Technology Category
- Cybersecurity & Privacy - Security Compliance
- Sensors - Environmental Sensors
Applicable Industries
- Automotive
- Education
Applicable Functions
- Human Resources
- Maintenance
Use Cases
- Indoor Air Quality Monitoring
- Outdoor Environmental Monitoring
Services
- System Integration
- Training
About The Customer
Toyota Spain is a branch of Toyota, a world leader in hybrid cars thanks to its Hybrid Synergy Drive ® technology. The company's main priorities are superior quality and client satisfaction. Toyota Spain markets 13 different models, with over 60 versions including an array of sedans, minivans and four wheel drives, using petrol, diesel and Hybrid Synergy Drive (HSD) engines. The company has a network of 80 dealers, with more than 58,500 vehicles sold in Spain during 2016. Toyota Spain promotes the ISO 14001 Environmental Management Standard throughout their dealer’s network in Spain relying on the GEA-TOYOTA application, developed with the AuraQuantic BPM Suite.
The Challenge
Toyota Spain, as part of its environmental commitment, aimed to implement the ISO 14001 Environmental Management System across its entire Official Dealer Network. This system had already been adopted by over 80% of Toyota dealers in Spain, with the goal of achieving 100% certification. The main challenges faced by Toyota Spain included the implementation of an effective management system that ensured compliance with current legislation, minimizing environmental impact, and optimizing processes that could potentially impact natural resources. The company needed a solution that would make environmental management in many centers both feasible and efficient, simplifying performance improvement analysis, increasing visibility, and ensuring compliance with legal environmental obligations, all while utilizing only the necessary human resources.
The Solution
Toyota Spain contracted AUREN, a multidisciplinary consultancy firm specializing in Systems Standardization and Information Technology, to support the implementation of the ISO 14001 environmental regulation. AUREN adapted the environmental processes for the dealers in the Toyota Spain network and provided support prior to certification. They introduced Toyota Spain to the AuraQuantic BPMS platform, on which they modeled and automated the processes corresponding to the ISO 14001 regulation and other internal processes, resulting in the creation of the GEA-TOYOTA solution. This solution was complemented by the environmental Maintenance Compliance and Legal Requirements services provided by AUREN’s technical specialists. The Toyota Spain Environmental Administrator also received training on the application, which has been instrumental in the automation of processes and management of the system across the entire network. The entire system is now controlled by minimal staff at the Toyota Spain headquarters.
Operational Impact
Quantitative Benefit
Case Study missing?
Start adding your own!
Register with your work email and create a new case study profile for your business.
Related Case Studies.
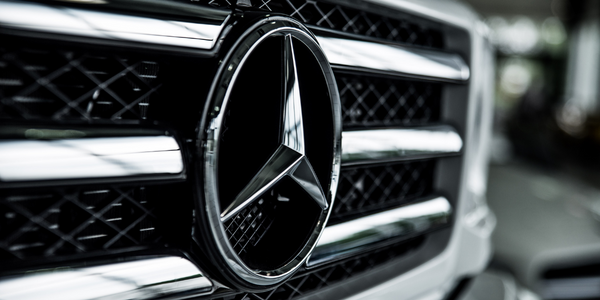
Case Study
Integral Plant Maintenance
Mercedes-Benz and his partner GAZ chose Siemens to be its maintenance partner at a new engine plant in Yaroslavl, Russia. The new plant offers a capacity to manufacture diesel engines for the Russian market, for locally produced Sprinter Classic. In addition to engines for the local market, the Yaroslavl plant will also produce spare parts. Mercedes-Benz Russia and his partner needed a service partner in order to ensure the operation of these lines in a maintenance partnership arrangement. The challenges included coordinating the entire maintenance management operation, in particular inspections, corrective and predictive maintenance activities, and the optimizing spare parts management. Siemens developed a customized maintenance solution that includes all electronic and mechanical maintenance activities (Integral Plant Maintenance).
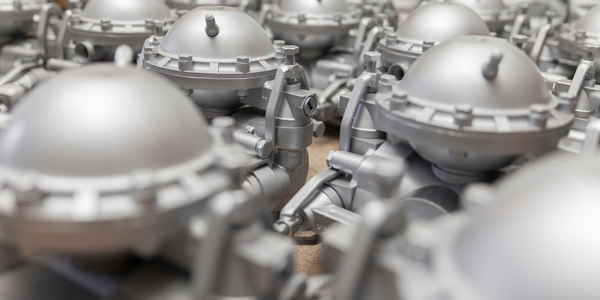
Case Study
Monitoring of Pressure Pumps in Automotive Industry
A large German/American producer of auto parts uses high-pressure pumps to deburr machined parts as a part of its production and quality check process. They decided to monitor these pumps to make sure they work properly and that they can see any indications leading to a potential failure before it affects their process.