Customer Company Size
Startup
Region
- Europe
Country
- Germany
Product
- Google Cloud
- BigQuery
- Google Kubernetes Engine (GKE)
- Compute Engine
Tech Stack
- Google Cloud
- BigQuery
- Google Kubernetes Engine (GKE)
- Compute Engine
Implementation Scale
- Enterprise-wide Deployment
Impact Metrics
- Productivity Improvements
- Digital Expertise
- Environmental Impact Reduction
Technology Category
- Analytics & Modeling - Predictive Analytics
- Platform as a Service (PaaS) - Data Management Platforms
- Infrastructure as a Service (IaaS) - Cloud Computing
Applicable Functions
- Business Operation
Use Cases
- Building Energy Management
- Remote Asset Management
Services
- Cloud Planning, Design & Implementation Services
- Software Design & Engineering Services
- System Integration
About The Customer
Syte is a German property tech startup that is revolutionizing the real estate industry with its AI-driven platform. The company provides real-time access to relevant property data, enabling real estate developers, investors, and architects to quickly assess the building potential of properties. Syte's platform helps optimize energy consumption and facilitates the re-densification of existing buildings to create additional housing space. Founded by David Nellessen and Matthias Zühlke, Syte aims to address the housing shortage in Germany by streamlining the process of property development and expansion. The company leverages advanced technologies, including Google Cloud tools, to enhance its data processing capabilities and improve the efficiency of real estate development.
The Challenge
Germany is facing a significant housing shortage, with a deficit of 700,000 homes. The cost of building materials is rising, rents are increasing, and incomes are being squeezed by the cost of living. Re-densification, which involves redeveloping and adding stories to existing buildings, is seen as a potential solution. However, this process is complex and requires navigating numerous logistical challenges, such as building law compliance. Traditional methods for identifying suitable sites for re-densification are time-consuming, often taking several days or weeks.
The Solution
Syte utilizes Google Cloud tools to enhance its AI-driven property platform, enabling real-time retrieval of property data. The platform allows users to search a database of 25 million properties using multiple filter parameters, significantly reducing the time required to identify sites for re-densification. By deploying BigQuery, Syte improved its search engine's scalability and responsiveness, reducing response times from 60 seconds to a maximum of two seconds. Additionally, Syte employs Google Kubernetes Engine (GKE) for training machine learning models, running data pipelines, and hosting web services. This setup has led to a 40% improvement in productivity by simplifying the deployment and management of applications. Compute Engine supports Syte's data processing needs, allowing the company to process massive amounts of LiDAR data efficiently. The integration of these technologies enables Syte to offer new features to larger target groups with minimal technical effort, focusing on reducing the carbon impact of the building sector.
Operational Impact
Quantitative Benefit
Case Study missing?
Start adding your own!
Register with your work email and create a new case study profile for your business.
Related Case Studies.
.png)
Case Study
Improving Vending Machine Profitability with the Internet of Things (IoT)
The vending industry is undergoing a sea change, taking advantage of new technologies to go beyond just delivering snacks to creating a new retail location. Intelligent vending machines can be found in many public locations as well as company facilities, selling different types of goods and services, including even computer accessories, gold bars, tickets, and office supplies. With increasing sophistication, they may also provide time- and location-based data pertaining to sales, inventory, and customer preferences. But at the end of the day, vending machine operators know greater profitability is driven by higher sales and lower operating costs.
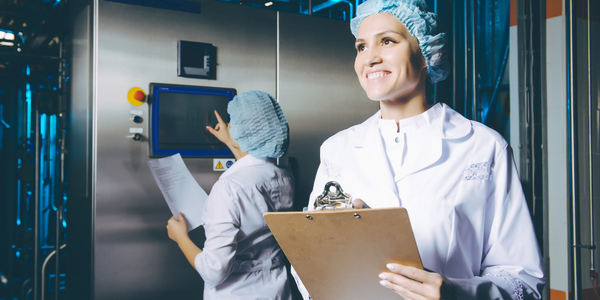
Case Study
Remote Wellhead Monitoring
Each wellhead was equipped with various sensors and meters that needed to be monitored and controlled from a central HMI, often miles away from the assets in the field. Redundant solar and wind generators were installed at each wellhead to support the electrical needs of the pumpstations, temperature meters, cameras, and cellular modules. In addition to asset management and remote control capabilities, data logging for remote surveillance and alarm notifications was a key demand from the customer. Terra Ferma’s solution needed to be power efficient, reliable, and capable of supporting high-bandwidth data-feeds. They needed a multi-link cellular connection to a central server that sustained reliable and redundant monitoring and control of flow meters, temperature sensors, power supply, and event-logging; including video and image files. This open-standard network needed to interface with the existing SCADA and proprietary network management software.
