Yield System, on January 1, 2004. The software is now utilized by 34 concurrent users who leverage SYSPRO's accounting, MRP, customer relationship management, and ODBC solutions to enhance operational efficiencies. The Material Yield System performs automatic yield calculations, enabling faster order turnaround and efficient remnant management.
Operational Impact
Quantitative Benefit
Case Study missing?
Start adding your own!
Register with your work email and create a new case study profile for your business.
Related Case Studies.
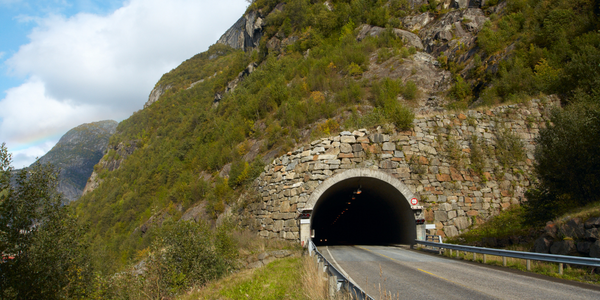
Case Study
IoT System for Tunnel Construction
The Zenitaka Corporation ('Zenitaka') has two major business areas: its architectural business focuses on structures such as government buildings, office buildings, and commercial facilities, while its civil engineering business is targeted at structures such as tunnels, bridges and dams. Within these areas, there presented two issues that have always persisted in regard to the construction of mountain tunnels. These issues are 'improving safety" and "reducing energy consumption". Mountain tunnels construction requires a massive amount of electricity. This is because there are many kinds of electrical equipment being used day and night, including construction machinery, construction lighting, and ventilating fan. Despite this, the amount of power consumption is generally not tightly managed. In many cases, the exact amount of power consumption is only ascertained when the bill from the power company becomes available. Sometimes, corporations install demand-monitoring equipment to help curb the maximum power demanded. However, even in these cases, the devices only allow the total volume of power consumption to be ascertained, or they may issue warnings to prevent the contracted volume of power from being exceeded. In order to tackle the issue of reducing power consumption, it was first necessary to obtain an accurate breakdown of how much power was being used in each particular area. In other words, we needed to be able to visualize the amount of power being consumed. Safety, was also not being managed very rigorously. Even now, tunnel construction sites often use a 'name label' system for managing entry into the work site. Specifically, red labels with white reverse sides that bear the workers' names on both sides are displayed at the tunnel work site entrance. The workers themselves then flip the name label to the appropriate side when entering or exiting from the work site to indicate whether or not they are working inside the tunnel at any given time. If a worker forgets to flip his or her name label when entering or exiting from the tunnel, management cannot be performed effectively. In order to tackle the challenges mentioned above, Zenitaka decided to build a system that could improve the safety of tunnel construction as well as reduce the amount of power consumed. In other words, this new system would facilitate a clear picture of which workers were working in each location at the mountain tunnel construction site, as well as which processes were being carried out at those respective locations at any given time. The system would maintain the safety of all workers while also carefully controlling the electrical equipment to reduce unnecessary power consumption. Having decided on the concept, our next concern was whether there existed any kind of robust hardware that would not break down at the construction work site, that could move freely in response to changes in the working environment, and that could accurately detect workers and vehicles using radio frequency identification (RFID). Given that this system would involve many components that were new to Zenitaka, we decided to enlist the cooperation of E.I.Sol Co., Ltd. ('E.I.Sol') as our joint development partner, as they had provided us with a highly practical proposal.
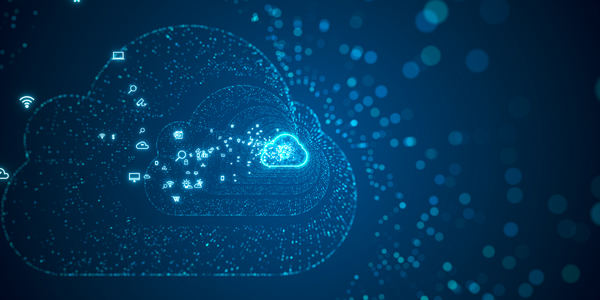
Case Study
Splunk Partnership Ties Together Big Data & IoT Services
Splunk was faced with the need to meet emerging customer demands for interfacing IoT projects to its suite of services. The company required an IoT partner that would be able to easily and quickly integrate with its Splunk Enterprise platform, rather than allocating development resources and time to building out an IoT interface and application platform.
