Customer Company Size
Large Corporate
Region
- America
Country
- Canada
Product
- Vocollect VoiceDirect Enterprise Connector
- Vocollect SR-20 Wired Headsets
- Vocollect SRX Wireless Headsets
- Vocollect T5 Mobile Devices
- Vocollect VoiceClient and VoiceConsole Software
Tech Stack
- Voice Technology
- Warehouse Management System (WMS)
- RF Scanning
Implementation Scale
- Enterprise-wide Deployment
Impact Metrics
- Cost Savings
- Customer Satisfaction
- Productivity Improvements
Technology Category
- Functional Applications - Remote Monitoring & Control Systems
- Functional Applications - Warehouse Management Systems (WMS)
Applicable Industries
- Consumer Goods
- Retail
Applicable Functions
- Logistics & Transportation
- Warehouse & Inventory Management
Use Cases
- Inventory Management
- Predictive Maintenance
- Warehouse Automation
Services
- System Integration
- Training
About The Customer
Sony of Canada, Ltd., established in 1955 and headquartered in Metropolitan Toronto, is a wholly owned subsidiary of Sony Corporation, one of the largest entertainment companies in the world. Sony's portfolio includes electronics, music, movies, games, and online businesses. The company processes approximately 18,000 orders per month and is responsible for inventory and demand planning, sales order management, transportation operations, and logistics operations. With a workforce of around 1,000 employees, Sony of Canada operates two distribution centers in Whitby, Ontario, and Coquitlam, British Columbia, housing approximately 2,200 SKUs and operating five days a week.
The Challenge
Sony of Canada faced challenges with their paper-based and RF systems for distribution. The paper system was cumbersome and lacked a locator system, making it difficult for employees to find products quickly. RF scanning, while faster than paper, involved too many steps and errors. Employees had to input data into handheld units, view screens, and the system was often slow to respond. The rapidly changing business model, with increasing online orders and more, smaller orders, exposed these weaknesses further. The company needed a more efficient system to handle high seasonality, support changing business models, and maintain a highly satisfied customer base.
The Solution
Sony of Canada, on the recommendation of their WMS provider RedPrairie, decided to integrate Honeywell Vocollect voice technology into their operations. They observed the technology in action at another Honeywell customer site and saw its potential for process improvements. The integration of Vocollect voice into their WMS upgrade allowed for significant efficiency gains. Initially, Vocollect voice was piloted for cluster-picking for parcel shipments due to its process fit and high number of picks. The training process was simple and short, taking as little as one hour. The technology was later expanded to the cycle counting workflow. The voice solution enabled accurate and quick order fulfillment, better management of seasonal volume hikes, and support for the company's growing e-commerce business. The consolidated picking methodology, cluster-picking, was used for processing less than master carton quantities, enhancing timeliness in supporting e-commerce.
Operational Impact
Quantitative Benefit
Case Study missing?
Start adding your own!
Register with your work email and create a new case study profile for your business.
Related Case Studies.
.png)
Case Study
Improving Vending Machine Profitability with the Internet of Things (IoT)
The vending industry is undergoing a sea change, taking advantage of new technologies to go beyond just delivering snacks to creating a new retail location. Intelligent vending machines can be found in many public locations as well as company facilities, selling different types of goods and services, including even computer accessories, gold bars, tickets, and office supplies. With increasing sophistication, they may also provide time- and location-based data pertaining to sales, inventory, and customer preferences. But at the end of the day, vending machine operators know greater profitability is driven by higher sales and lower operating costs.
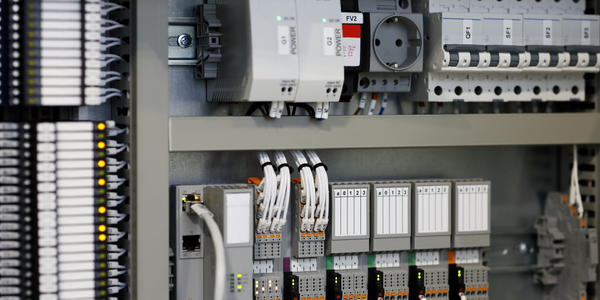
Case Study
Improving Production Line Efficiency with Ethernet Micro RTU Controller
Moxa was asked to provide a connectivity solution for one of the world's leading cosmetics companies. This multinational corporation, with retail presence in 130 countries, 23 global braches, and over 66,000 employees, sought to improve the efficiency of their production process by migrating from manual monitoring to an automatic productivity monitoring system. The production line was being monitored by ABB Real-TPI, a factory information system that offers data collection and analysis to improve plant efficiency. Due to software limitations, the customer needed an OPC server and a corresponding I/O solution to collect data from additional sensor devices for the Real-TPI system. The goal is to enable the factory information system to more thoroughly collect data from every corner of the production line. This will improve its ability to measure Overall Equipment Effectiveness (OEE) and translate into increased production efficiencies. System Requirements • Instant status updates while still consuming minimal bandwidth to relieve strain on limited factory networks • Interoperable with ABB Real-TPI • Small form factor appropriate for deployment where space is scarce • Remote software management and configuration to simplify operations
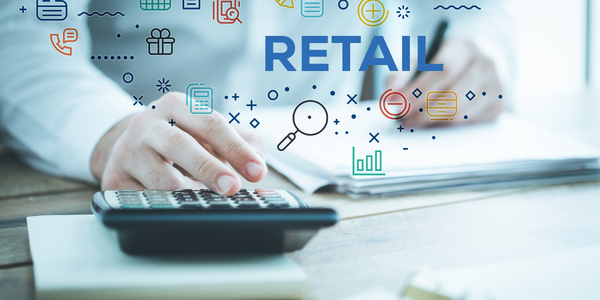
Case Study
Digital Retail Security Solutions
Sennco wanted to help its retail customers increase sales and profits by developing an innovative alarm system as opposed to conventional connected alarms that are permanently tethered to display products. These traditional security systems were cumbersome and intrusive to the customer shopping experience. Additionally, they provided no useful data or analytics.
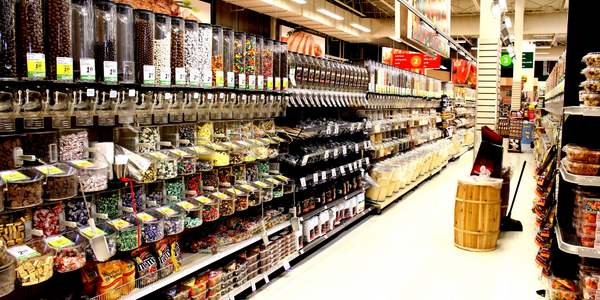
Case Study
How Sirqul’s IoT Platform is Crafting Carrefour’s New In-Store Experiences
Carrefour Taiwan’s goal is to be completely digital by end of 2018. Out-dated manual methods for analysis and assumptions limited Carrefour’s ability to change the customer experience and were void of real-time decision-making capabilities. Rather than relying solely on sales data, assumptions, and disparate systems, Carrefour Taiwan’s CEO led an initiative to find a connected IoT solution that could give the team the ability to make real-time changes and more informed decisions. Prior to implementing, Carrefour struggled to address their conversion rates and did not have the proper insights into the customer decision-making process nor how to make an immediate impact without losing customer confidence.