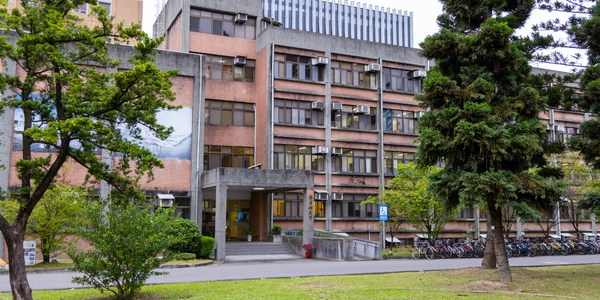
Case Study
Energy Saving & Power Monitoring System
Recently a university in Taiwan was experiencing dramatic power usage increases due to its growing number of campus buildings and students. Aiming to analyze their power consumption and increase their power efficiency across 52 buildings, the university wanted to build a power management system utilizing web-based hardware and software. With these goals in mind, they contacted Advantech to help them develop their system and provide them with the means to save energy in the years to come.
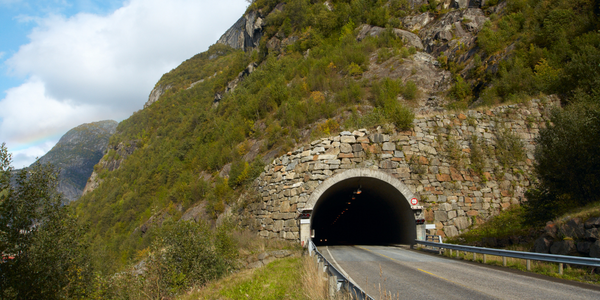
Case Study
IoT System for Tunnel Construction
The Zenitaka Corporation ('Zenitaka') has two major business areas: its architectural business focuses on structures such as government buildings, office buildings, and commercial facilities, while its civil engineering business is targeted at structures such as tunnels, bridges and dams. Within these areas, there presented two issues that have always persisted in regard to the construction of mountain tunnels. These issues are 'improving safety" and "reducing energy consumption". Mountain tunnels construction requires a massive amount of electricity. This is because there are many kinds of electrical equipment being used day and night, including construction machinery, construction lighting, and ventilating fan. Despite this, the amount of power consumption is generally not tightly managed. In many cases, the exact amount of power consumption is only ascertained when the bill from the power company becomes available. Sometimes, corporations install demand-monitoring equipment to help curb the maximum power demanded. However, even in these cases, the devices only allow the total volume of power consumption to be ascertained, or they may issue warnings to prevent the contracted volume of power from being exceeded. In order to tackle the issue of reducing power consumption, it was first necessary to obtain an accurate breakdown of how much power was being used in each particular area. In other words, we needed to be able to visualize the amount of power being consumed. Safety, was also not being managed very rigorously. Even now, tunnel construction sites often use a 'name label' system for managing entry into the work site. Specifically, red labels with white reverse sides that bear the workers' names on both sides are displayed at the tunnel work site entrance. The workers themselves then flip the name label to the appropriate side when entering or exiting from the work site to indicate whether or not they are working inside the tunnel at any given time. If a worker forgets to flip his or her name label when entering or exiting from the tunnel, management cannot be performed effectively. In order to tackle the challenges mentioned above, Zenitaka decided to build a system that could improve the safety of tunnel construction as well as reduce the amount of power consumed. In other words, this new system would facilitate a clear picture of which workers were working in each location at the mountain tunnel construction site, as well as which processes were being carried out at those respective locations at any given time. The system would maintain the safety of all workers while also carefully controlling the electrical equipment to reduce unnecessary power consumption. Having decided on the concept, our next concern was whether there existed any kind of robust hardware that would not break down at the construction work site, that could move freely in response to changes in the working environment, and that could accurately detect workers and vehicles using radio frequency identification (RFID). Given that this system would involve many components that were new to Zenitaka, we decided to enlist the cooperation of E.I.Sol Co., Ltd. ('E.I.Sol') as our joint development partner, as they had provided us with a highly practical proposal.