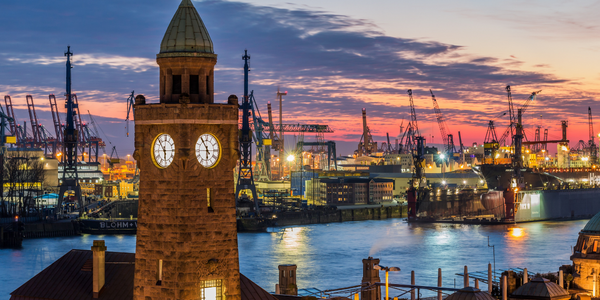
Case Study
Bridge monitoring in Hamburg Port
Kattwyk Bridge is used for both rail and road transport, and it has played an important role in the Port of Hamburg since 1973. However, the increasing pressure from traffic requires a monitoring solution. The goal of the project is to assess in real-time the bridge's status and dynamic responses to traffic and lift processes.
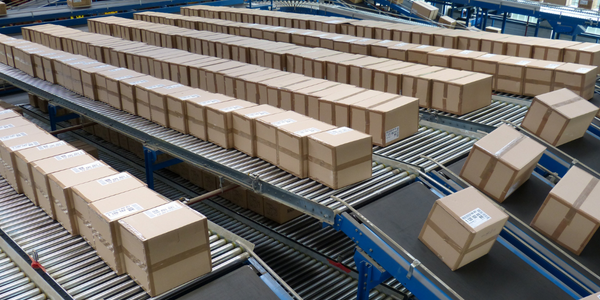
Case Study
IoT Data Analytics Case Study - Packaging Films Manufacturer
The company manufactures packaging films on made to order or configure to order basis. Every order has a different set of requirements from the product characteristics perspective and hence requires machine’s settings to be adjusted accordingly. If the film quality does not meet the required standards, the degraded quality impacts customer delivery causes customer dissatisfaction and results in lower margins. The biggest challenge was to identify the real root cause and devise a remedy for that.
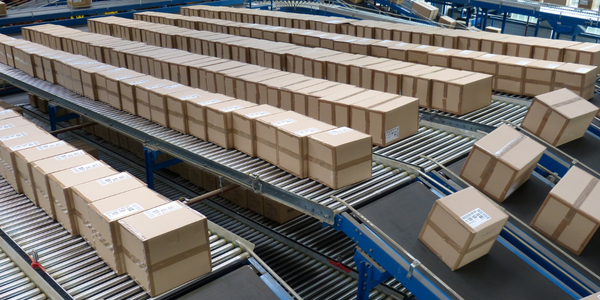
Case Study
Zenon the Ideal Basis for An Ergonomic HMI
KHS develops and produces machines and equipment for filling and packaging in the drinks industry. Because drinks manufacturing, filling and packaging consist of a number of highly complex processes, the user-friendly and intuitive operation of equipment is increasingly gaining in significance. In order to design these processes as simple as possible for the user, KHS decided to introduce a uniform, transparent and standardized solution to the company. The HMI interface should meet the requirement for people with different qualifications and enable them to work on a standard platform.
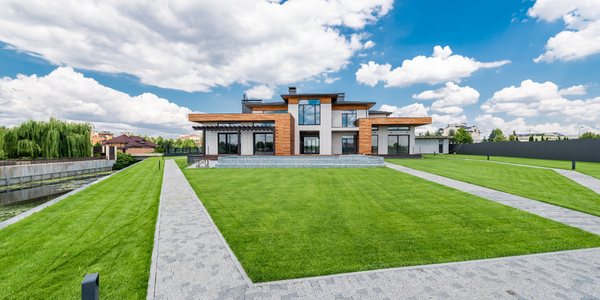
Case Study
Bellas Landscaping
Leading landscaping firm serving central Illinois streamlines operations with Samsara’s real-time fleet tracking solution: • 30+ vehicle fleet includes International Terrastar dump trucks and flatbeds, medium- and light-duty pickups from Ford and Chevrolet. Winter fleet includes of snow plows and salters.