Technology Category
- Functional Applications - Manufacturing Execution Systems (MES)
- Sensors - Haptic Sensors
Applicable Industries
- Automotive
- Transportation
Applicable Functions
- Maintenance
- Quality Assurance
Use Cases
- Autonomous Transport Systems
- Transportation Simulation
Services
- Testing & Certification
- Training
About The Customer
Mobility Worldwide is a charity organization that builds and provides carts for individuals with physical disabilities in resource-poor countries where wheelchairs are neither affordable nor equipped for rural durability. These carts not only provide mobility but also offer opportunities for inventory storage for small vendors. The organization's founding site in Columbia, Missouri, is one of 30-40 affiliates worldwide and produces the majority of carts deployed across the world. The workforce at Mobility Worldwide is made up entirely of volunteers, who typically work 3-4 hours at a time.
The Challenge
Mobility Worldwide, a charity that builds carts for individuals with physical disabilities in resource-poor countries, faced significant challenges in scaling up its production. The organization aimed to double its capacity from 2000 to 4000 carts per year, but faced hurdles due to lack of standardization, absence of bills of materials, and a workforce made up entirely of volunteers unfamiliar with lean manufacturing. The Columbia site, which produces the majority of the carts, operates at only 50% utilization due to volunteers typically working 3-4 hours at a time. The organization also faced logistical challenges due to the rural locations where the carts are deployed, making it difficult to supply replacement parts. Quality assurance was another major issue, as without verification of proper builds, the charity was unable to meet the long-term needs of its recipients.
The Solution
To overcome these challenges, Mobility Worldwide implemented VKS work instruction software. The first step was to introduce work instructions, which served as a method of discovery, revealing gaps in the current state of tribal knowledge. The organization adhered to a Toyota philosophy called quality at the source, meaning that they embedded all inspection criteria into work instructions. VKS also served as a manufacturing execution system (MES), directing volunteers through the workflow and eliminating the need for a heavy-duty onboarding and training process. The organization also began to apply lean methodologies like kanban, starting from the work instructions. To address the issue of training, Kaizen teams were formed from each of the 3 departments and team members became the VKS authors, helping to standardize processes via VKS software. This significantly reduced the learning curve and training time for volunteers.
Operational Impact
Quantitative Benefit
Case Study missing?
Start adding your own!
Register with your work email and create a new case study profile for your business.
Related Case Studies.
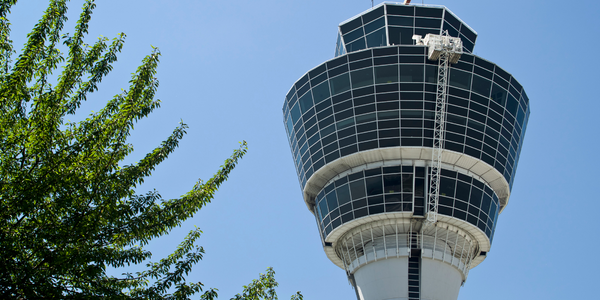
Case Study
Airport SCADA Systems Improve Service Levels
Modern airports are one of the busiest environments on Earth and rely on process automation equipment to ensure service operators achieve their KPIs. Increasingly airport SCADA systems are being used to control all aspects of the operation and associated facilities. This is because unplanned system downtime can cost dearly, both in terms of reduced revenues and the associated loss of customer satisfaction due to inevitable travel inconvenience and disruption.
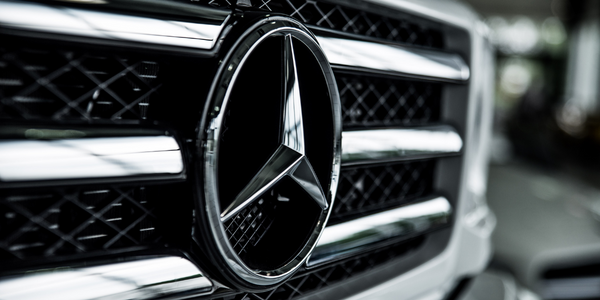
Case Study
Integral Plant Maintenance
Mercedes-Benz and his partner GAZ chose Siemens to be its maintenance partner at a new engine plant in Yaroslavl, Russia. The new plant offers a capacity to manufacture diesel engines for the Russian market, for locally produced Sprinter Classic. In addition to engines for the local market, the Yaroslavl plant will also produce spare parts. Mercedes-Benz Russia and his partner needed a service partner in order to ensure the operation of these lines in a maintenance partnership arrangement. The challenges included coordinating the entire maintenance management operation, in particular inspections, corrective and predictive maintenance activities, and the optimizing spare parts management. Siemens developed a customized maintenance solution that includes all electronic and mechanical maintenance activities (Integral Plant Maintenance).
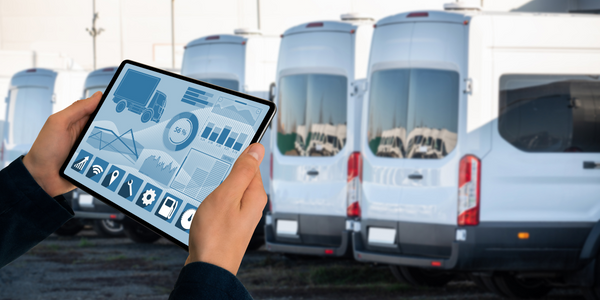
Case Study
IoT-based Fleet Intelligence Innovation
Speed to market is precious for DRVR, a rapidly growing start-up company. With a business model dependent on reliable mobile data, managers were spending their lives trying to negotiate data roaming deals with mobile network operators in different countries. And, even then, service quality was a constant concern.
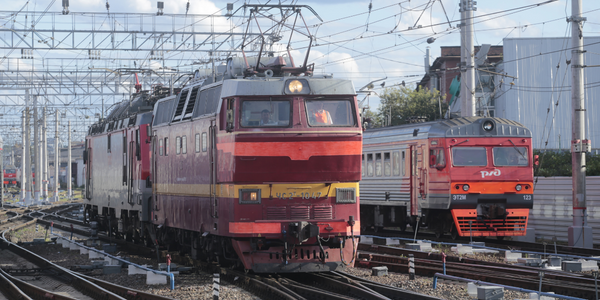
Case Study
Digitize Railway with Deutsche Bahn
To reduce maintenance costs and delay-causing failures for Deutsche Bahn. They need manual measurements by a position measurement system based on custom-made MEMS sensor clusters, which allow autonomous and continuous monitoring with wireless data transmission and long battery. They were looking for data pre-processing solution in the sensor and machine learning algorithms in the cloud so as to detect critical wear.
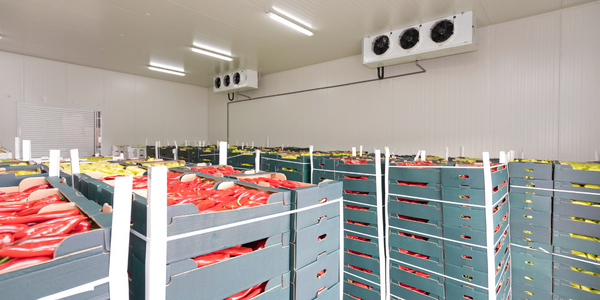
Case Study
Cold Chain Transportation and Refrigerated Fleet Management System
1) Create a digital connected transportation solution to retrofit cold chain trailers with real-time tracking and controls. 2) Prevent multi-million dollar losses due to theft or spoilage. 3) Deliver a digital chain-of-custody solution for door to door load monitoring and security. 4) Provide a trusted multi-fleet solution in a single application with granular data and access controls.