Applicable Industries
- Cement
- Metals
Applicable Functions
- Product Research & Development
Use Cases
- Mesh Networks
- Time Sensitive Networking
Services
- Testing & Certification
- Training
About The Customer
Trek Bicycle Company, headquartered in Wisconsin, U.S.A., is a global leader in bicycle design, manufacturing, and distribution. The company boasts a rich tradition of victory in the world’s premier cycling events, including seven consecutive Tour de France titles and six straight 24-hour World Solo Championships. Trek offers a broad range of bicycles and cycling products under the Trek, Gary Fisher, LeMond, Bontrager, and Klein brand names. The company is known for its commitment to innovation, quality, and performance, leading the field with forward-thinking and next-generation technology.
The Challenge
Trek Bicycle Company, a global leader in bicycle design, manufacturing, and distribution, faced a significant challenge in maintaining its competitive edge in the industry. The company's success hinged on its ability to release innovative products that met stringent strength and stiffness requirements, all while adhering to critical product launch deadlines. A specific challenge was to expedite the market release of a cycle with an assembly composed of an aluminum steer tube bonded with epoxy adhesive into a composite fork that is bolted to the wheel axle. The complexity of the assembly and the need for precision in design and manufacturing posed a significant hurdle in meeting the desired speed to market.
The Solution
To overcome this challenge, Trek Bicycle Company turned to ANSYS Mechanical software. This advanced technology was used to accurately predict stress levels in the composite and metal fork assembly. Component geometries from SolidWorks CAD models were imported into ANSYS software, where the Virtual Topology feature was used to construct a unified mesh representing the entire assembly of composite and metal parts. The software's bonded contact elements automatically configured the mesh to account for epoxied parts, thus eliminating the need for manual adjustment of mesh densities and selection of element types. The shell lay-up capabilities of ANSYS technology were instrumental in representing the complex material properties of composites in regions containing different numbers of layers aligned in various orientations.
Operational Impact
Quantitative Benefit
Case Study missing?
Start adding your own!
Register with your work email and create a new case study profile for your business.
Related Case Studies.
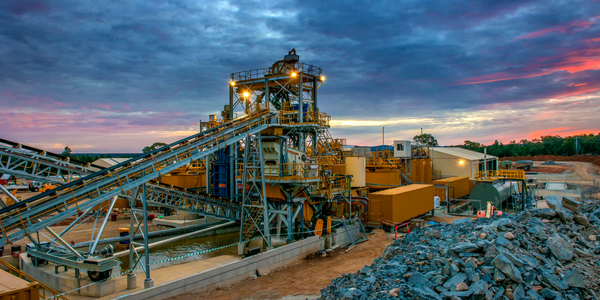
Case Study
Goldcorp: Internet of Things Enables the Mine of the Future
Goldcorp is committed to responsible mining practices and maintaining maximum safety for its workers. At the same time, the firm is constantly exploring ways to improve the efficiency of its operations, extend the life of its assets, and control costs. Goldcorp needed technology that can maximize production efficiency by tracking all mining operations, keep employees safe with remote operations and monitoring of hazardous work areas and control production costs through better asset and site management.
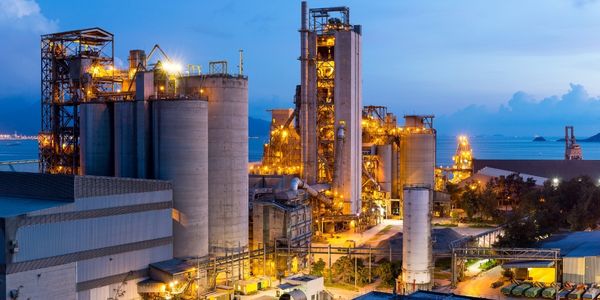
Case Study
System 800xA at Indian Cement Plants
Chettinad Cement recognized that further efficiencies could be achieved in its cement manufacturing process. It looked to investing in comprehensive operational and control technologies to manage and derive productivity and energy efficiency gains from the assets on Line 2, their second plant in India.
