Customer Company Size
Large Corporate
Region
- America
Country
- United States
Product
- myVW mobile app
- Google Cloud Vertex AI
- Gemini models
Tech Stack
- Generative AI
- Machine Learning
- BigQuery
Implementation Scale
- Enterprise-wide Deployment
Impact Metrics
- Customer Satisfaction
- Digital Expertise
Technology Category
- Analytics & Modeling - Generative AI
- Platform as a Service (PaaS) - Data Management Platforms
- Application Infrastructure & Middleware - API Integration & Management
Applicable Industries
- Automotive
Applicable Functions
- Product Research & Development
- Business Operation
Use Cases
- Digital Twin
- Remote Asset Management
- Predictive Maintenance
Services
- Software Design & Engineering Services
- System Integration
About The Customer
Volkswagen of America, Inc. (VWoA) is a prominent operating unit of Volkswagen Group of America, a subsidiary of Volkswagen AG. Headquartered in Reston, Virginia, VWoA is responsible for selling a range of vehicles, including the Atlas, Atlas Cross Sport, Golf GTI, Golf R, ID.4, Jetta, Jetta GLI, Taos, and Tiguan, through more than 600 independent U.S. dealers. The company operates a state-of-the-art assembly facility in Chattanooga, Tennessee, where it produces Volkswagen brand vehicles such as the Atlas, Atlas Cross Sport, and the ID.4. As part of the global Volkswagen Group, one of the world's largest producers of passenger cars and Europe's largest automaker, VWoA is committed to delivering high-quality vehicles and innovative solutions to its customers. The company is focused on leveraging advanced technologies to enhance the driving experience and provide exceptional customer service.
The Challenge
Volkswagen of America faced the challenge of providing vehicle owners with intuitive access to critical vehicle information and services. The company aimed to enhance the user experience by integrating advanced AI capabilities into their myVW mobile app. This required a strategic partnership with a technology provider that could offer industry-leading AI and machine learning capabilities. The goal was to create a virtual assistant that could deliver accurate and low-latency information to users, allowing them to easily access vehicle manuals and receive answers to specific questions about their vehicles. Additionally, Volkswagen needed to ensure that the app met specific legal requirements and high standards while delivering an innovative and user-centric experience.
The Solution
Volkswagen partnered with Google Cloud to integrate generative AI capabilities into the myVW mobile app. This collaboration involved leveraging Google Cloud's industry-leading AI and machine learning capabilities, as well as expertise from Google Cloud Consulting, to develop the myVW Virtual Assistant. The assistant combines Volkswagen's connected car data with Gemini models on the Google Cloud Vertex AI platform, enabling it to deliver low-latency, accurate information to users. The app allows MY24 Atlas and Atlas Cross Sport owners to explore their vehicle manuals and ask questions specific to their vehicles. Users can also utilize Gemini's multi-modal capabilities to receive helpful information by pointing their smartphone camera at their dashboards. The integration of Google Cloud Vertex AI and BigQuery allows Volkswagen to ground and tune Gemini models on multiple data sources, including vehicle owner manuals, frequently asked questions, help center articles, official Volkswagen YouTube videos, and step-by-step guides. Google Cloud Consulting provided comprehensive support throughout the app development process, ensuring that the app met Volkswagen's legal requirements and high standards while delivering an innovative and user-centric experience.
Operational Impact
Quantitative Benefit
Case Study missing?
Start adding your own!
Register with your work email and create a new case study profile for your business.
Related Case Studies.
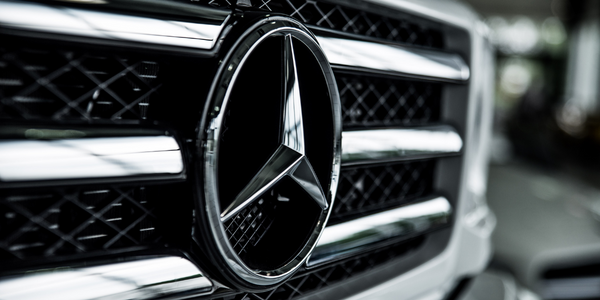
Case Study
Integral Plant Maintenance
Mercedes-Benz and his partner GAZ chose Siemens to be its maintenance partner at a new engine plant in Yaroslavl, Russia. The new plant offers a capacity to manufacture diesel engines for the Russian market, for locally produced Sprinter Classic. In addition to engines for the local market, the Yaroslavl plant will also produce spare parts. Mercedes-Benz Russia and his partner needed a service partner in order to ensure the operation of these lines in a maintenance partnership arrangement. The challenges included coordinating the entire maintenance management operation, in particular inspections, corrective and predictive maintenance activities, and the optimizing spare parts management. Siemens developed a customized maintenance solution that includes all electronic and mechanical maintenance activities (Integral Plant Maintenance).
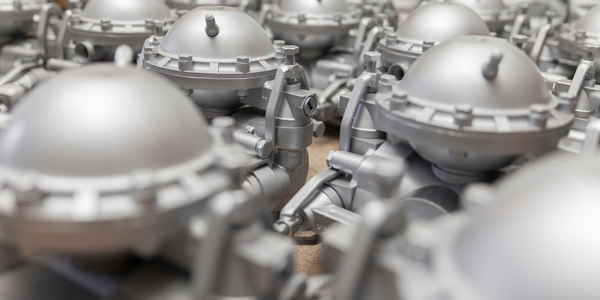
Case Study
Monitoring of Pressure Pumps in Automotive Industry
A large German/American producer of auto parts uses high-pressure pumps to deburr machined parts as a part of its production and quality check process. They decided to monitor these pumps to make sure they work properly and that they can see any indications leading to a potential failure before it affects their process.