Customer Company Size
Large Corporate
Region
- America
Country
- United States
Product
- nGeniusONE Service Assurance Platform
- InfiniStream Appliances
- Packet Flow Switches
Tech Stack
- Cisco ACI-based software-defined data center
- MPLS and WAN connections
Implementation Scale
- Enterprise-wide Deployment
Impact Metrics
- Cost Savings
- Productivity Improvements
Technology Category
- Infrastructure as a Service (IaaS) - Cloud Computing
Applicable Industries
- Automotive
Applicable Functions
- Discrete Manufacturing
- Product Research & Development
Use Cases
- Manufacturing System Automation
- Remote Asset Management
Services
- Cloud Planning, Design & Implementation Services
- System Integration
About The Customer
The customer is the U.S. division of a global auto manufacturer that sells cars, trucks, SUVs and light commercial vehicles worldwide under multiple brand names. In order to take advantage of today’s digital transformation, the company is consolidating data centers in a push to ensure its IT infrastructure can support the objective of building, selling, and servicing vehicles from anywhere in the world. The company's CIO has a vision of being able to design, build, sell, and service the company’s vehicles from any place around in the globe, and the IT team embarked on a data center consolidation effort with the goal of lowering risk and decreasing time-to-market with Cloud and application deployments.
The Challenge
The U.S. division of a global auto manufacturer embarked on a data center consolidation effort with the goal of lowering risk and decreasing time-to-market with Cloud and application deployments. They needed to deploy new application services faster, reducing the rollout of new services from four months down to one day. Another major challenge was to assure performance of the design and build application services across a distributed infrastructure where all production facilities had to connect back to the data center. Failure to connect to the MPLS or WAN, and to the critical design and build applications, can stop the production line, disrupt the manufacturing cycle, and impact bottom-line revenue. IT was under tremendous pressure to manage the implementation of a Cisco ACI-based software-defined data center, as well as put in place a single solution to monitor their plant and office automation tools. A further challenge was the need to monitor manufacturing plants without installing agents on the production network.
The Solution
To meet the digital transformation needs of the company, the architects and managers in the new data centers turned to NETSCOUT®. The nGeniusONE Service Assurance platform with Adaptive Service Intelligence™ (ASI) technology, along with InfiniStream appliances and Packet Flow Switches allow the IT team responsible for the data center and infrastructure to identify, isolate and mitigate issues quickly. The nGenius Packet Flow Switches were used to feed network traffic to InfiniStream appliances which provide comprehensive analysis across the enterprise environment. The nGeniusONE platform enables IT to manage the company’s remote plants from a central location. Passive, agent-less architecture gathers information from plants and feeds this back to the centralized management. As the company retools additional manufacturing plants, the data center IT team is leveraging NETSCOUT solutions to monitor, analyze and resolve issues related to their MPLS and WAN connections between the data center and plants, as well as with their plant floor control systems, plant automation and office automation services.
Operational Impact
Quantitative Benefit
Case Study missing?
Start adding your own!
Register with your work email and create a new case study profile for your business.
Related Case Studies.
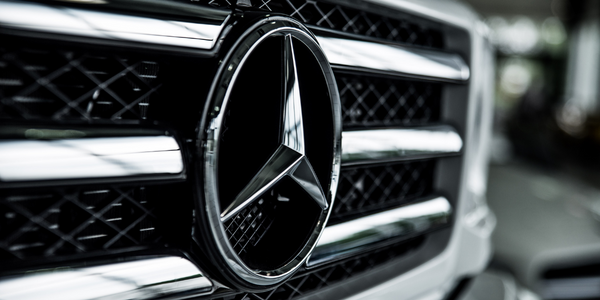
Case Study
Integral Plant Maintenance
Mercedes-Benz and his partner GAZ chose Siemens to be its maintenance partner at a new engine plant in Yaroslavl, Russia. The new plant offers a capacity to manufacture diesel engines for the Russian market, for locally produced Sprinter Classic. In addition to engines for the local market, the Yaroslavl plant will also produce spare parts. Mercedes-Benz Russia and his partner needed a service partner in order to ensure the operation of these lines in a maintenance partnership arrangement. The challenges included coordinating the entire maintenance management operation, in particular inspections, corrective and predictive maintenance activities, and the optimizing spare parts management. Siemens developed a customized maintenance solution that includes all electronic and mechanical maintenance activities (Integral Plant Maintenance).
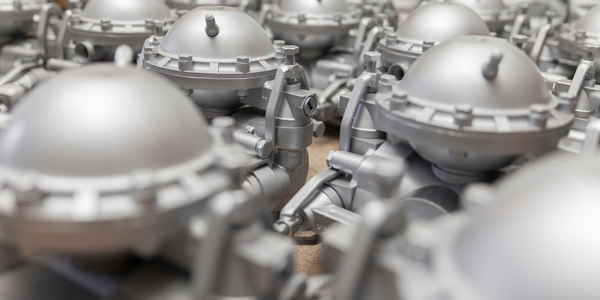
Case Study
Monitoring of Pressure Pumps in Automotive Industry
A large German/American producer of auto parts uses high-pressure pumps to deburr machined parts as a part of its production and quality check process. They decided to monitor these pumps to make sure they work properly and that they can see any indications leading to a potential failure before it affects their process.