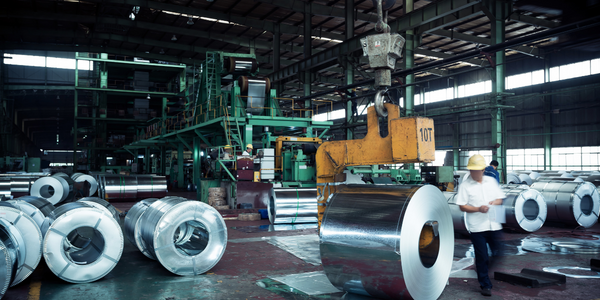
Case Study
KSP Steel Decentralized Control Room
While on-site in Pavlodar, Kazakhstan, the DAQRI team of Business Development and Solutions Architecture personnel worked closely with KSP Steel’s production leadership to understand the steel production process, operational challenges, and worker pain points.
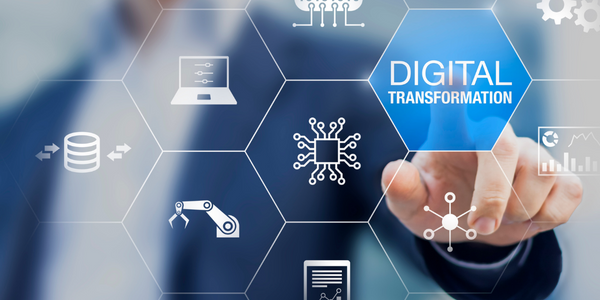
Case Study
Bluescope Steel on Path to Digitally Transform Operations and IT
Increasing competition and fluctuations in the construction market prompted BlueScope Steel to look toward digital transformation of its four businesses, including modern core applications and IT infrastructure. BlueScope needed to modernize its infrastructure and adopt new technologies to improve operations and supply chain efficiency while maintaining and updating an aging application portfolio.
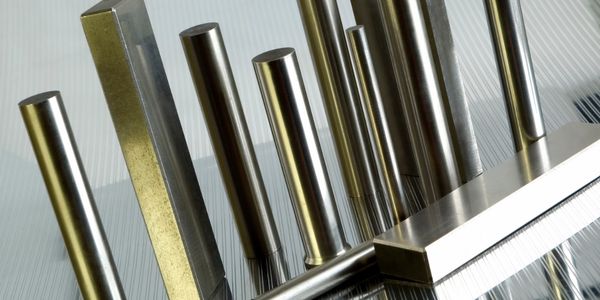
Case Study
RobotStudio Case Study: Benteler Automobiltechnik
Benteler has a small pipe business area for which they produce fuel lines and coolant lines made of aluminum for Porsche and other car manufacturers. One of the problems in production was that when Benteler added new products, production had too much downtime.
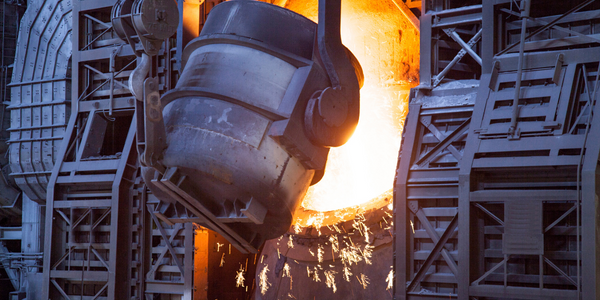
Case Study
Continuous Casting Machines in a Steel Factory
With a very broad range of applications, steel is an important material and has been developed into the most extensive alloy in the engineering world. Since delivering high quality is absolutely crucial for steel plants, ensuring maximum productivity and the best quality production are the keys to competitiveness in the steel industry. Additionally, working conditions in steel factories are not suitable for workers to stay in for long periods of time, so manufactures usually adopt various machines to complete the steel production processes. However, the precision of these machines is often overestimated and the lack of flexibility also makes supervisors unable to adjust operating procedures. A renowned steel factory in Asia planned to improve its Distributed Control System (DCS) of furnaces as well as addressing the problem of insufficient accuracy. However, most well-known international equipment suppliers can not provide a satisfactory solution and local maintenance because the project needed new technologies to more accurately control equipment operations. By implementing Advantech’s automated monitoring and control solution, steel factories can not only improve the manufacturing processes but can also allow users to add additional functions to the existing system so as to make sure the operation runs at high efficiency.